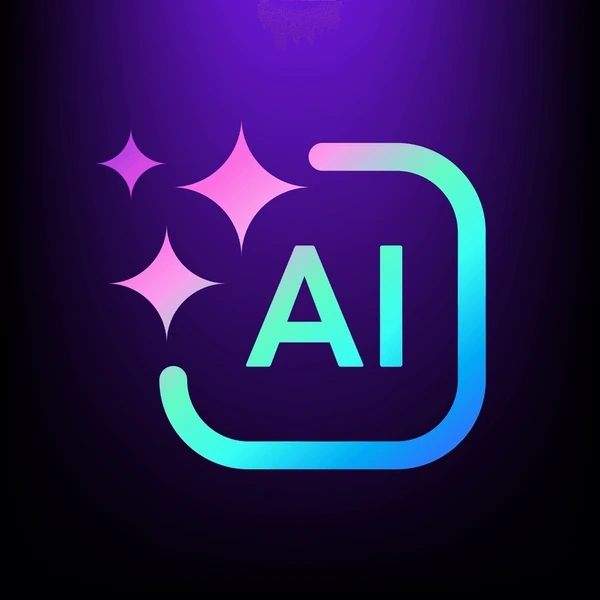
Smarter email, faster business.
Why AI-Integrated ERP Systems Are Essential for the Modern Aviation Industry
April 10, 2025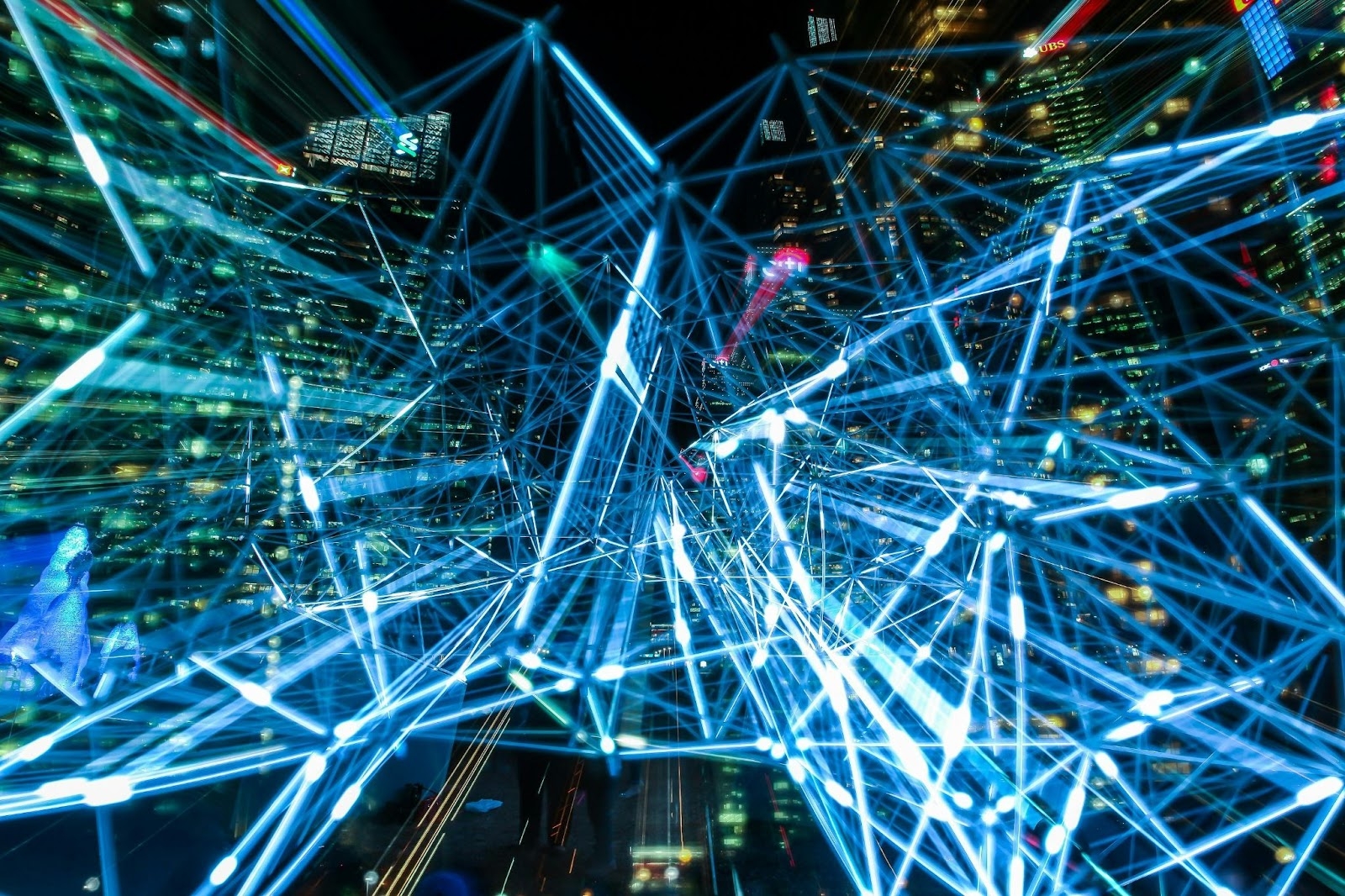
Discover how AI ERP systems are becoming indispensable for modern aviation—integrating predictive maintenance, streamlining supply chains, and keeping fleets flying on time.
Flying has always been difficult. Launching objects and people in the air, on a controlled trajectory, has never been easy. And at present, the aviation industry is navigating one of its most complex eras yet. Airlines are tasked with keeping more planes in the sky, and for longer periods, while managing labor shortages, global supply chains, and rising costs—all while maintaining strict safety standards. It’s a high-wire act with no room for error.
Helping aviation companies meet the challenge: AI ERP systems. These next-generation technology platforms combine enterprise resource planning (ERP) with artificial intelligence.
For airlines, AI ERP platforms unify operational data from across maintenance, supply chain, inventory, and flight operations into one single, intelligent system. Instead of working in silos or reacting after the fact, AI ERP empowers real-time, predictive insights that keep aircraft flying and passengers moving.
In this article, we’ll unpack why AI-integrated ERP systems are essential for modern aviation companies. We’ll explore how these systems enhance predictive maintenance, strengthen supply chain resilience, boost workforce productivity, and help airlines overcome industry-specific challenges. Plus, we’ll outline how airlines and MRO providers can take practical steps toward AI ERP adoption today.
The complexity of aviation operations today
Modern aviation is a marvel of coordination—mired in complications. Airlines are juggling labor shortages, rising operational costs, supply chain disruptions, and the lingering effects of the COVID-19 pandemic. Each of these factors alone is a monumental obstacle, but together, they create a perfect storm of inefficiency and lost profits.
Start with the labor crunch. Since 2019, hourly wages for aircraft technicians and maintenance engineers have jumped by more than 20%, a sharp rise driven by high demand and limited supply of skilled workers. By 2033, projections suggest that one-fifth of aviation maintenance technician jobs could go unfilled, compounding the strain on existing teams. Add to that the backlog of deferred maintenance from the pandemic era. Airlines, faced with grounded fleets and reduced revenue, delayed non-essential maintenance. Now, as travel demand rebounds, those deferred tasks are catching up fast, increasing the risk of unscheduled downtime and escalating maintenance pressures.
Finally, legacy systems are holding operators back. Many airlines still rely on fragmented platforms, outdated PDFs, and manual data entry, making it difficult to access real-time insights across departments.
Without integrated tools, maintenance, supply chain, and operational teams are forced to work in silos—leading to missed signals and costly delays..
These complexities set the stage for why AI ERP systems are not just beneficial but absolutely critical for modern aviation.
What AI ERP brings to aviation: Unified data, smarter decisions
In an industry where fragmented information can ground a fleet, AI ERP systems act as a unifying force. They bring together maintenance logs, procurement schedules, inventory data, flight operations, and even technician notes into a single, cohesive platform. This consolidation creates a living, breathing operational brain for the airline.
AI ERP systems go beyond merely storing data. They actively analyze both structured information, like inventory counts and supplier contracts, and unstructured data, such as maintenance reports and handwritten technician notes. With AI integration, the system can surface actionable insights that would otherwise get buried in spreadsheets and siloed systems.
One standout example is how AI copilots are transforming maintenance workflows. Rather than digging through PDFs or outdated records, technicians can ask simple, natural-language questions—“When and where was this part last replaced?” or “What’s the failure rate of this component?”—and the AI delivers precise answers instantly.
The benefits extend to procurement and inventory management as well. AI ERP platforms continuously monitor parts usage trends and predict future demand, helping aviation companies avoid both shortages and excess stock. This predictive capability allows teams to align maintenance schedules with supplier lead times, keeping critical components flowing when and where they’re most needed.
In short, AI ERP systems transform data from a passive record-keeping function into a dynamic decision-making engine.
Predictive maintenance meets AI ERP
Predictive maintenance has already driven major efficiency gains for aviation, but when it’s integrated with AI ERP systems, it becomes even more powerful. Take Delta’s use of the Airbus Skywise platform, which boasts a predictive success rate of over 95% for identifying pending failures (Delta Tech Ops). Integrating this kind of predictive insight directly into an AI ERP system allows maintenance schedules, parts procurement, and workforce assignments to automatically adjust in real time.
Without AI ERP, predictive maintenance insights might exist in a separate system—still valuable but much less helpful, living disconnected from day-to-day operational workflows. With integration, however, AI-generated forecasts flow seamlessly into maintenance calendars and inventory management tools, ensuring parts and technicians are available well before failure occurs.
Generative AI adds another layer of intelligence. These systems can automatically summarize fault histories, recommend preventative actions, and even generate work orders to address issues before they escalate. Instead of reacting to problems, airlines become proactive—anticipating needs and orchestrating maintenance activity with surgical precision.
Perhaps most critically, AI ERP closes the loop between predictive insights and supply chain readiness. If a critical component shows signs of early wear, the system can immediately check stock levels, reorder parts, and update supplier timelines, helping ensure that nothing delays the repair.
In short, airlines connecting predictive maintenance with ERP workflows build a smarter, more responsive maintenance ecosystem—one where unscheduled downtime becomes the rare exception, not the inevitable, occasional occurrence.
AI ERP strengthens supply chain resilience
Aviation supply chains are notoriously complex, spanning millions of parts, dozens of vendors, and countless variables, such as weather disruptions and global shortages. When a single weak link breaks, the consequences ripple across the entire operation.
AI-powered ERP systems continuously analyze communication flows, shipment data, and supplier performance to identify early warning signs of disruption.
If a delivery is delayed or a vendor faces production issues, the system flags the risk in advance, giving procurement teams time to secure alternative sources or adjust maintenance schedules.
These AI-enhanced control towers offer cross-functional visibility, helping ensure maintenance, inventory, and supply chain teams operate from the same real-time data with a unified view of parts availability, lead times, and repair needs.
AI ERP systems also improve external collaboration. Airlines sharing demand forecasts and parts requirements with suppliers can reduce the risk of stockouts and production bottlenecks. Suppliers equipped with better insights can align their output to meet airline needs, strengthening the entire ecosystem.
And there’s a bonus: AI ERP reduces the administrative burden of reconciling supplier records and managing manual purchase orders. Automated systems handle these tasks with speed and accuracy.
AI ERP improves workforce productivity and upskilling
The aviation workforce is under immense pressure. Experienced technicians are retiring, labor shortages are deepening, and junior staff need to get up to speed—fast. AI ERP systems play a pivotal role in bridging this gap, enhancing productivity while supporting the upskilling of new talent.
AI copilots integrated into ERP systems guide technicians through troubleshooting tasks, reducing reliance on trial and error. These systems have already demonstrated their effectiveness in other industries, slashing troubleshooting time by 35% and cutting repair times by 25%.
Just as important, AI ERP platforms capture and distribute institutional knowledge. Virtual assistants help junior technicians by providing step-by-step repair guidance, referencing past maintenance records, and suggesting proven solutions.
This democratization of expertise ensures that less experienced team members can perform at a high level, reducing dependency on a shrinking pool of seasoned experts.
Beyond the hangar floor, AI ERP automates much of the clerical workload associated with maintenance—generating work orders, updating logs, and filing compliance documentation automatically.
In essence, AI ERP is becoming the digital backbone of workforce development, helping airlines train, retain, and maximize the productivity of their teams—even in a labor-constrained environment.
Barriers to AI ERP adoption in aviation (and how to overcome them)
Despite its immense potential, integrating AI ERP systems in aviation isn’t a simple plug-and-play operation. Airlines face a unique combination of legacy systems, regulatory scrutiny, and cultural challenges that can slow down digital transformation.
First, legacy infrastructure remains a major barrier. Many airlines still rely on fragmented, outdated systems with manual inputs and static PDF records. Before AI ERP can work its magic, airlines need to modernize their data environments—digitizing records and connecting diverse systems so that they can “speak” to each other.
Next, there’s the unavoidable issue of safety-critical environments. Commercial aviation has zero tolerance for error. AI must augment human expertise, not replace it. Any recommendation made by an AI ERP system needs human verification, especially for mission-critical maintenance decisions.
Explainable AI (XAI) plays an essential role here. By making AI-generated insights transparent and understandable, XAI helps build trust with maintenance crews, engineers, and leadership alike When teams understand how the system reaches its conclusions, they’re far more likely to rely on and validate (before implementing) the recommendations.
There’s also the human element of change management. Successful AI ERP deployment depends on workforce engagement across departments. Airlines that foster collaboration between tech teams, maintenance crews, and procurement professionals will accelerate adoption and maximize results.
Overcoming these barriers is possible—and essential. With thoughtful planning, airlines can future-proof their operations and bridge the gap between existing ERP systems and next-generation AI.
Getting started with AI ERP: Steps for airlines and MROs
The path to AI ERP adoption doesn’t have to be overwhelming. Aviation companies and MRO providers can take clear, manageable steps to build momentum and prove value early in the process.
Start by targeting high-impact, low-risk use cases. For instance, using AI ERP for inventory forecasting or maintenance scheduling provides quick wins without heavy regulatory hurdles. These pilots help demonstrate the system’s potential and build organizational confidence.
Next, ensure your data foundation is solid. AI ERP systems thrive on clean, connected data. Aviation companies must invest in digitizing legacy records and building a centralized data infrastructure that feeds the ERP’s intelligence engines.
Workforce training is equally critical. Delta’s success with predictive maintenance, for example, is rooted in its experienced internal teams who validate AI recommendations and continuously refine their models (Delta Tech Ops). Airlines must upskill their workforce to leverage AI tools most effectively.
Finally, collaboration across the ecosystem is key. Aviation companies, ERP vendors, OEMs, and suppliers should work together to align data strategies and system integrations. Building a connected network allows predictive insights to flow smoothly across every part of the operation.
Ready to future-proof your fleet? Discover how ePlaneAI can help you integrate aviation-specific AI into your existing ERP—and keep your operations flying high.
Reference: McKinsey & Company: The generative AI opportunity in airline maintenance.
Aviation Maintenance Trends That May Gain Momentum in Uncertain Circumstances
Aircraft are staying in service longer, supply chains are a powder keg, and the tech is evolving overnight. Discover the maintenance trends gaining momentum and what they mean for operators trying to stay airborne and profitable.
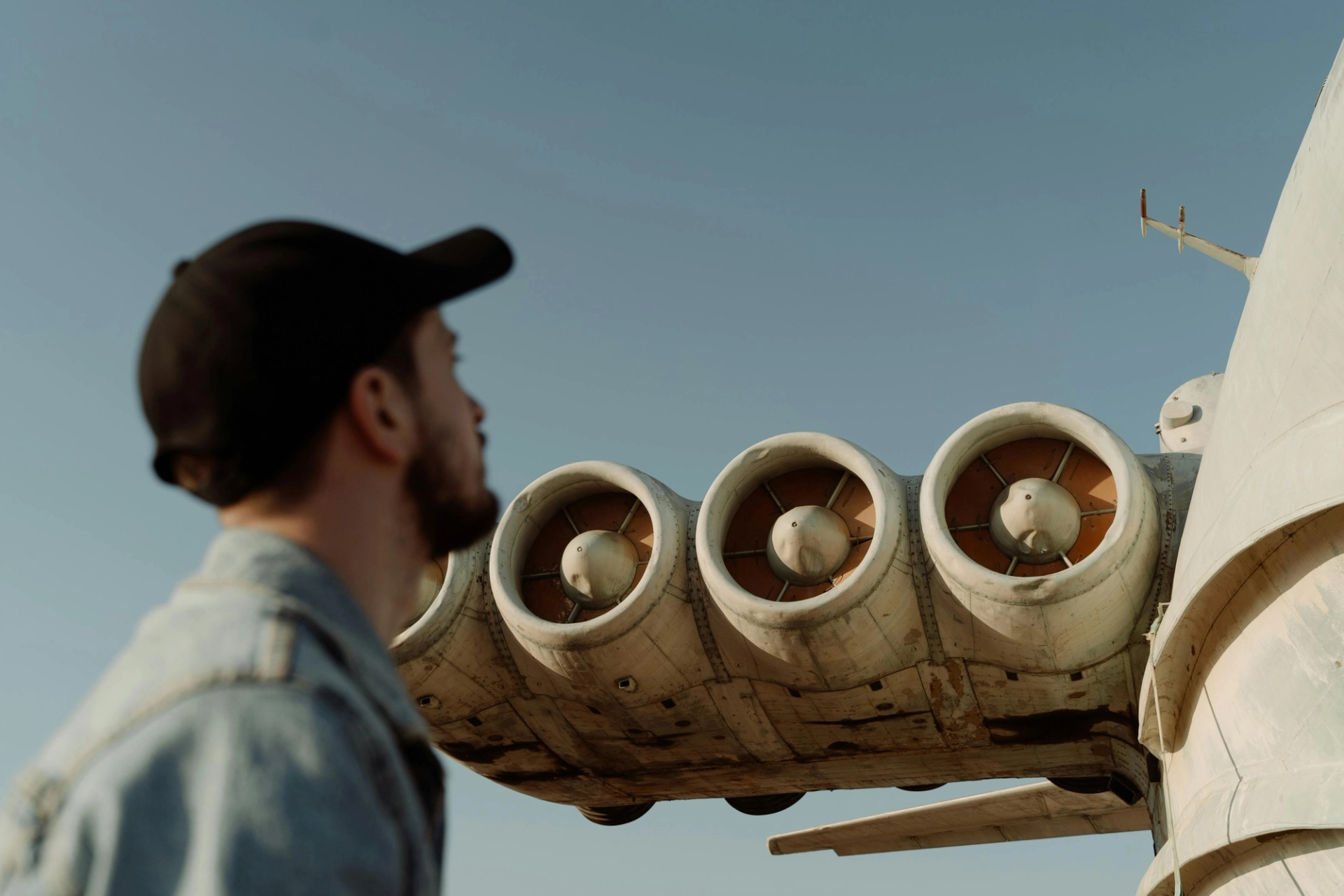
September 4, 2025
How ePlaneAI Can Help You Create an Aviation Sales Accountability Plan
Aviation sales need accountability more than ever. See how ePlaneAI helps airlines, MROs, and suppliers create data-driven sales accountability plans that boost performance, align incentives, and drive measurable growth.
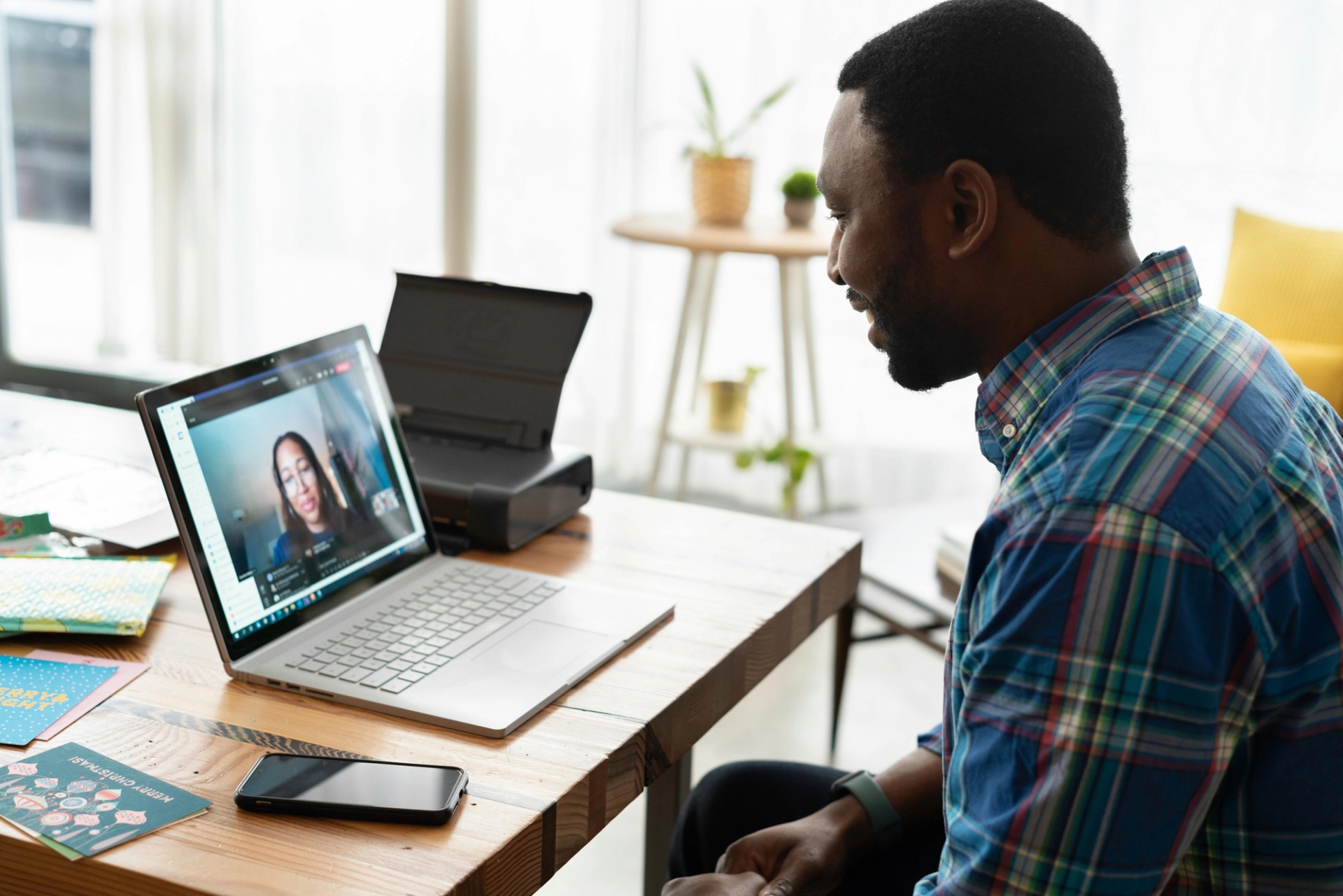
September 1, 2025
Aircraft Part Shipping Strategies That Work for Your Business
From urgent AOG shipments to oversized engine freight, better aircraft part shipping strategy matters. Learn the most effective ways to move high-value aviation parts safely, quickly, and cost-efficiently.
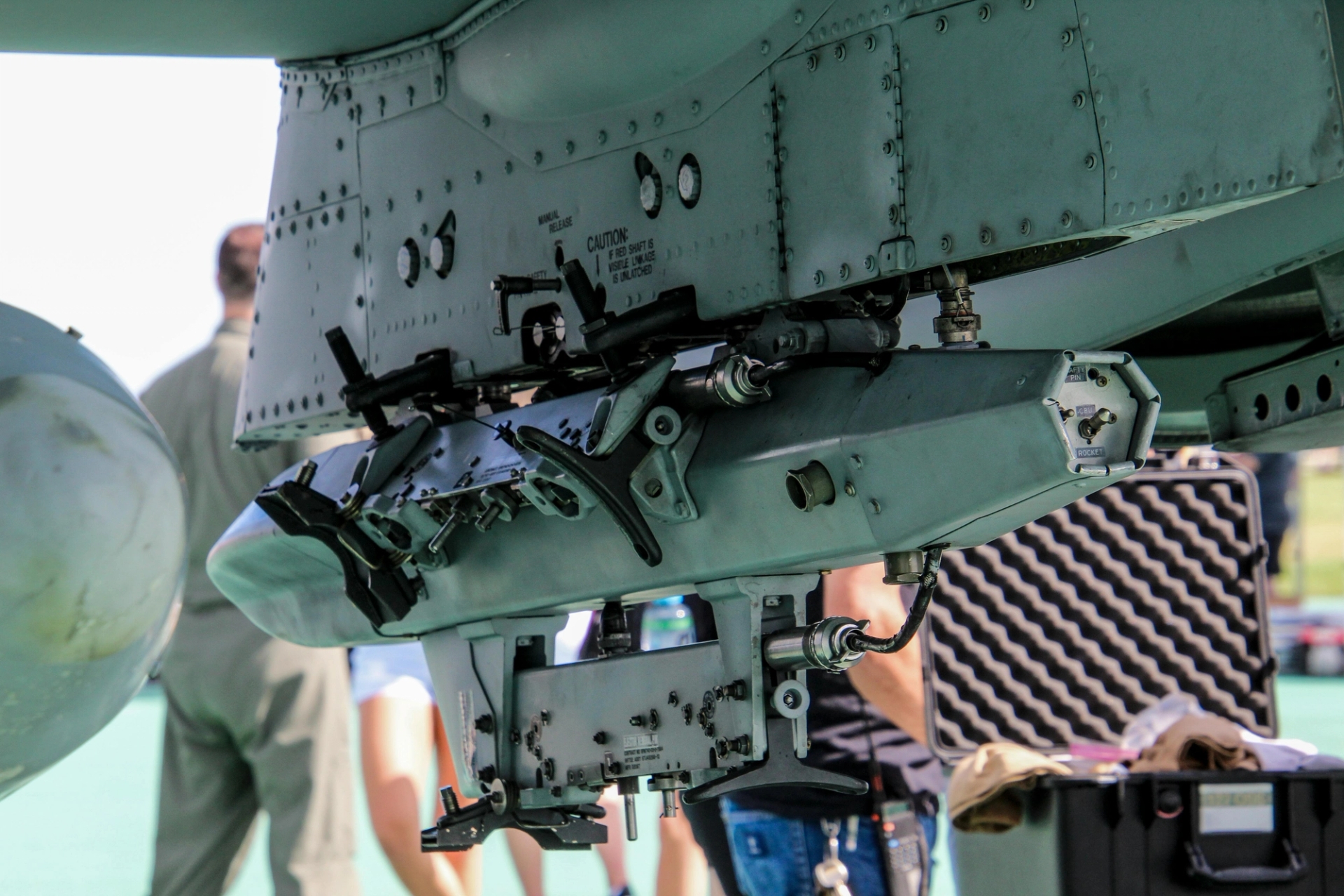
August 27, 2025
How to Use AeroGenie to Streamline Procurement Reporting in Aviation
What makes AI tools understand human language? It’s not magic—it’s NLP. Learn how NLP works, where it's going, and how it's changing the way we query and build reports with AI.
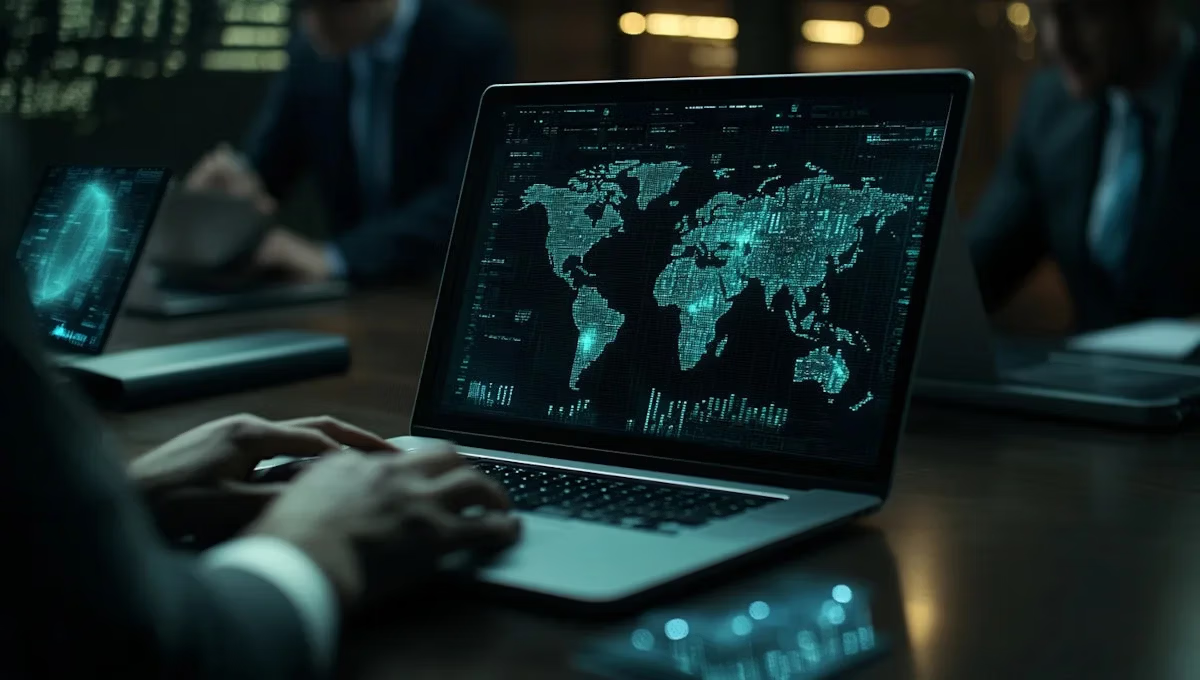