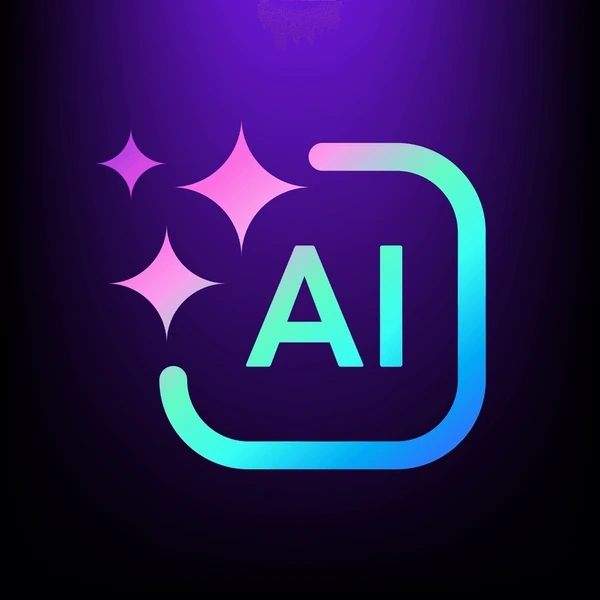
Smarter email, faster business.
Trending
Categories
Safran Landing Systems Expands and Modernizes Molsheim Facility
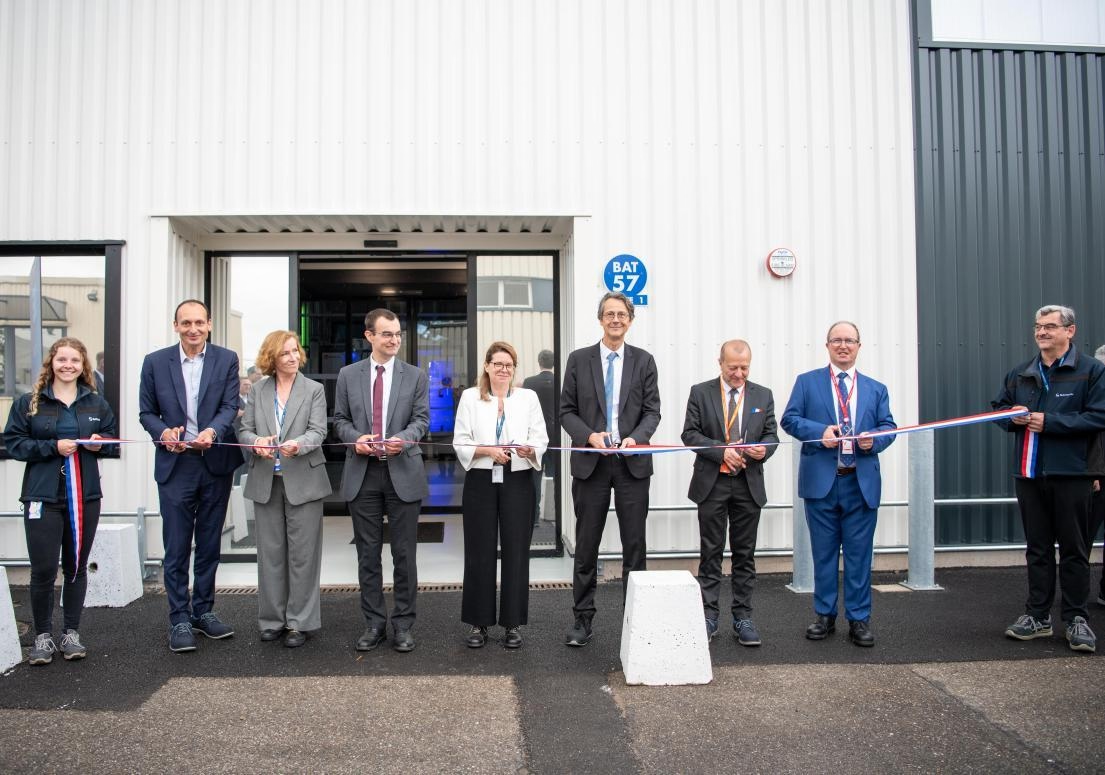
Safran Landing Systems Expands and Modernizes Molsheim Facility
Safran Landing Systems has officially inaugurated a new, state-of-the-art machining building alongside two advanced surface treatment lines at its Molsheim site in Alsace, France. This development marks a significant milestone in the company’s ongoing efforts to modernize its production capabilities. The inauguration ceremony was attended by prominent regional and corporate figures, including Claude Sturni, Vice-President of the Grand Est Region; Thierry Rogelet, Sub-Prefect of Molsheim; Olivier Andriès, CEO of Safran; and François Bastin, CEO of Safran Landing Systems.
Enhancing Production Capacity and Technological Capabilities
The expansion aims to bolster the facility’s ability to produce and maintain landing and braking systems, addressing the increasing demands driven by rising aircraft production rates and the global growth of maintenance, repair, and overhaul (MRO) services. Central to this upgrade is the newly opened ExcelFAB building, which spans 840 square meters and houses high-tech five-axis machining centers. These centers are tasked with manufacturing critical components such as braking manifolds, uplocks, and steering manifolds. The facility operates with a fully automated production process designed to ensure high industrial performance and superior quality standards.
This modernization effort was supported by a €1.125 million grant from the Grand Est Region in 2021, which facilitated the development of ExcelFAB and the enhancement of broader production capabilities at the Molsheim site. In addition to the machining building, the expansion includes a sulfuric acid anodizing (SAA) line dedicated to treating aluminum components like wheels and hydraulic rings, as well as a chrome plating line that services landing gear maintenance for up to 3,000 different types of steel parts. Both treatment lines are equipped with digital technologies that enable real-time monitoring of production data, thereby improving quality control processes.
Commitment to Sustainability and Corporate Responsibility
Safran’s modernization initiative also reflects a strong commitment to corporate social responsibility and environmental sustainability. The new facilities feature ergonomically optimized workstations designed to minimize manual handling and enhance worker safety. ExcelFAB incorporates advanced thermal insulation and a reversible thermodynamic heating system, which together have reduced energy consumption by 40%. The newly installed machining centers are 10% more energy efficient compared to previous models. Furthermore, the SAA line has achieved a significant reduction in CO₂ emissions—cutting 98 tonnes annually—through the implementation of a heat pump system that replaces traditional gas heating.
Challenges and Market Implications
While the expansion positions Safran Landing Systems to better meet industry demand and underscores its dedication to innovation and sustainability, it also introduces several operational challenges. The company must carefully manage increased production costs and ensure the seamless integration of new technologies, all while maintaining strict compliance with aviation regulations. Market reactions have been predominantly positive, with investor confidence rising in response to Safran’s growth prospects. However, concerns remain regarding potential supply chain disruptions as the facility scales up its operations.
This strategic move is also expected to prompt competitors within the landing systems sector to accelerate their own modernization and expansion efforts in order to maintain market share amid intensifying competition. Safran’s latest developments at Molsheim thus highlight its strategy to combine industrial excellence with environmental responsibility, even as it navigates the complexities of a rapidly evolving aerospace market.
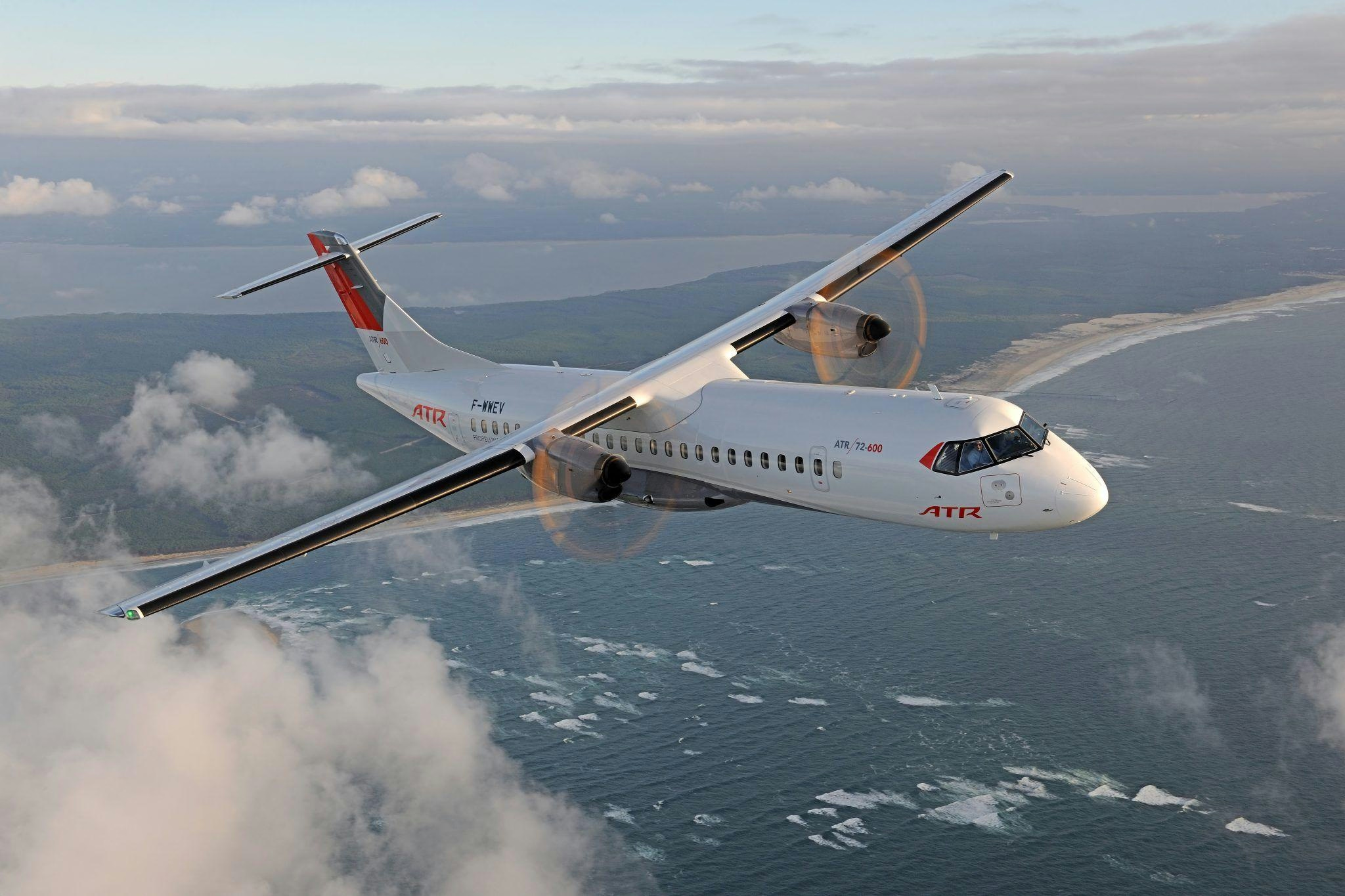
Air Mauritius Replaces ATR72-500 with ATR72-600 Aircraft

Thai AirAsia Plans Increased Operations at Suvarnabhumi, Cautious on China Market
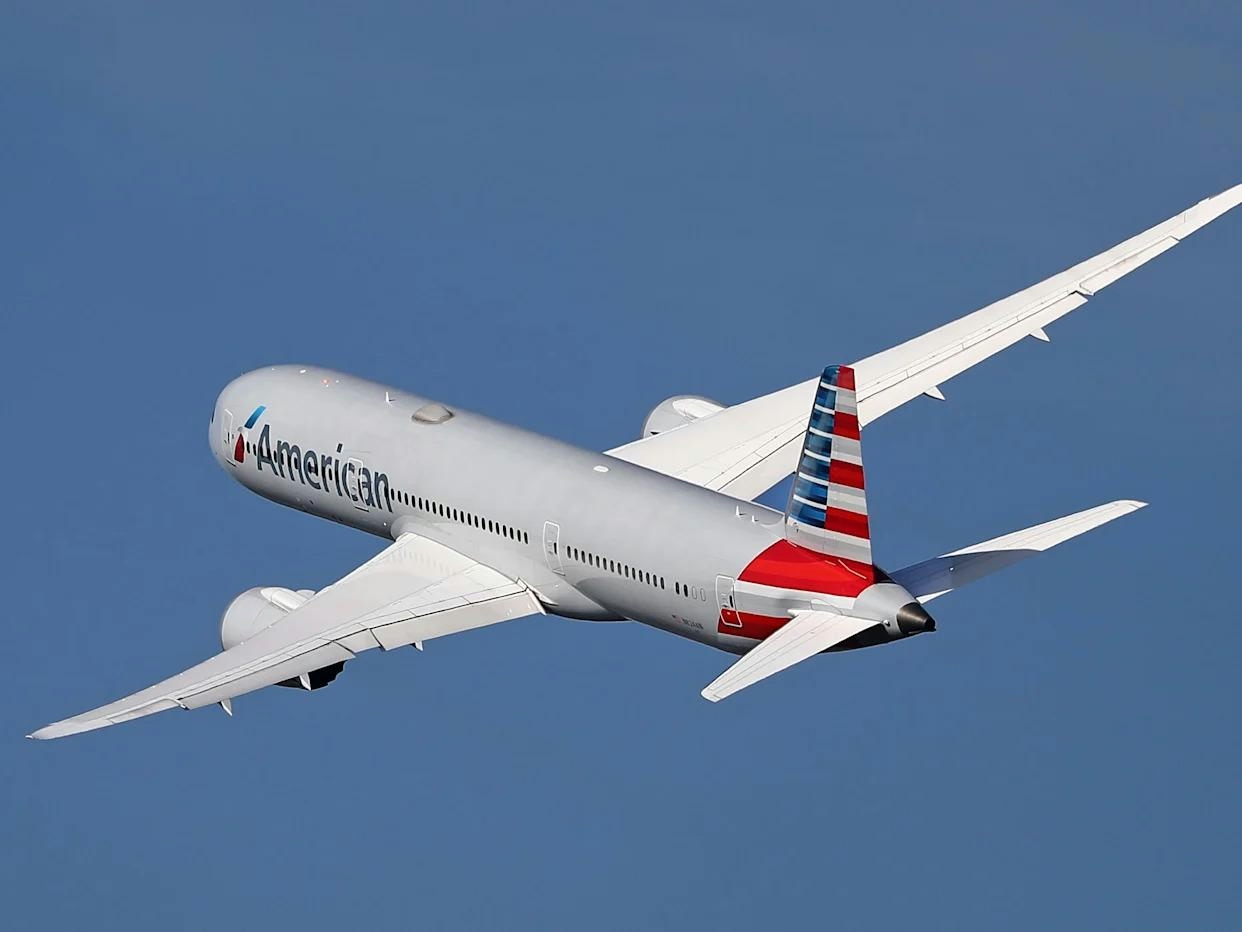
Investigation Underway After Dreamliner Diverts Over China
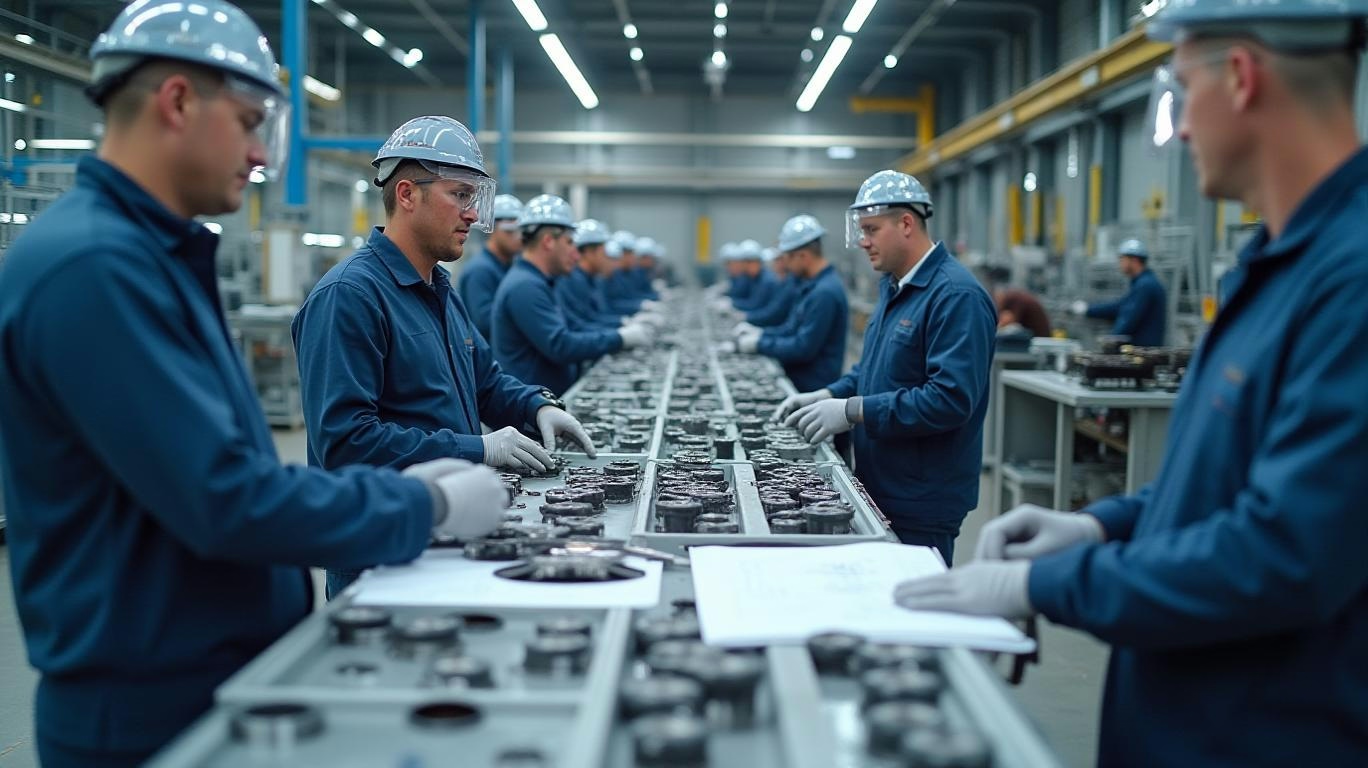
Howmet Aerospace’s Role in Global Aviation and Its Market Valuation
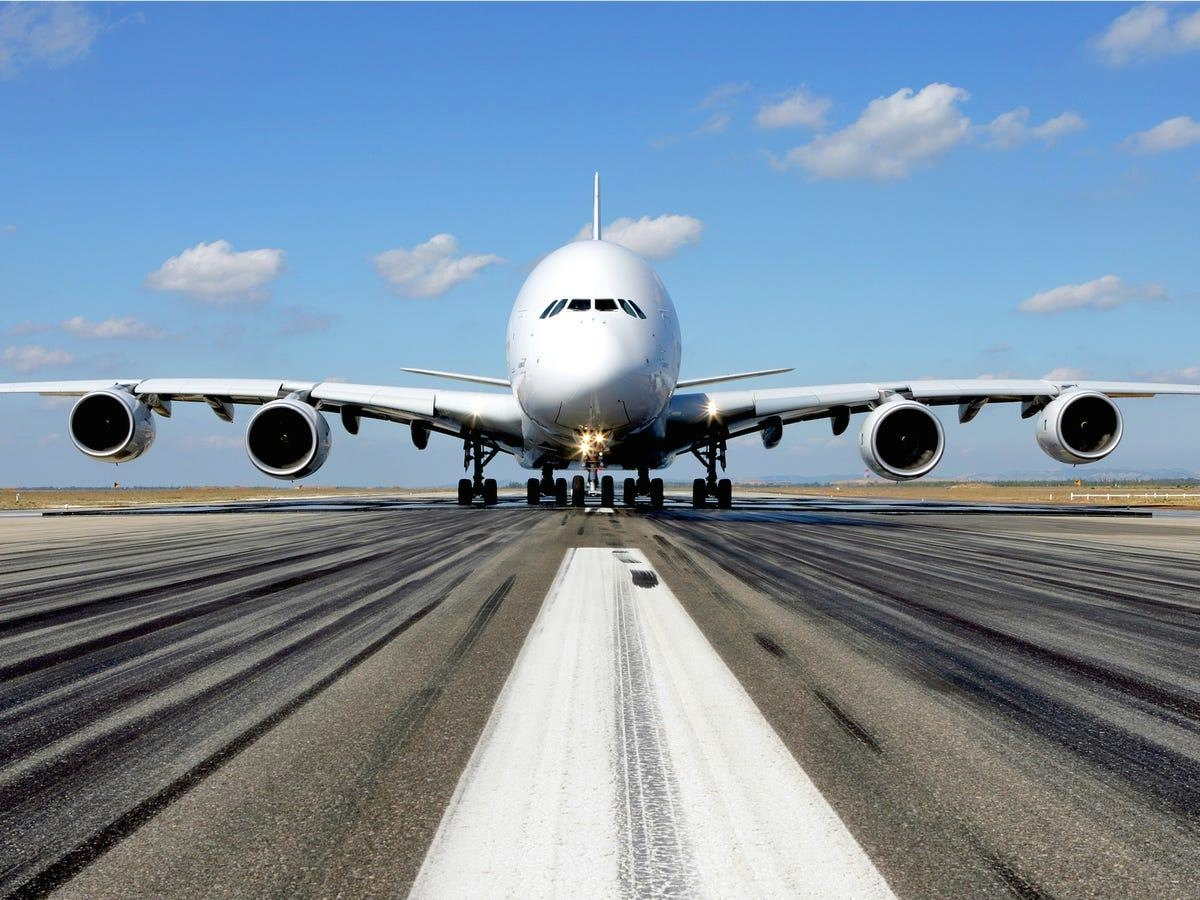
Why No U.S. Airlines Operate the Airbus A380
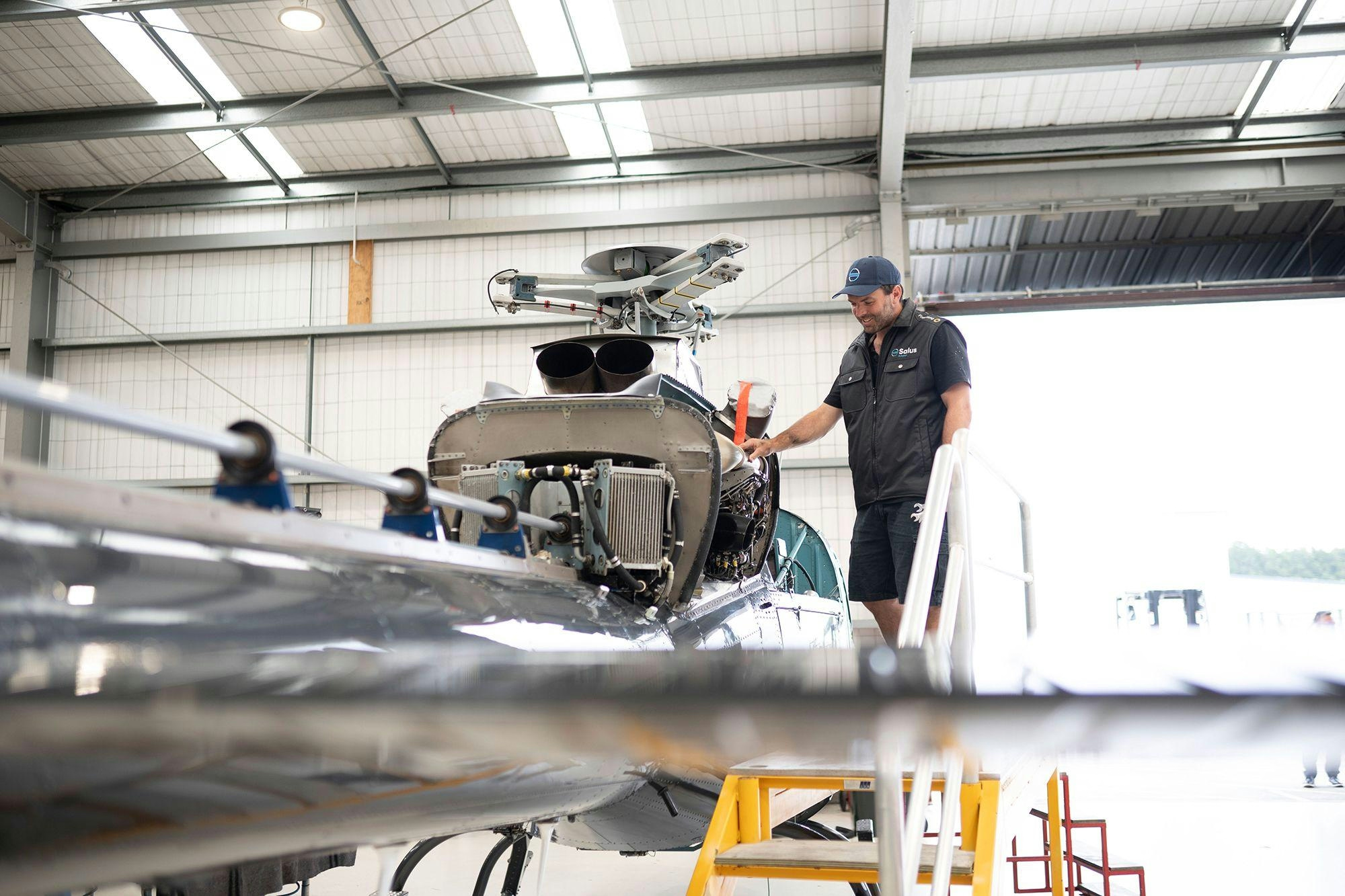
Iranian Technicians Overhaul BK 117 Helicopter Engine
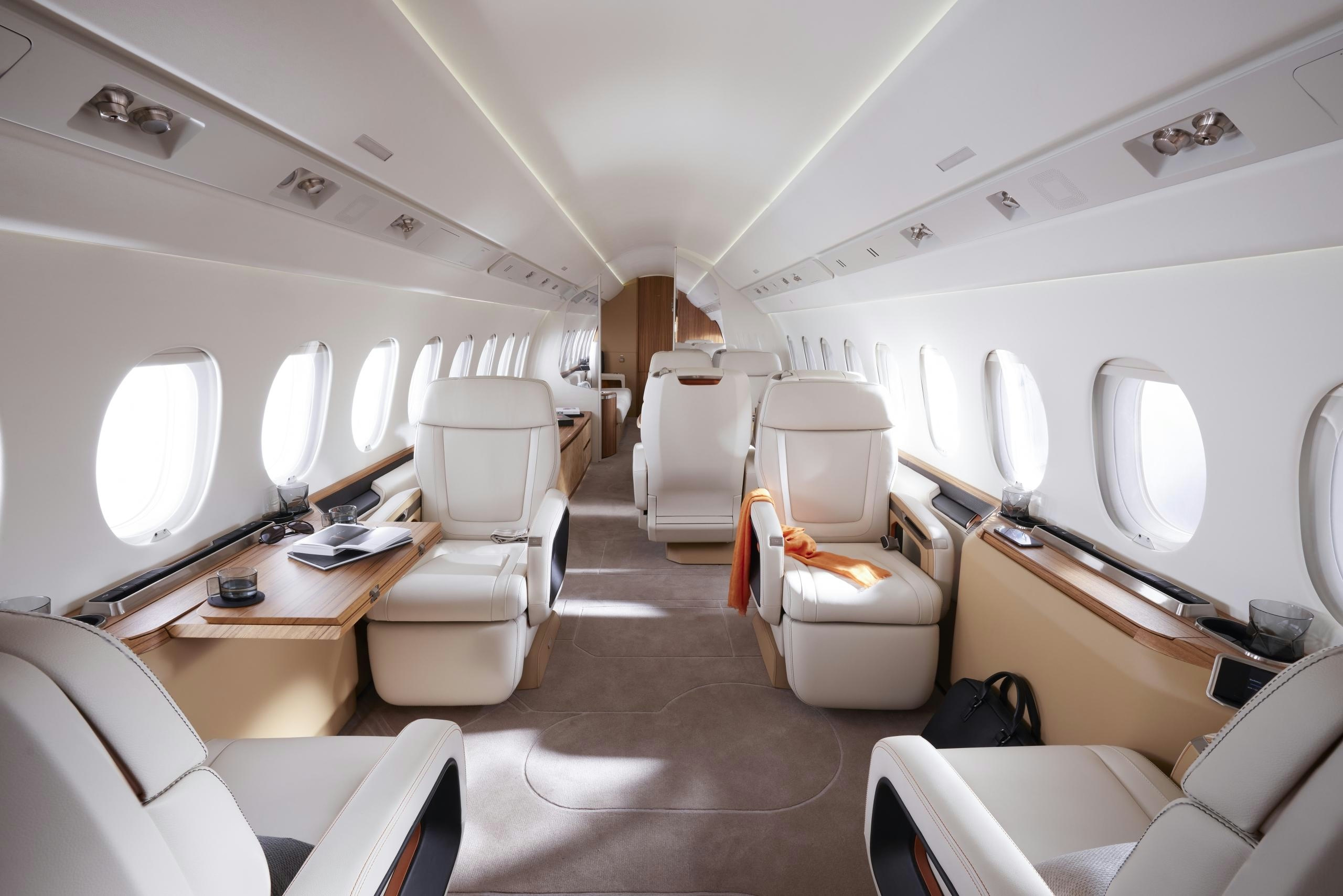
Canada's Flightpath Begins Operations with Dassault Aviation
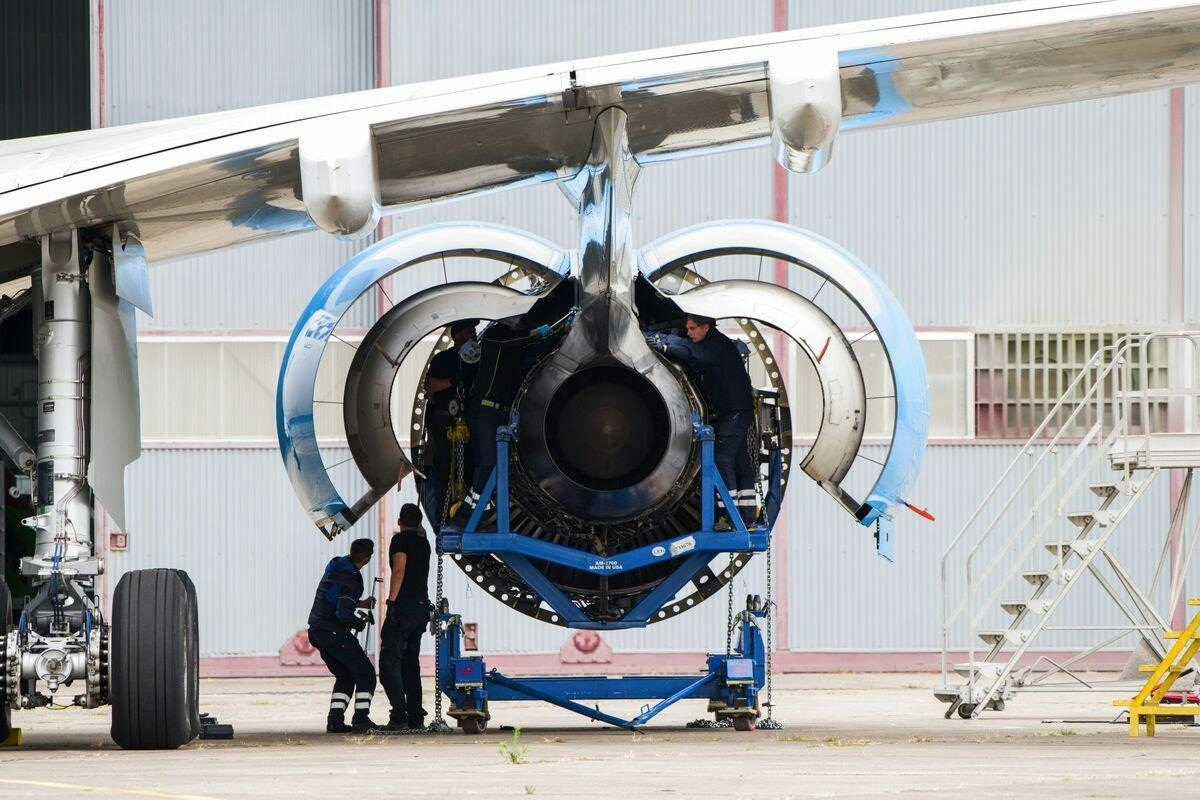
Powerhouse Engines Acquires Two CFM56-5B Engines to Expand Leasing Portfolio
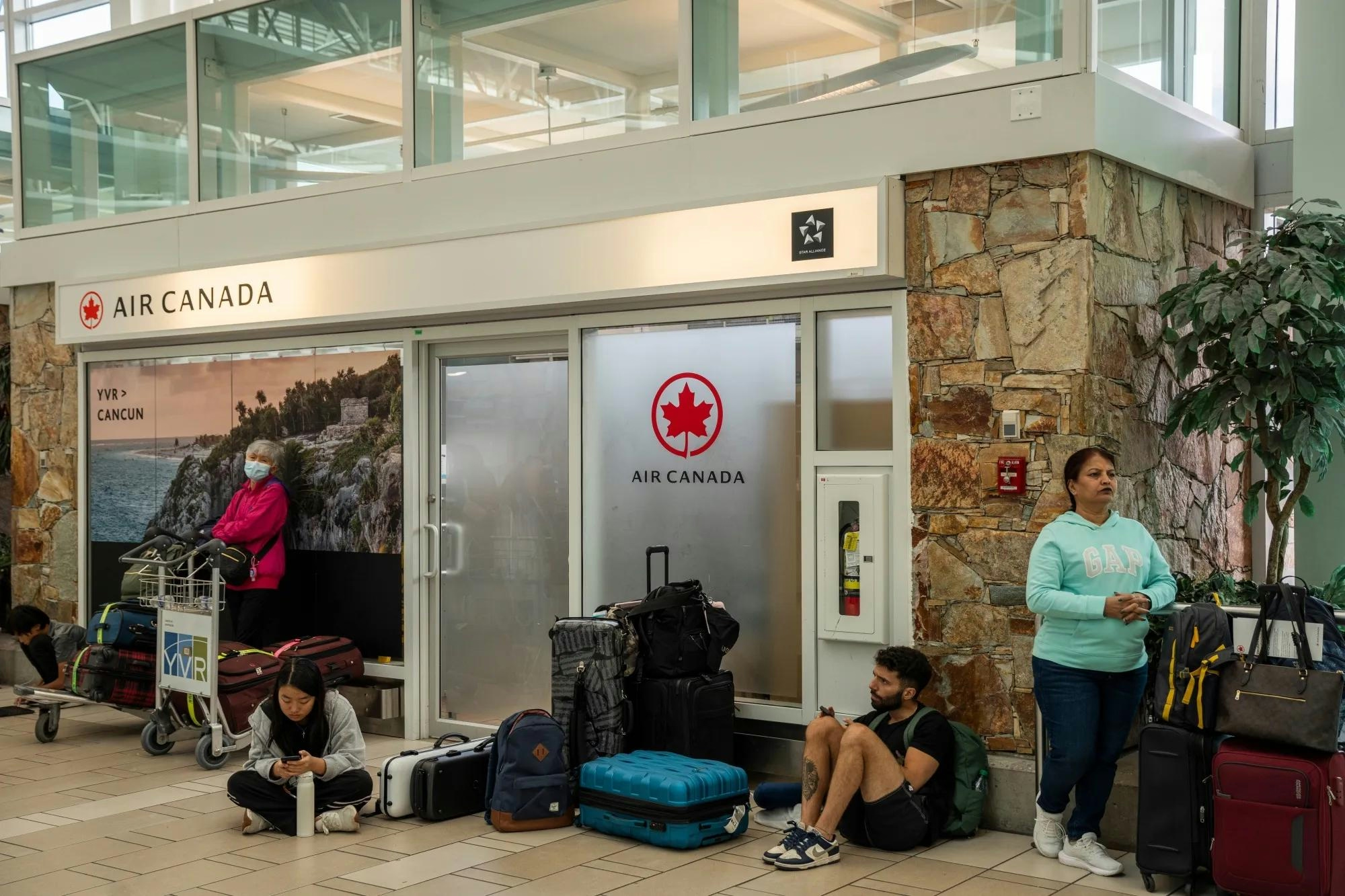
Air Canada Grounded by Strike, Withdraws Financial Guidance
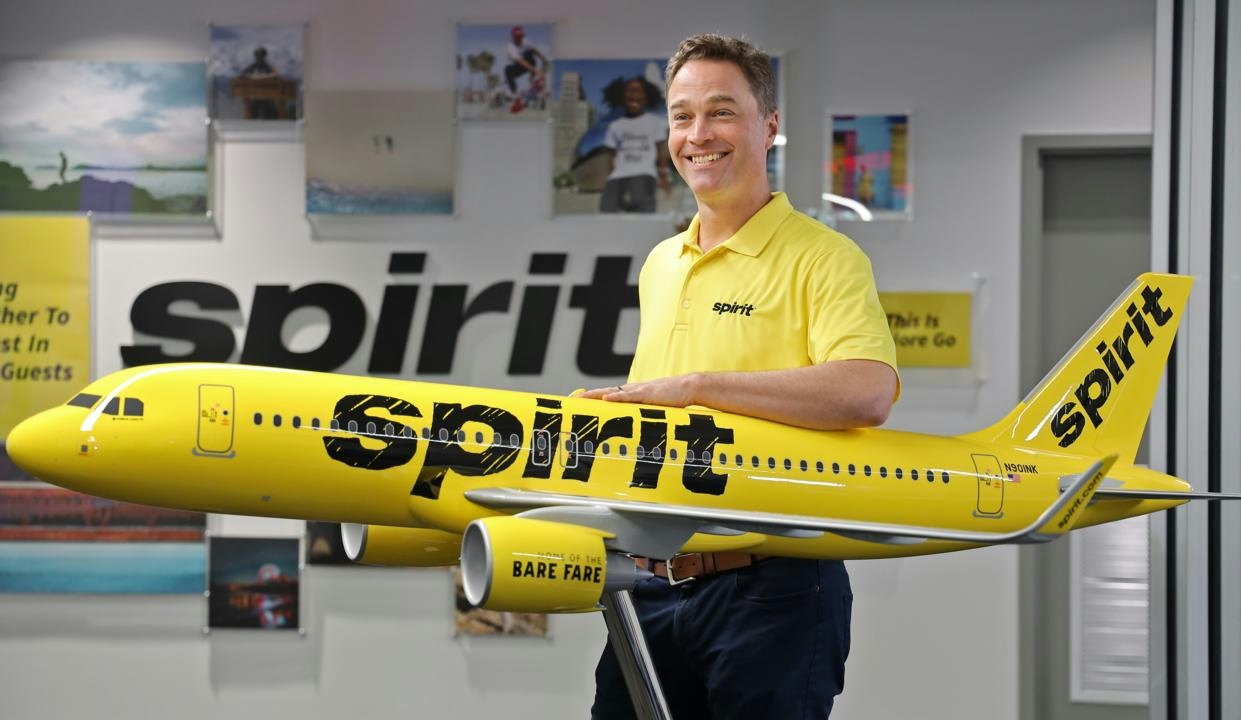