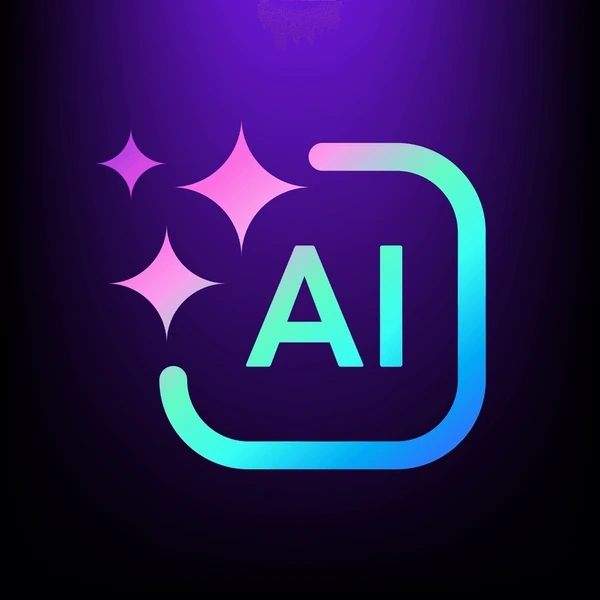
Email più intelligenti, business più veloce. Tag automatici, analisi e risposte immediate a richieste, preventivi, ordini e altro.
Tendenze
Categories
Can Superalloy Techniques Resolve Aircraft Engine Issues in Sixth-Generation Fighters?
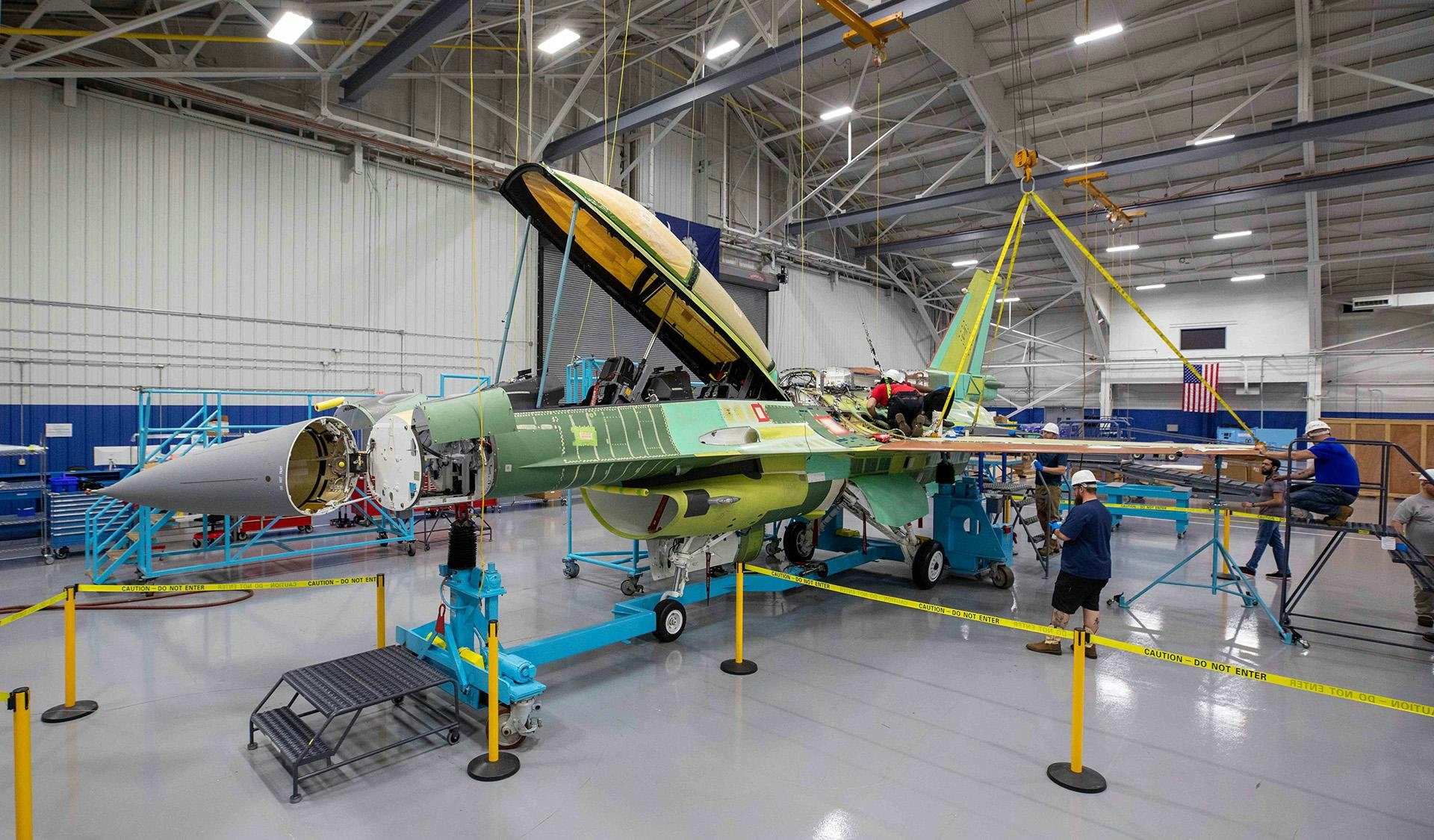
Can Superalloy Techniques Resolve Aircraft Engine Issues in Sixth-Generation Fighters?
Advances in Superalloy Processing for Aircraft Engines
Chinese researchers have announced promising laboratory results for a novel superalloy processing technique that could enhance the strength and durability of aircraft engines, according to state media reports. The innovation focuses on superalloy turbine discs, a critical and technically demanding component of aircraft engines. Developed by a team at Dalian University of Technology in northeast China, the method involves rapidly cooling the metal alloy during manufacturing, potentially leading to significant performance improvements. This advancement is being considered for integration into engines designed for China’s next-generation, sixth-generation fighter jets, a sector where the country faces increasing pressure to close the gap with Western aerospace leaders.
Turbine discs play a pivotal role in engine operation, serving as the foundation for turbine blades that convert thermal energy from fuel combustion into the rotational force necessary to propel aircraft. These components must endure extreme temperatures, high pressure, and intense rotational speeds, making the choice and treatment of superalloy materials crucial to engine power, efficiency, and longevity. The rapid cooling technique developed by the Dalian team aims to enhance these properties, potentially extending the operational lifespan and reliability of turbine discs in demanding flight conditions.
Challenges in Integration and Industry Implications
Despite the potential benefits, incorporating advanced superalloy techniques into existing engine designs presents significant challenges. The adaptation process is complex and can lead to delays and increased costs, as engineers must ensure that new materials are compatible with current manufacturing processes and engine architectures. This complexity is underscored by recent setbacks in international projects, such as delays in the F-35 engine upgrade, which highlight the difficulties in meeting ambitious development timelines for next-generation propulsion systems.
These technical hurdles have not escaped the attention of defense contractors and investors, many of whom remain cautious about the feasibility and schedule of such advancements. The aerospace market is closely watching these developments, with global competitors evaluating whether to adopt similar superalloy processing methods or pursue alternative technologies to maintain their strategic advantage in military aviation.
As China advances its sixth-generation fighter programs, the successful application of new superalloy processing techniques could represent a significant technological milestone. However, the transition from laboratory innovation to operational deployment involves navigating a complex landscape of technical, financial, and strategic challenges. The coming years will be critical in determining whether these breakthroughs can effectively address the persistent engine issues that have long challenged the global aerospace industry.
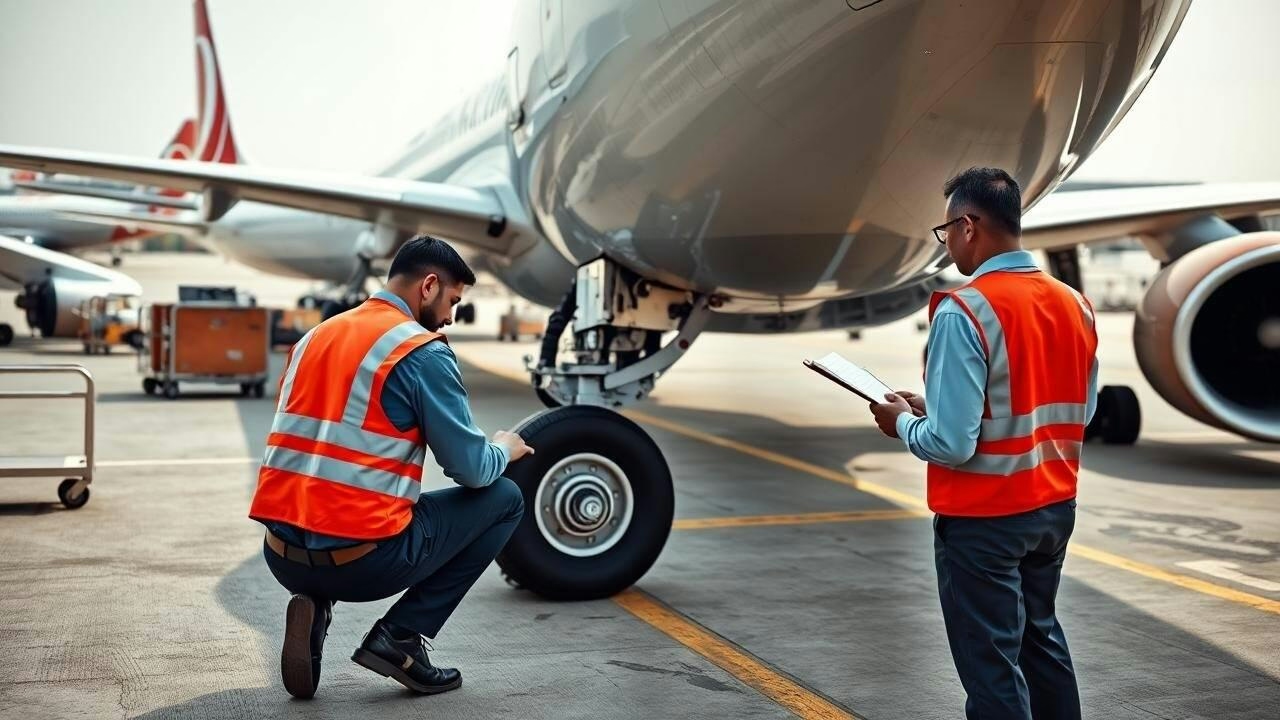
India and Turkey Strengthen Civil Aviation Ties with New Aircraft Leasing Agreements
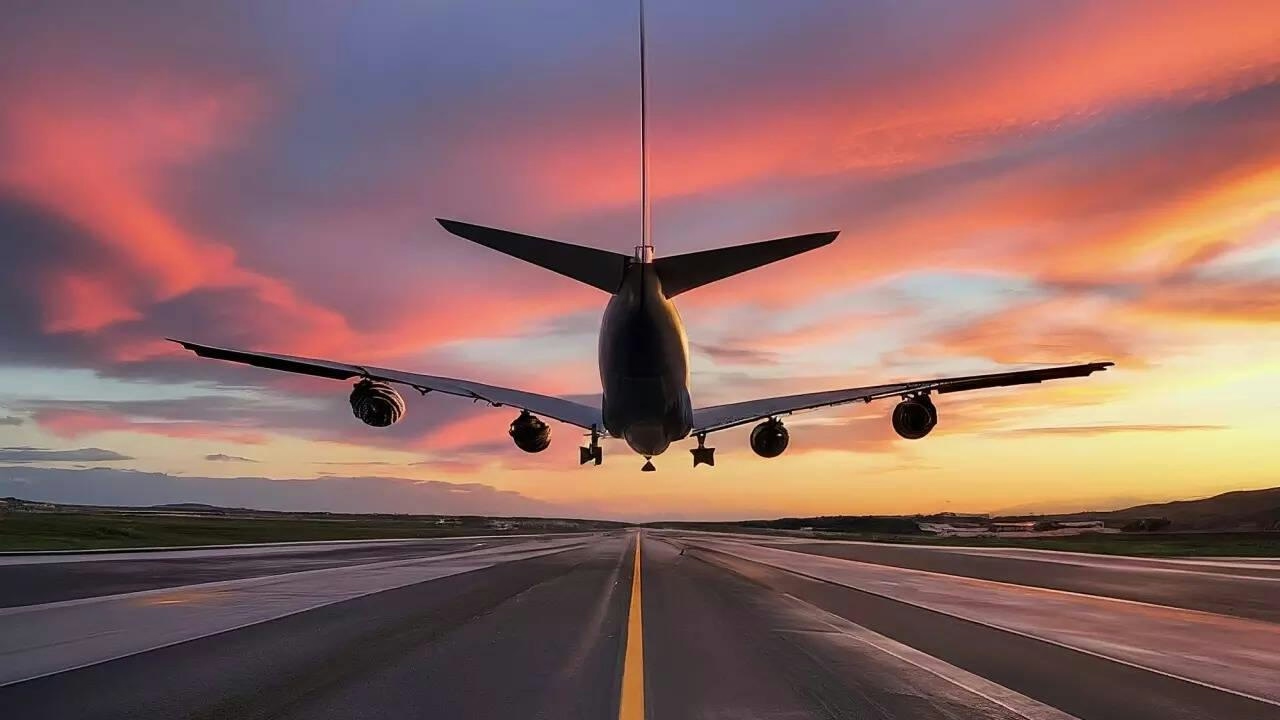
India Restores Aviation Links with Turkey, Extends Leasing Deal Amid Pakistan Airspace Ban
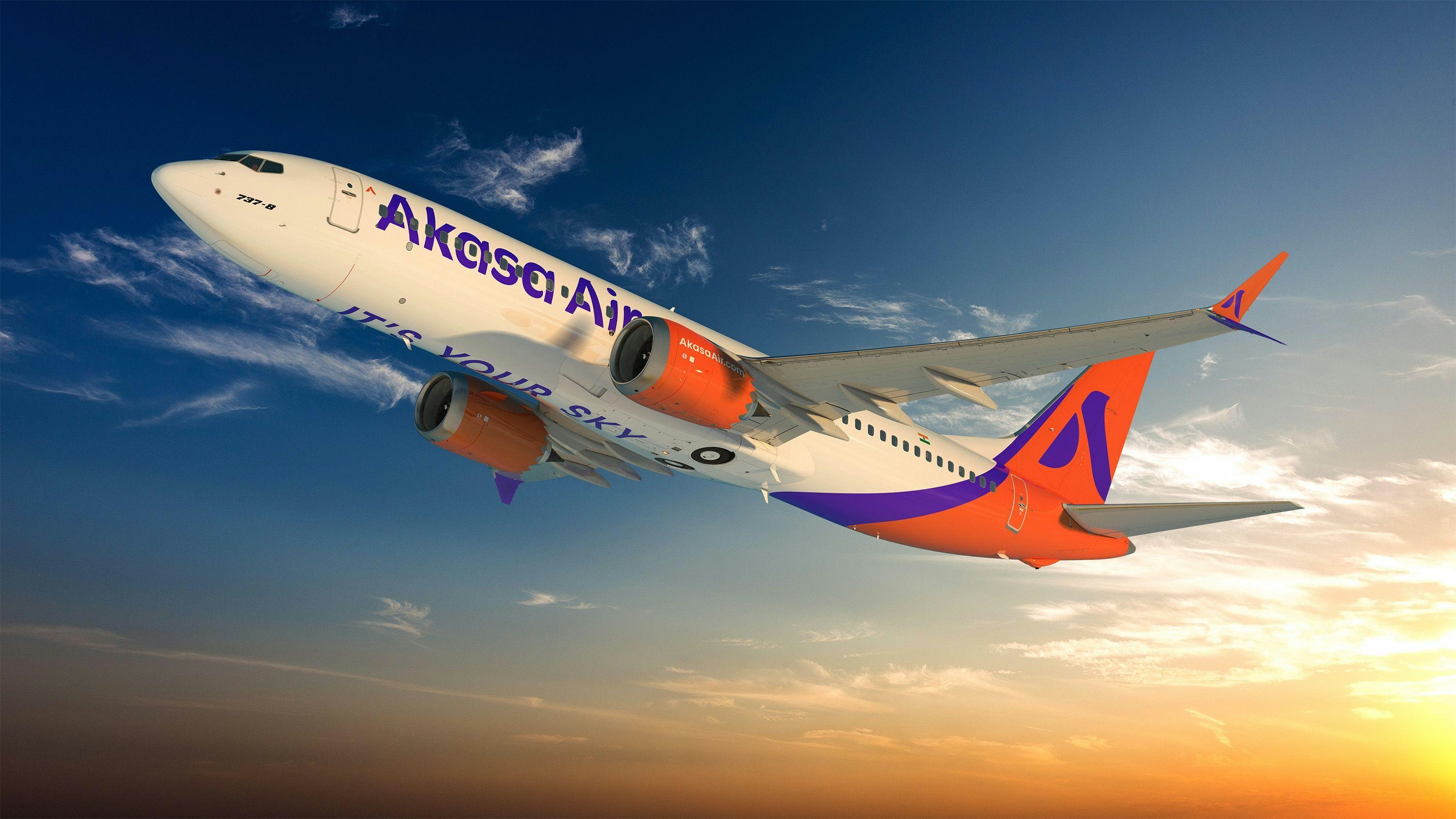
Akasa Air Plans to Expand Fleet to 40 Aircraft by FY26 Amid Boeing Supply Chain Improvements
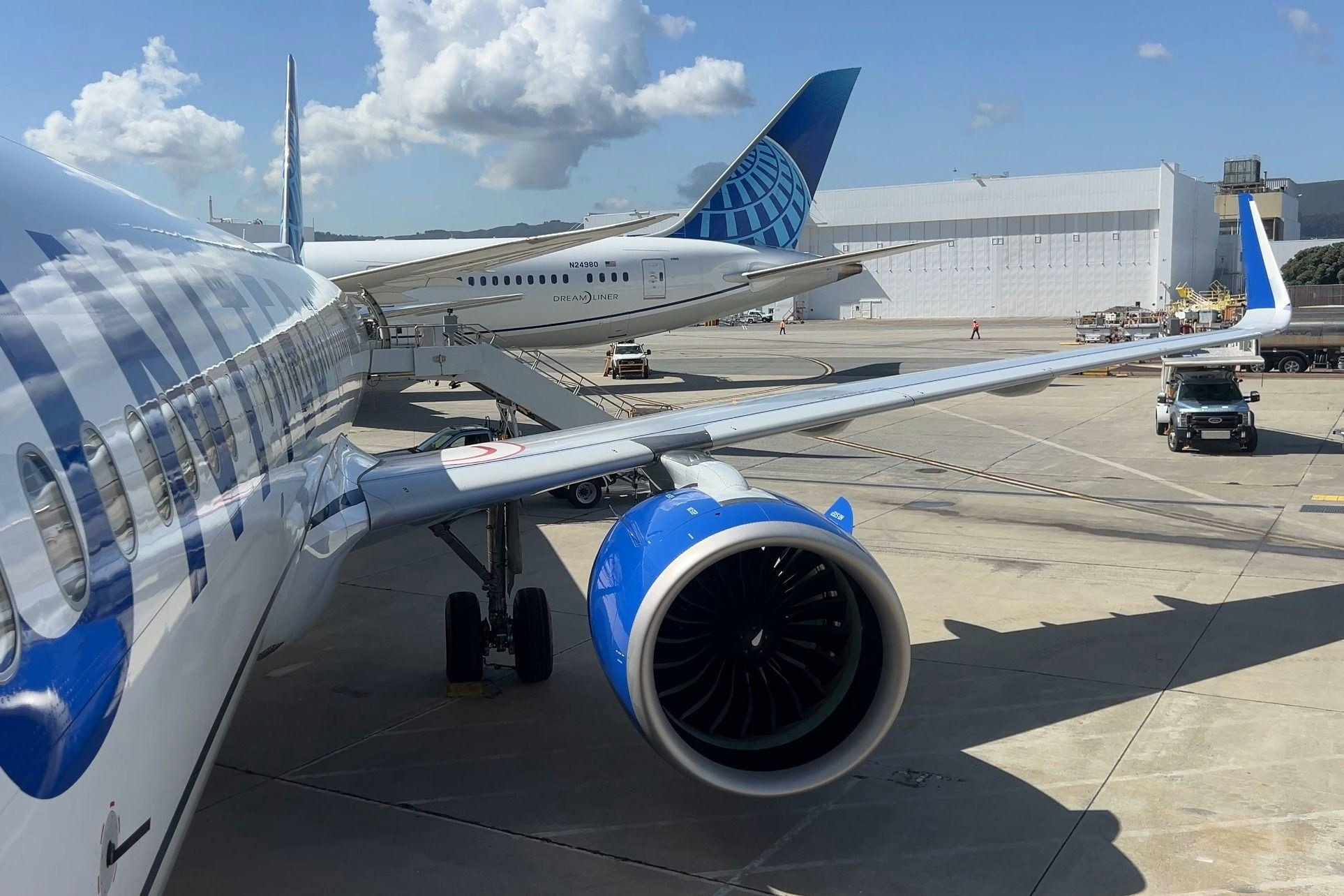
Which Narrowbody Aircraft Is United Airlines the Largest and Only U.S. Operator Of?
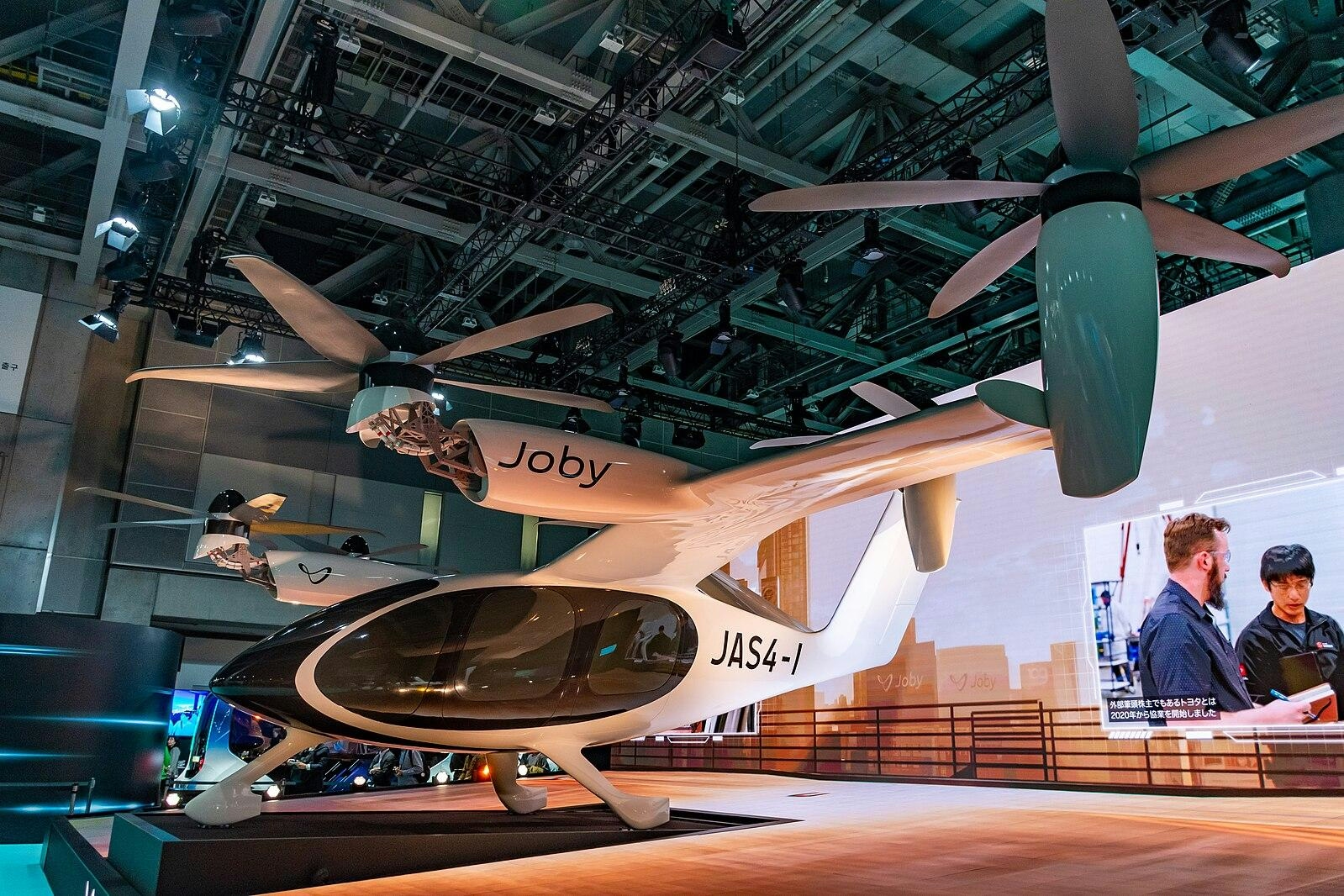
Joby Aviation Shares Fall 0.84% Amid Regulatory Delays and Partnership Changes
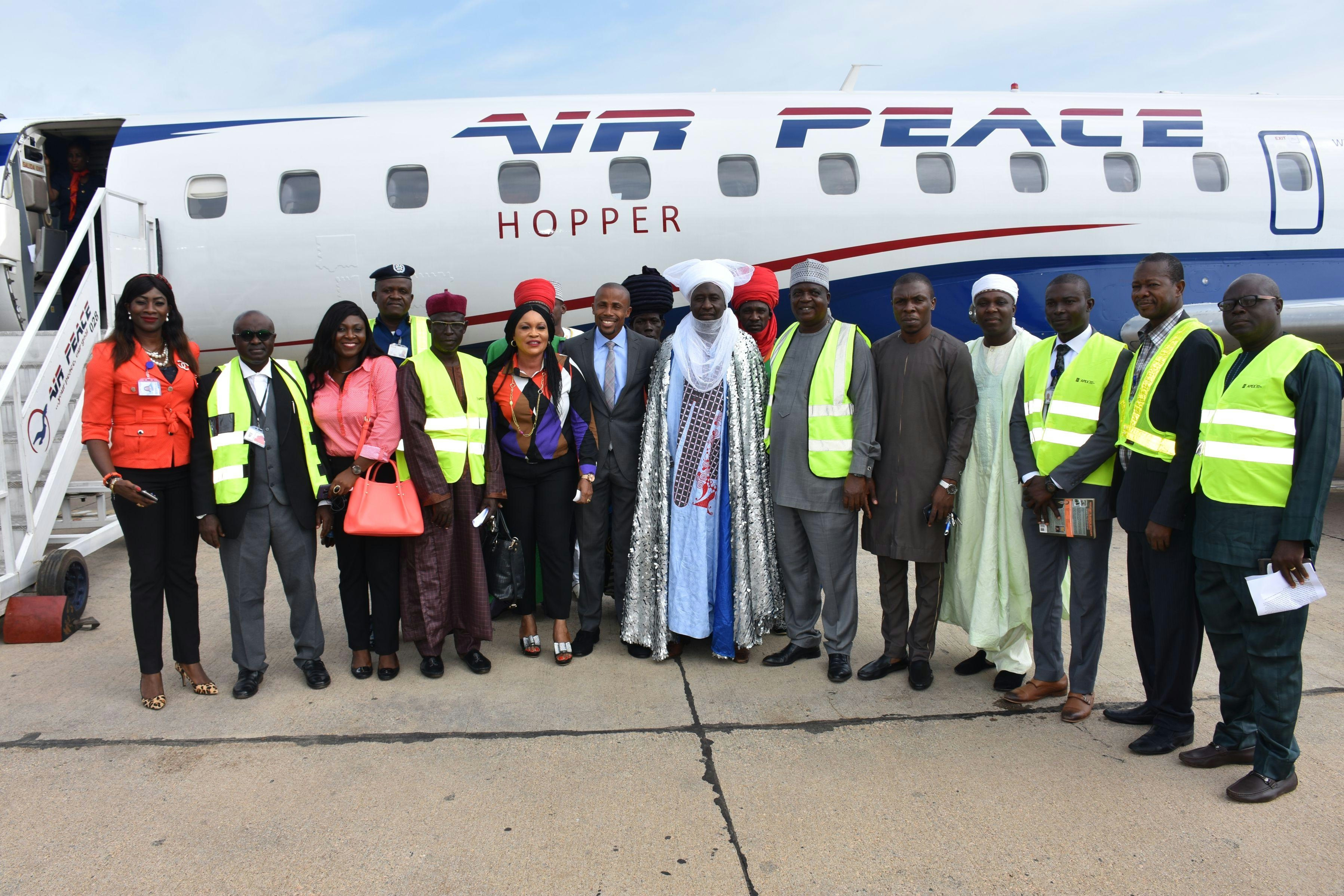
Air Peace Expands Lagos Hub to Enhance West Africa Travel
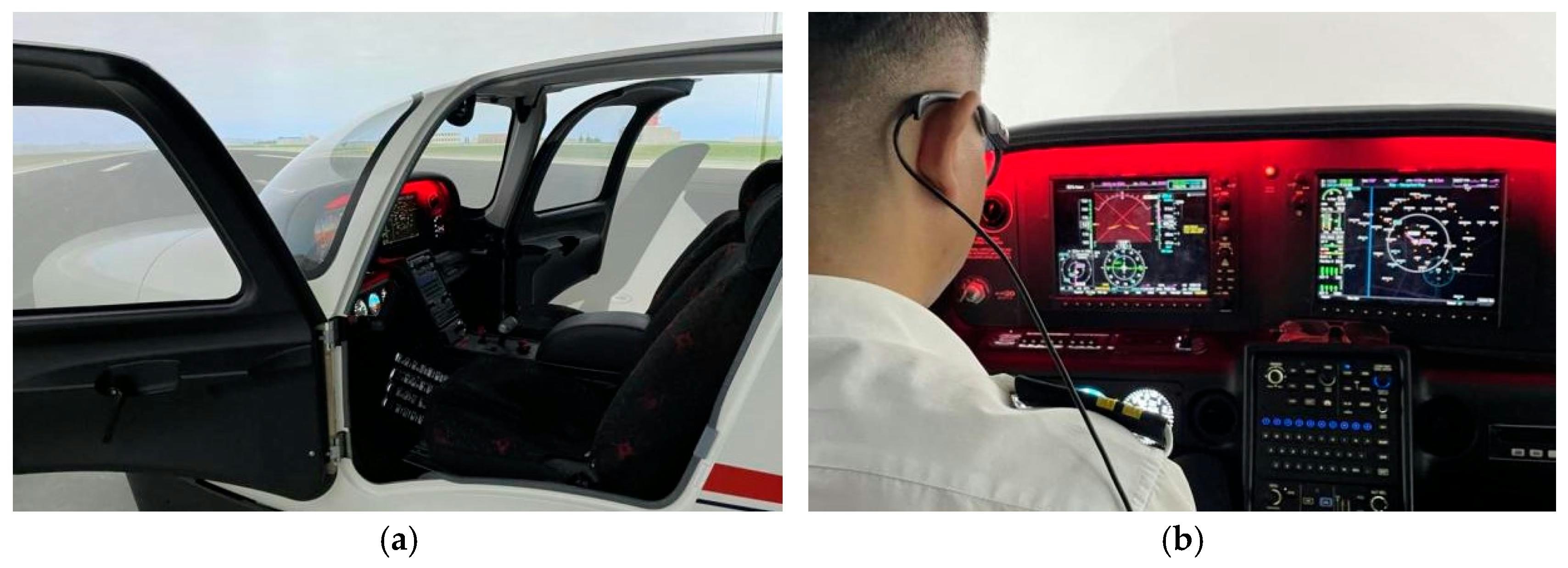
APC Introduces Project ORCA AI Tools for Pilot Training

Autonomy Proving Ground Conducts First Alternative Navigation Flight
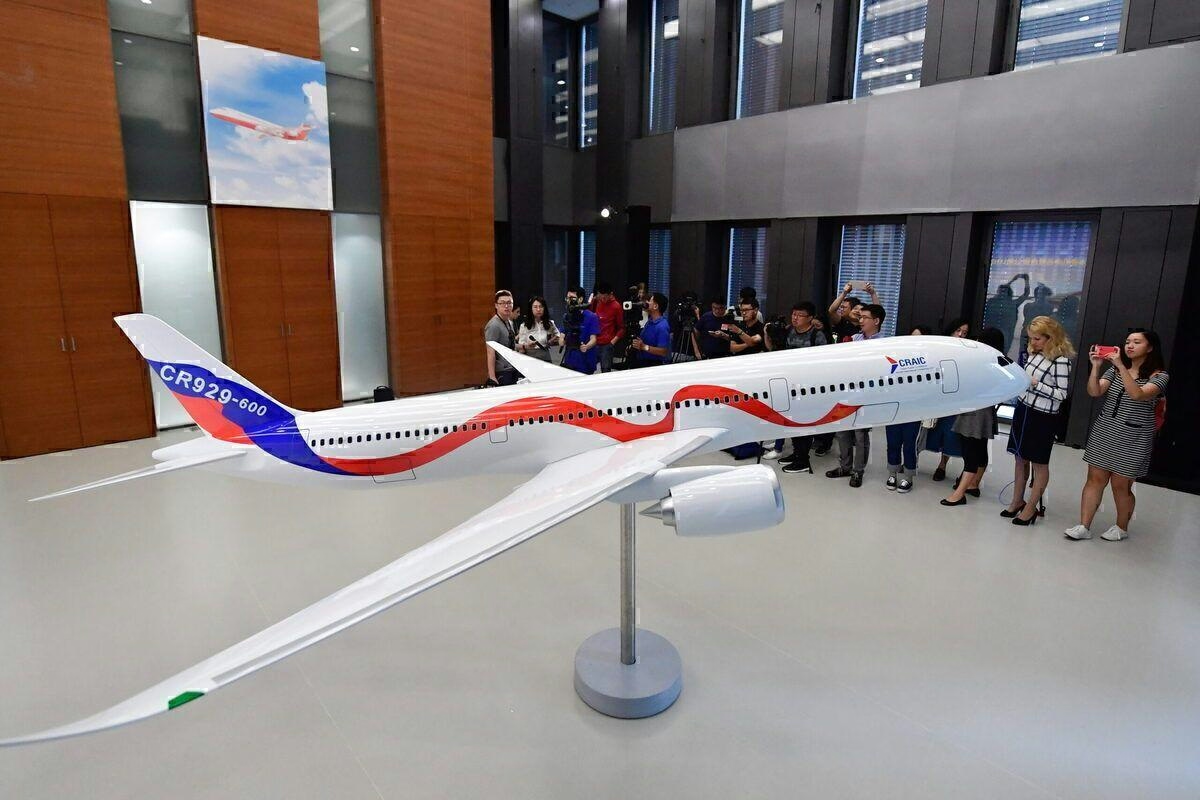
Can Russia’s new widebody aircraft rival Boeing’s Dreamliner?
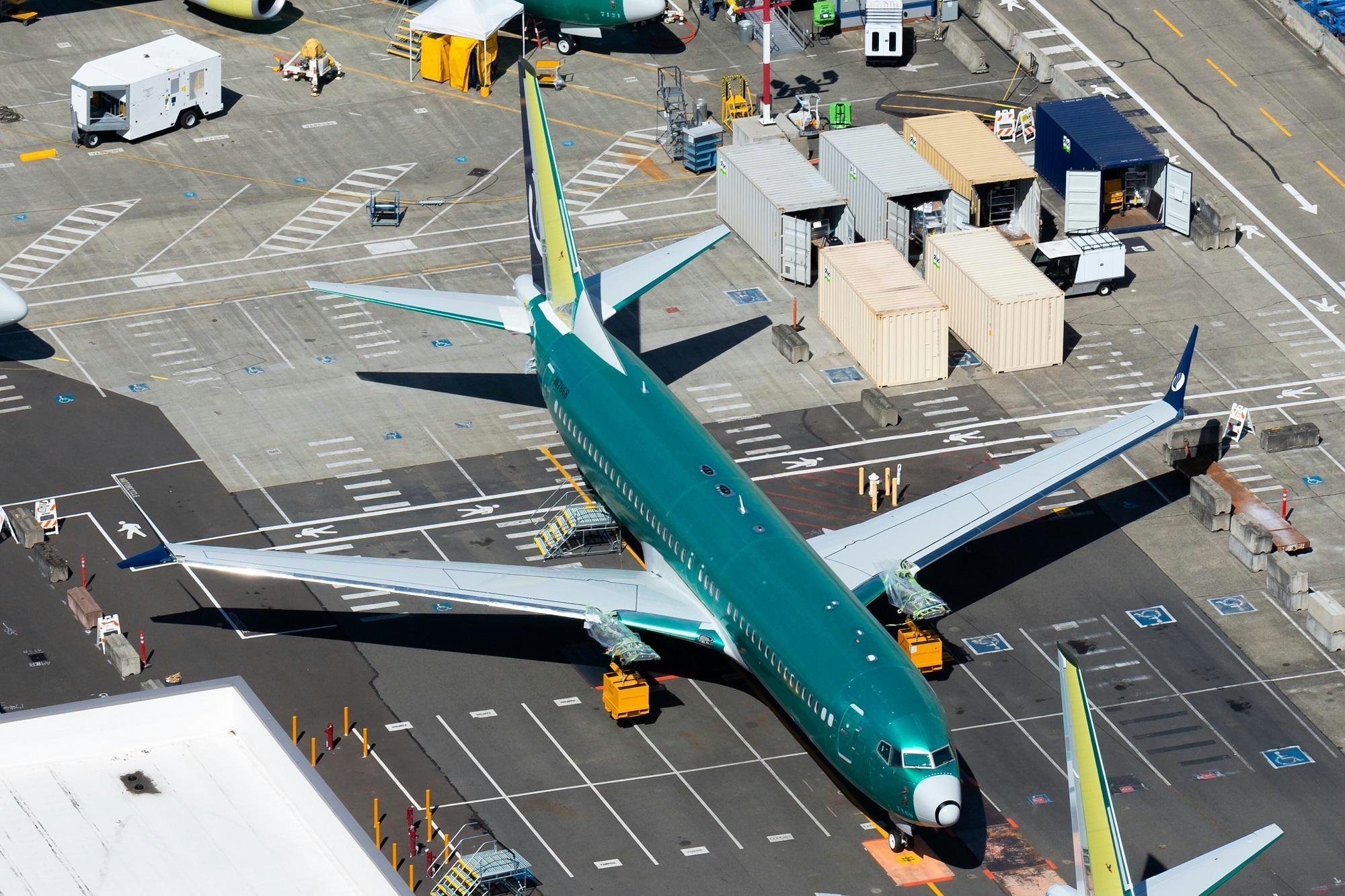