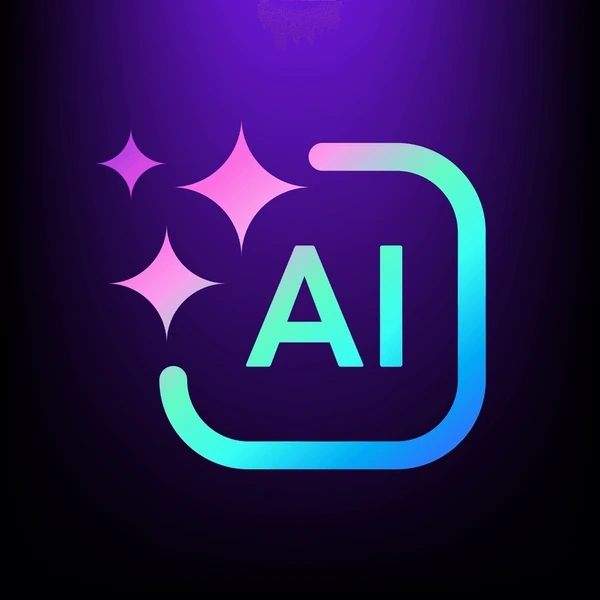
Smarter email, faster business.
How Aircraft Weight Reduction Curbs Fuel Costs (And Which Parts Can Be Replaced to Reduce Weight)
July 03, 2025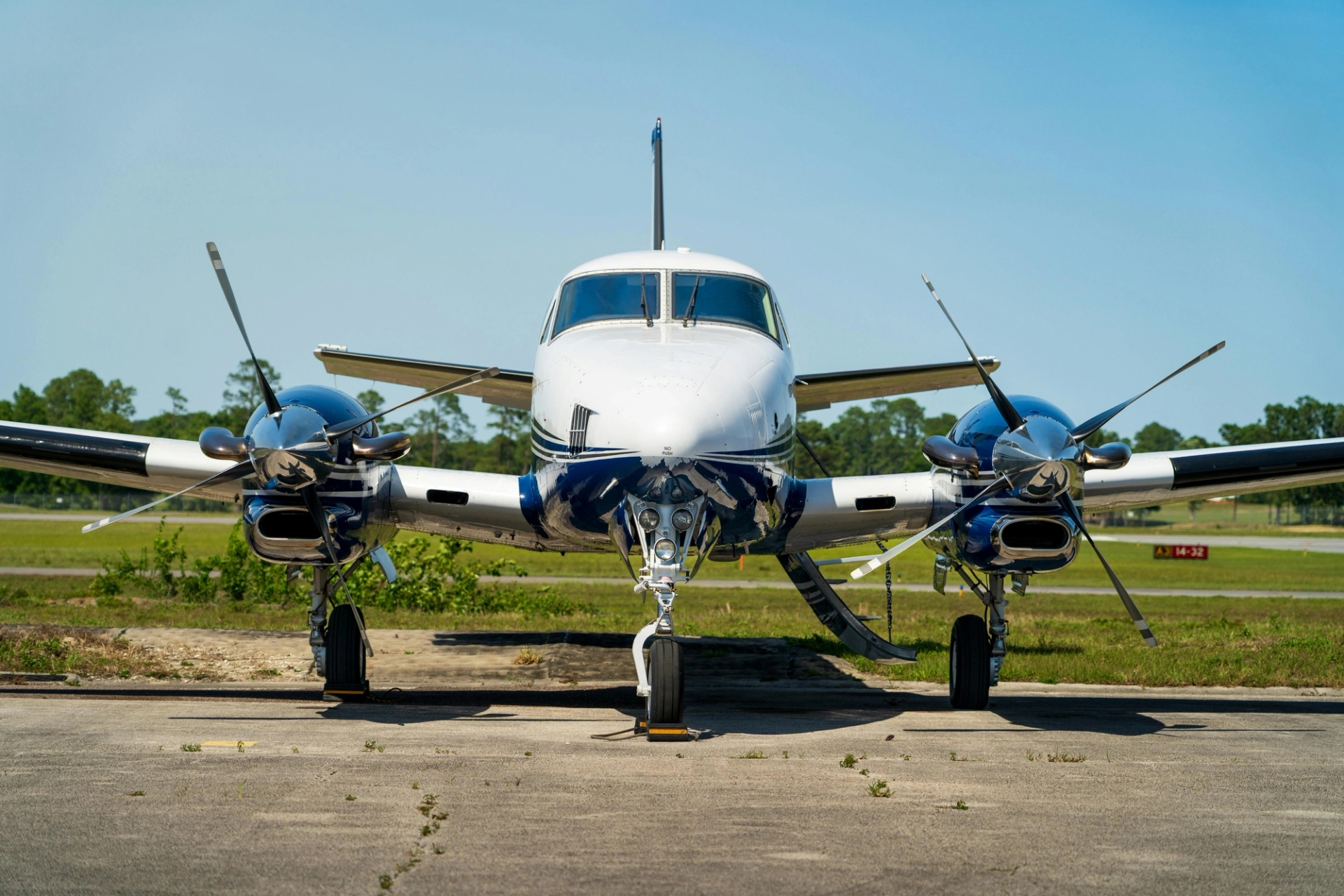
Making weight. Discover how airlines are dropping pounds to trim the bulk and CO₂ emissions — shedding one seat, cart, and connector at a time.
Fuel is the single largest operating expense for most airlines, and every extra pound on board burns through more of it. In an industry under pressure from tariffs, tightening emissions regulations, and sustainability targets like the IEA’s net-zero by 2050, weight reduction is crucial for curbing costs and maintaining compliance (International Energy Agency).
Fleets need to shed pounds and make weight.
Airlines, manufacturers, and research consortia have all fallen in line, exploring solutions like upgrading outdated materials, rethinking cabin layouts, and even redesigning toilet flows. This article explores how aircraft weight reduction lowers fuel costs and carbon emissions, and exactly which parts are getting lighter to make it happen.
The link between aircraft weight and fuel consumption
The relationship is direct and unforgiving: The heavier the aircraft, the more fuel it needs to get off the ground and stay in the air. Weight increases fuel burn, and more fuel adds more weight in a compounding cycle that engineers and operations teams work hard to break.
A widely cited benchmark shows that for every 1% drop in aircraft weight, fuel use falls by about 0.75% (Dynamic Metals). For a long-haul commercial jet, that can translate into 300,000 liters (~ 79,252 gallons) of fuel saved per year, cutting CO₂ emissions by roughly 750 metric tonnes (~827 short tons), per plane fuel cost savings of $475,000.
Weight is also tightly regulated for safety. The FAA Pilot’s Handbook of Aeronautical Knowledge warns that overloading or mismanaging aircraft weight and balance can reduce lift, impair climb rates, shorten range, and even make it difficult to land safely (FAA).
And then there’s the weight of the fuel itself. Aviation gasoline (Avgas) weighs roughly 6 to 7 pounds per gallon, and Jet A (kerosene-based fuel) even more (Sunoco, Foreflight). That means adding 30 gallons of fuel can add more weight than a full-grown passenger—fueling becomes its own weight-balance calculation (FAA).
Key benefits of weight reduction
Weight reduction has tangible, bottom-line, and environmental payoffs.
Operationally, a lighter aircraft improves nearly every performance metric: shorter takeoff rolls, steeper climb angles, higher cruising speeds, and lower stall speeds.
Excess weight, however, shortens flight ranges, lowers maximum altitudes, and increases landing speed, all of which chip away at aircraft performance and safety (FAA).
Environmentally, trimming aircraft weight is one of the most straightforward ways to slash emissions. According to Dynamic Metals, even minimal reductions in aircraft weight drive big wins for the environment. A 1% reduction in weight is about the same as eliminating emissions from 160 vehicles on the road per year (Dynamic Metals).
Weight reduction also aligns with global climate targets. The CAELESTIS Project, funded under the EU’s Horizon Europe program, has committed to reducing fuel burn and emissions by 30% by advancing lightweight materials and designs (CAELESTIS Project). These improvements help aviation comply with the European Green Deal and the Paris Agreement while supporting the International Energy Agency’s (IEA) broader roadmap to net-zero emissions by 2050 (European Commission, United Nations Framework Convention on Climate Change).
Replaceable aircraft parts and systems that cut weight
Structural and component materials
One of the most effective ways to reduce an aircraft's weight is by shifting its core materials. Advanced metals like aluminum-lithium alloys can reduce component weight by up to 10%, while titanium is increasingly replacing steel in landing gear and engine parts due to its improved strength-to-weight ratio (Dynamic Metals).
CAELESTIS is also pioneering the use of composite materials and virtual prototyping to build lighter, safer structures. Digital twin technology allows engineers to simulate performance in real-time, optimizing materials for weight efficiency in different flight scenarios without sacrificing durability (CAELESTIS Project).
Even small substitutions, such as using composite wiring and connectors, AL-LI alloys, or chromate-free paint, can shed hundreds of pounds. One workshop presentation from Bombardier Aerospace outlined how these seemingly minor changes, when combined, can reduce weight by over 3,000 pounds (International Civil Aviation Organization).
Interiors and cabin systems
Cabin design is one of the most overlooked sources of weight, and also one of the easiest to optimize. Airlines are replacing traditional seating with lightweight options. Iberia’s Airbus A350s, for example, use ultra-light Recaro seats that significantly improve the aircraft’s environmental profile (Aviation Week, Recaro).
Beverage service carts are another surprising weight sink. Japan’s All Nippon Airways (ANA) swapped out its old metal carts for new lightweight models that are up to 10 kg (22 pounds) lighter each. With numerous carts onboard a single Boeing 777-300ER, the weight savings totaled roughly 580 kg (~1,270 pound) per aircraft. Across its fleet, ANA estimates this change alone cuts 5,700 tons of fuel use annually—eliminating the CO₂ equivalent of 17,500 Olympic swimming pools. In terms of cost, that’s a savings of 11.4 million gallons of gas per year, or $10.2 million in fuel (All Nipon Airways).
Other changes are smaller but add up: chromate-free paint (-150 lbs), lighter carpets (-125 lbs), and composite air ducts (-11 kg) all contribute to meaningful reductions (International Civil Aviation Organization, Aviation Week).
Diehl Aviation is even designing integrated lavatory-galley units that save space and reduce weight, freeing up room for 12 more passenger seats while trimming excess structural mass (Aviation Week, Diehl Aviation Group).
Service and operational supplies
Not all weight savings require physical redesigns. Sometimes it's about what you bring aboard, and how much of it.
Iberia now tailors how much water is loaded on each flight, reducing unnecessary weight from overfilled tanks. Its A350s use a system that limits lavatory faucet flow to just five seconds per use, compared to 10 seconds on older models (Aviation Week).
Diehl’s Greywater Reuse System goes a step further. It recycles water from lavatory sinks to flush toilets, allowing airlines to reduce freshwater loads. This change offers a potential savings of up to 210 kg per long-haul flight and nearly 90 tons of CO₂ emissions per year, per aircraft (Aviation Week, Diehl Aviation Group).
Digital manuals and paperless cockpits are also cutting weight. ANA and Iberia both eliminated printed materials, in-flight magazines, and paper manuals, replacing them instead with tablets and apps for pilots and crew (All Nipon Airways, Aviation week, Grupo Iberia).
Innovations in weight management
While hardware swaps can deliver fast wins, airlines and manufacturers are also investing in other long-term weight management strategies.
Digital twins and virtual prototyping are at the forefront. These tools simulate aircraft performance under diverse real-world conditions, allowing engineers to optimize structural design, material placement, and load distribution without overbuilding for every worst-case scenario.
CAELESTIS uses this technology to reduce structural weight while maintaining safety, paving the way for aircraft that are both stronger and lighter (CAELESTIS Project).
Center of gravity (CG) optimization is another area of focus. Flying with an aft CG reduces trim drag, which in turn lowers fuel burn. This can be achieved by redesigning internal fuel burn sequences, moving heavy equipment aft (toward the rear tail of the aircraft), or even adjusting passenger seating configurations (International Civil Aviation Organization).
Smarter material science is also allowing the aviation industry to push weight-reduction boundaries. The aerospace sector is exploring self-healing alloys, ultra-light metals that rival composites, and smart materials that respond to flight conditions. These innovations could extend part life, reduce maintenance downtime and repair cycles, and offer better recycling outcomes in the long term (Dynamic Metals, Reuters).
Real-world case studies
The weight savings may sound small, but scaled across fleets, the results are massive.
Southwest Airlines retrofitted cabin interiors and saved 6 million gallons of fuel in one year. That’s a savings of roughly $36 million per year (Southwest Airlines One Report).
Adopting similar green measures, United Airlines upcycled over 700 seat bottoms, 900 seat backs, and 1,000 headrests into consumer goods—conserving 3.4 million gallons of water and avoiding hundreds of pounds of landfill waste (Aviation Week).
American Airlines took a multipronged approach: lighter seats, new brake systems, minimal ice stockpiles, and even lighter paint jobs. Together, these measures save 12.4 million gallons of fuel annually (roughly $74.4 million in fuel costs) and eliminate 117,800 metric tons of CO₂ emissions (Aviation Week, American Airlines Environmental, Social, and Governance Report).
Additionally, LATAM Airlines has committed to removing all single-use plastics, expecting to cut 1,000+ tons annually, and Air Canada participates in wide-scale recycling and redistribution of unused amenity kits, blankets, and uniforms (Aviation Week, LATAM Airlines, Air Canada Media Centre).
Challenges and trade-offs
Despite the clear benefits, weight reduction comes with trade-offs. The most obvious: upfront costs. Advanced metals like titanium or aluminum-lithium alloys are significantly more expensive than traditional materials. While these investments pay off over time through fuel savings and lower maintenance, the initial price tag can be a barrier, especially for smaller carriers operating on tight margins (Dynamic Metals).
There are also operational challenges. When ANA introduced lighter service carts, this altered the center of gravity and affected how the carts handled. As a result, a change as minor as new beverage carts required crew retraining and work adjustments (All Nippon Airways). Even the weight of cutlery and seat fabrics can subtly shift an aircraft's balance, potentially increasing trim drag or affecting stability.
Regulatory constraints can also block certain innovations. For instance, replacing windshield wipers with rain-repellent coatings could shave off 24 pounds per aircraft, but this efficiency upgrade hinges on updates to FAA regulations (International Civil Aviation Organization).
Finally, the passenger experience can’t be ignored. Airlines must balance sustainability with comfort and brand expectations. Iberia, for example, switched to digital magazines but still chose to keep printed menus, knowing not all passengers are digital-first travelers (Aviation Week).
The future of aircraft weight reduction
Aircraft weight reduction isn’t a one-and-done initiative. It’s both a process and a strategy, continually evolving to meet environmental, governmental, and market demands. As such, weight reduction is built into every phase of the design and operational lifecycle.
Future gains will likely come from next-gen materials that are not only lighter but smarter: think alloys that respond to stress, composites that heal themselves, and recycled metals that still retain full performance capabilities.
Manufacturers like those involved in the CAELESTIS Project are also integrating digital engineering into every component, testing designs virtually to design for optimal weight distribution and minimal material use (CAELESTIS Project).
Retrofitting existing fleets will also be critical. Winglets, lighter interiors, and upgraded avionics are all viable for older aircraft. And with sustainability reporting increasingly baked into corporate ESG strategies, airlines that ignore weight reduction will face increased costs and reputational risks.
To fully achieve aircraft weight reduction, supply chain collaboration is key, which relies on suppliers creating more eco-conscious components, from passenger seats to soap dispensers. Airlines, thus, will be able to make weight-saving swaps faster and at lower cost.
Looking ahead
Aircraft weight reduction isn’t just about better aerodynamics, sleeker design, and advanced metal alloys. It’s about finding and incorporating all possible ways to help aircraft shed excess pounds. Every ounce saved cuts fuel costs, lowers emissions, and future-proofs fleets against tightening climate regulations.
From material science breakthroughs to rethinking how water flows in an airplane lavatory, the aviation industry is proving that the path to sustainability is paved in small, bit-by-bit wins. Whether it’s new composite seats, recycled cabin materials, or optimized flight loads, each small decision adds up to tremendous environmental and monetary gains.
Ready to reduce fuel burn, emissions, and compliance risk without compromising performance? ePlaneAI helps manufacturers, MROs, and fleet operators identify high-impact opportunities for aircraft weight reduction across components, systems, and operational workflows. With advanced modeling tools for aircraft weight and balance, real-time performance insights, and predictive analytics around aircraft fuel weight, our platform supports lighter, smarter, and more sustainable flight.
Book a demo to see how ePlaneAI can help your fleet make weight, cut costs, and stay compliant, one smarter decision at a time.
Aviation Maintenance Trends That May Gain Momentum in Uncertain Circumstances
Aircraft are staying in service longer, supply chains are a powder keg, and the tech is evolving overnight. Discover the maintenance trends gaining momentum and what they mean for operators trying to stay airborne and profitable.
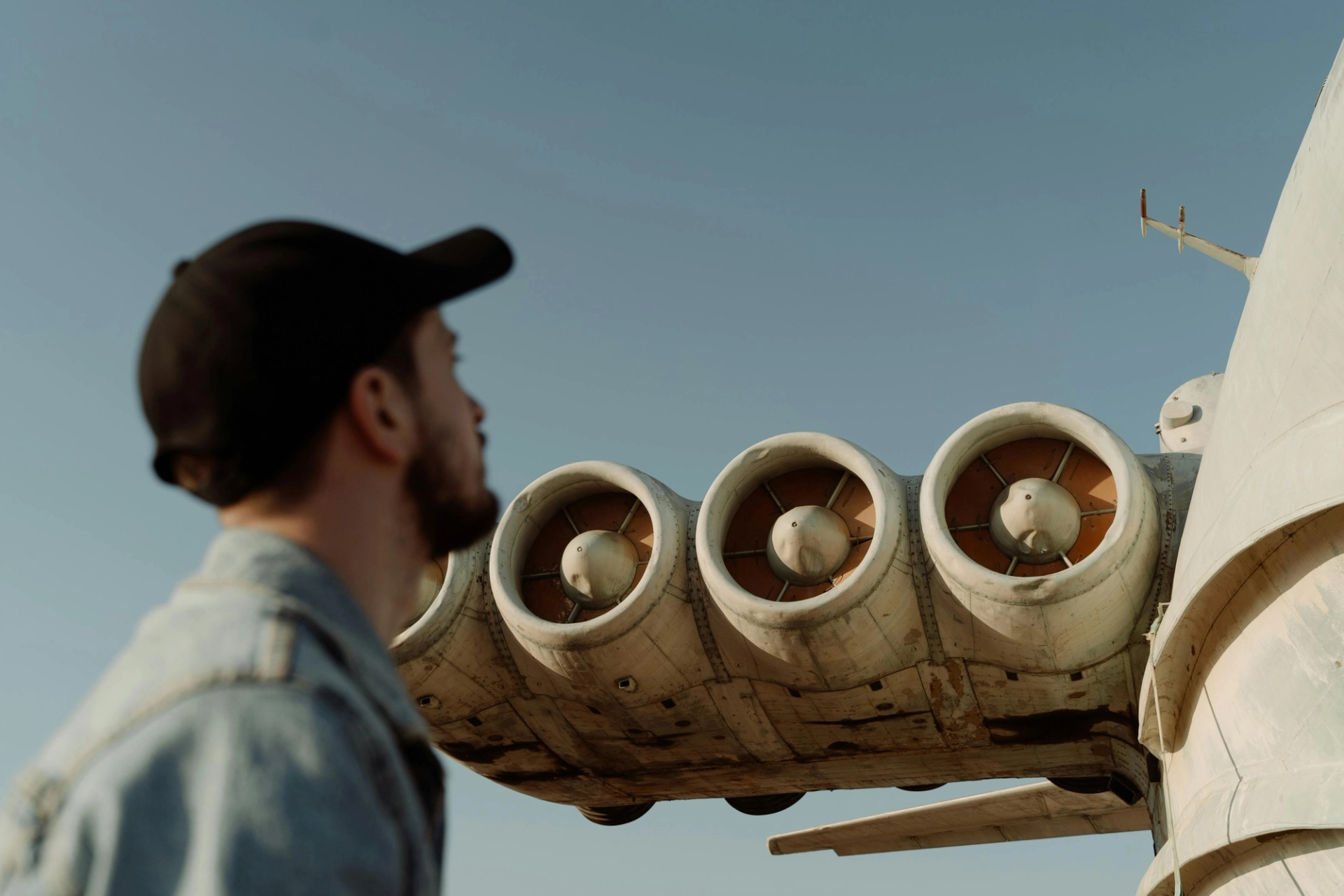
August 27, 2025
How to Use AeroGenie to Streamline Procurement Reporting in Aviation
What makes AI tools understand human language? It’s not magic—it’s NLP. Learn how NLP works, where it's going, and how it's changing the way we query and build reports with AI.
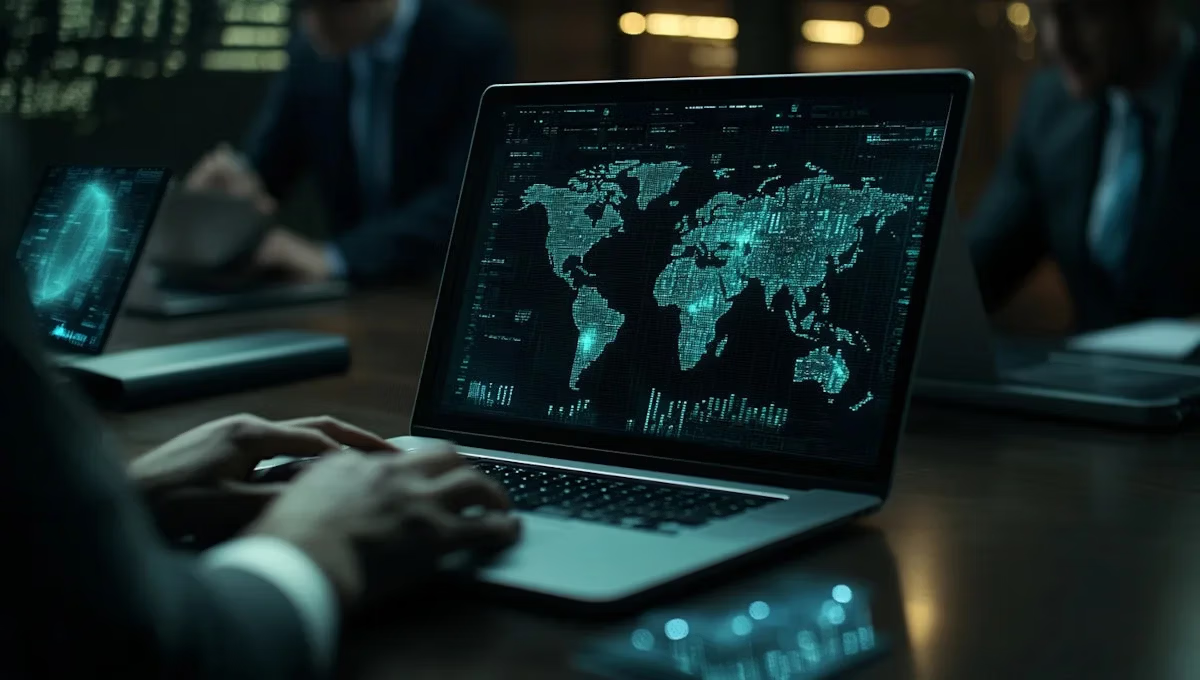
August 25, 2025
What Is Parts Manufacturer Approval (PMA) and Why Is It Important in Aviation?
PMA parts are transforming aviation—cutting costs, improving performance, and reducing downtime. Learn why FAA-approved PMA components are becoming a go-to choice for airlines, MROs, and OEMs alike.
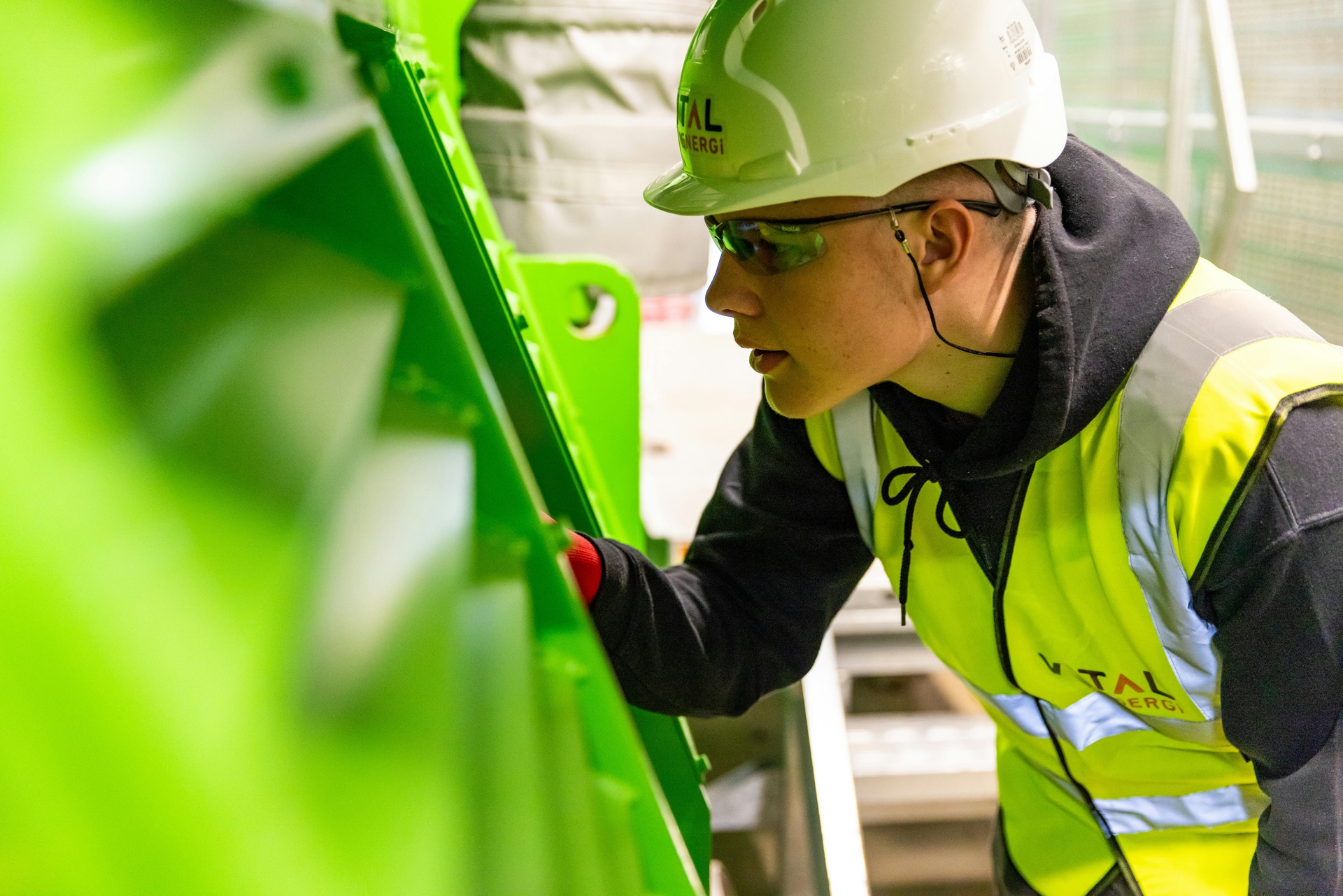
August 22, 2025
How to Manage Your Aircraft Maintenance Team With Schedule AI
Tired of manual maintenance scheduling headaches? Meet Schedule AI. See how Schedule AI is transforming aircraft operations, helping your team optimize tasks and drastically cut down turnaround times. Keep your fleet in the air and on schedule.
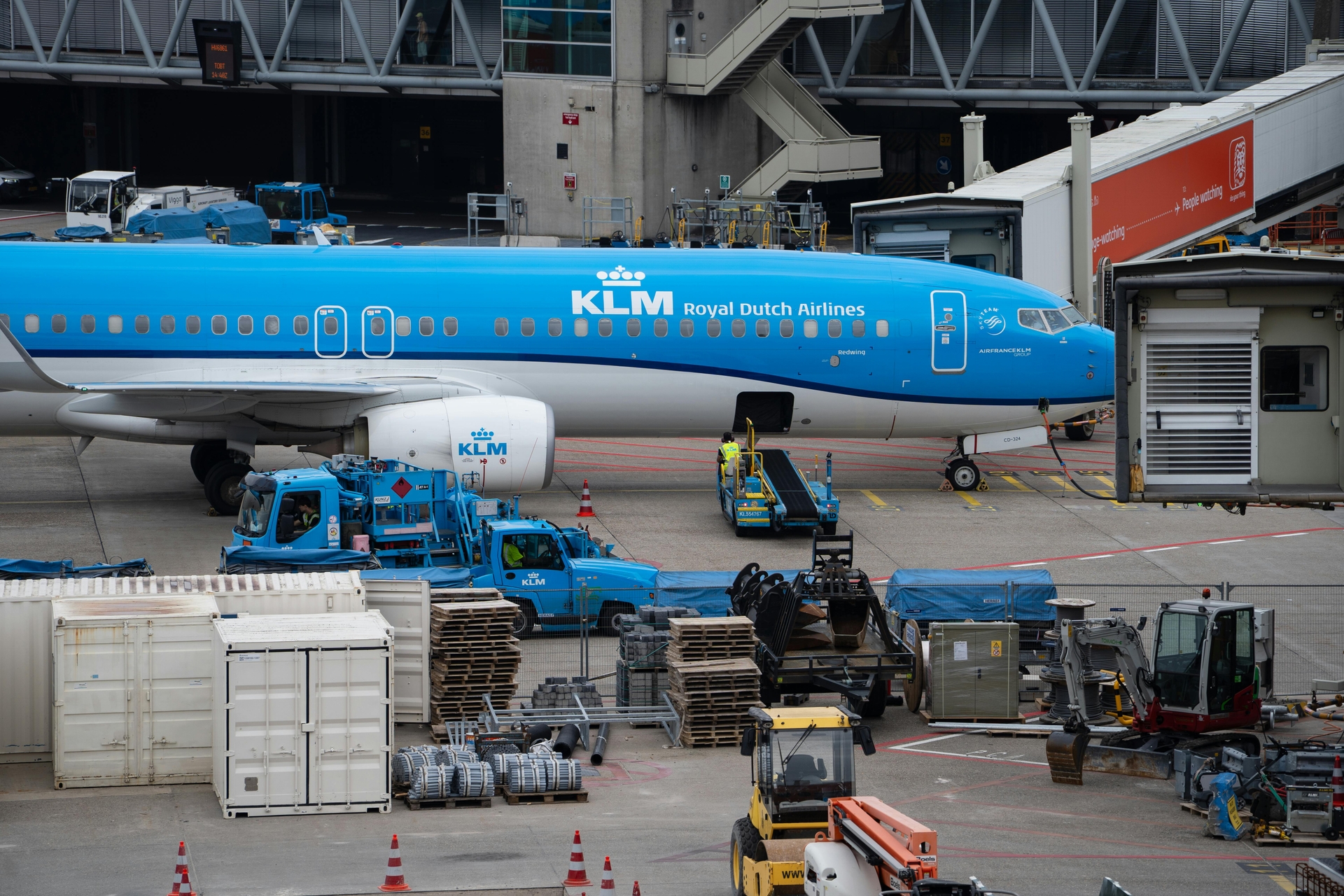