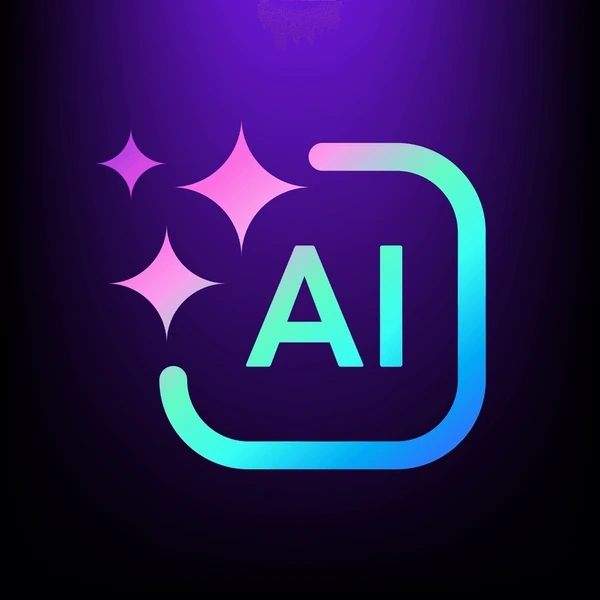
بريد إلكتروني أذكى، وأعمال أسرع. وسم وتحليل والرد تلقائيًا على طلبات العروض، وعروض الأسعار، والطلبات، والمزيد — فورًا.
الرائج الآن
Safran Sees Growing Role For Additive Manufacturing In Engines

Safran Advances Additive Manufacturing in Turbofan Engine Production
At the Paris Air Show this year, Safran showcased significant progress in additive manufacturing (AM) with the unveiling of a turbine rear frame produced under its RISE technology program. Measuring three feet in diameter, this component represents the largest part the company has fabricated using AM, highlighting the growing integration of this technology in turbofan engine design and manufacturing.
Innovations and Efficiency Gains
Delphine Dijoud, vice president engineering deputy at Safran Aircraft Engines, emphasized that the new turbine rear frame is approximately one-third lighter than its traditionally cast and machined equivalent. The production timeline has also been drastically shortened, shrinking from 18 months to just three weeks. Safran aims to further reduce this cycle to one week or less, enabling more agile design modifications and accelerating innovation.
The component was manufactured using a nickel superalloy powder, chosen for its suitability in the engine’s high-temperature hot section. While additive manufacturing is not always the most cost-effective method for melting metal, Francois-Xavier Foubert, CEO of Safran Additive Manufacturing Campus, explained that the process offers distinct advantages when it eliminates welds, reduces weight, or allows for more complex, functionally integrated designs. AM also improves material efficiency, with a buy-to-fly ratio significantly better than traditional methods: conventional manufacturing requires 3 to 10 pounds of metal to produce a 1-pound part, whereas AM uses only about 1.5 pounds. The parts produced are nearly net shape, minimizing the need for extensive post-processing.
Currently, Safran produces 14 different part types using additive manufacturing, employing materials such as aluminum, nickel superalloys, and titanium. Foubert noted that AM components constitute roughly 25% of the parts in the RISE demonstrator engine, a proportion expected to be maintained in future engine programs. Advances in AM machinery are enabling the production of increasingly larger components, with projections that parts up to two meters in diameter could be additively manufactured by the early 2030s. Improvements in laser power and powder layer thickness are also enhancing productivity.
Challenges and Industry Context
Despite these advancements, Safran faces considerable challenges in scaling additive manufacturing. Transitioning from conventional manufacturing methods involves substantial costs and technical complexities. Each AM machine-tool, priced between €3 million and €5 million ($3.4 million to $5.7 million), is limited to processing a single type of metal powder. Although a single machine can produce multiple part designs, expanding the range of metal powders necessitates additional expensive equipment. These financial and operational hurdles are compounded by skepticism within the traditional manufacturing sector, where concerns persist regarding the reliability and certification of AM components.
The competitive environment is intensifying as well. Industry rivals such as Pratt & Whitney and Boeing are accelerating their investments in additive manufacturing to achieve similar benefits in weight reduction and production efficiency. Safran’s demonstration of a lighter turbine rear frame reflects a broader industry trend, yet the path forward remains both highly competitive and technically demanding.
Traditional manufacturing processes will continue to hold relevance alongside additive manufacturing. Casting remains a cost-effective solution for less complex parts and offers advanced metallurgical capabilities, including single-crystal components. Forging is expected to remain the preferred method for highly stressed parts. Eric Dalbies, Safran’s executive vice president for strategy and industrial development, stated, “Forging, casting or AM—we will pick the cheapest, as long as we preserve sovereignty.” As the aerospace industry evolves, engine manufacturers will carefully balance innovation, cost, and reliability in selecting manufacturing methods.
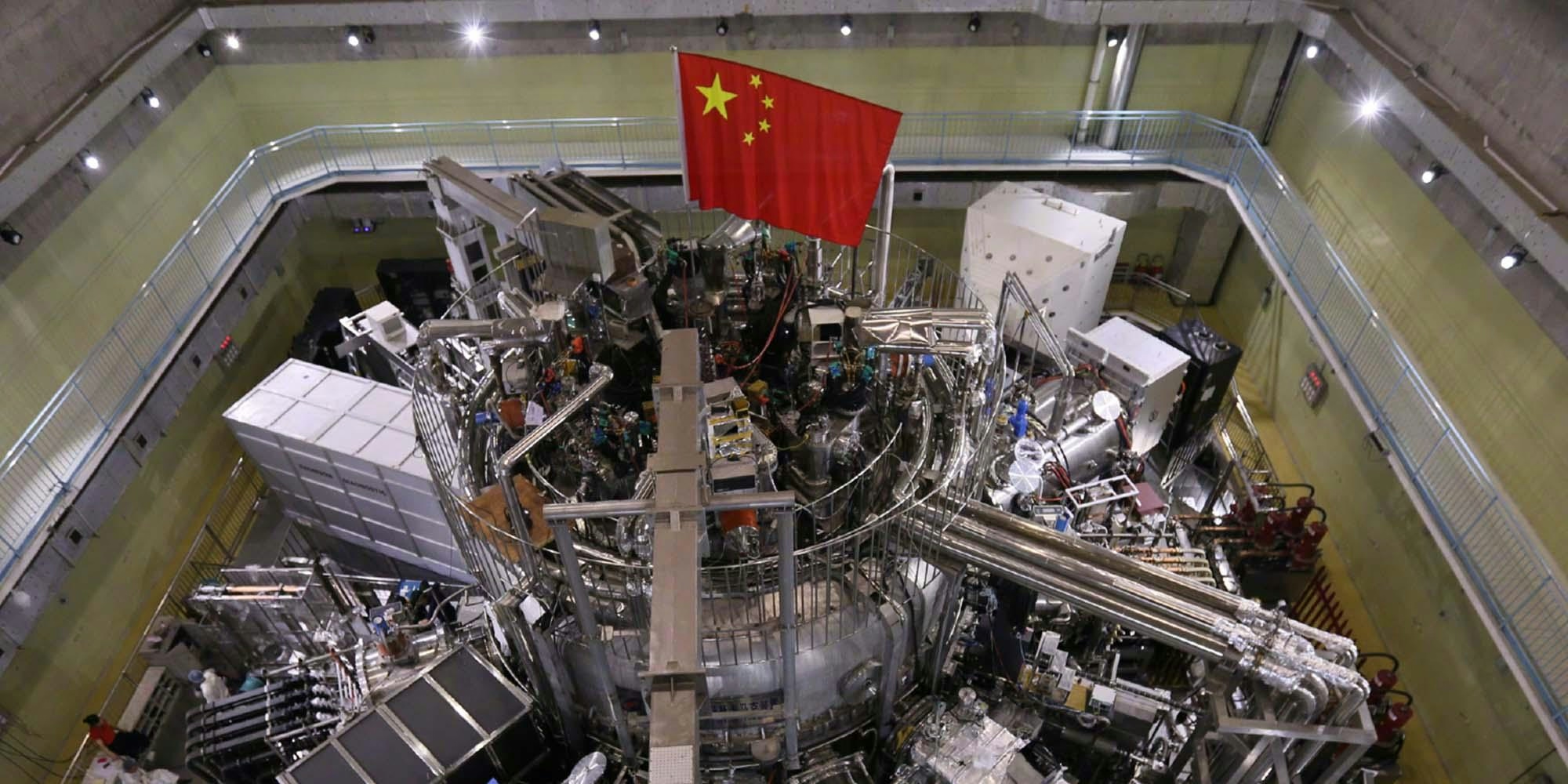
China Begins Testing Plasma-Powered Engines
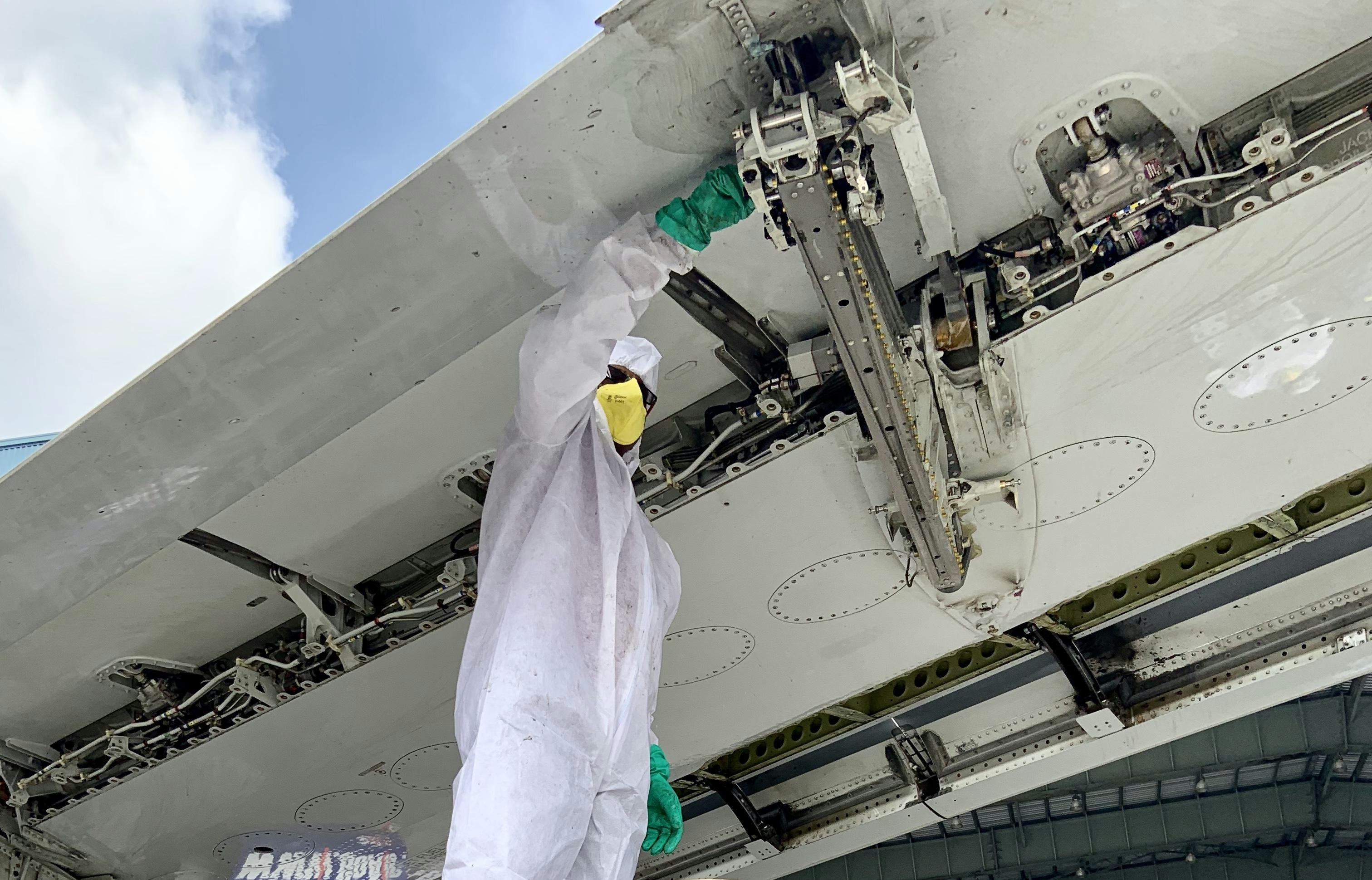
Challenges in India’s MRO Industry: Safety, Skills, and Self-Reliance
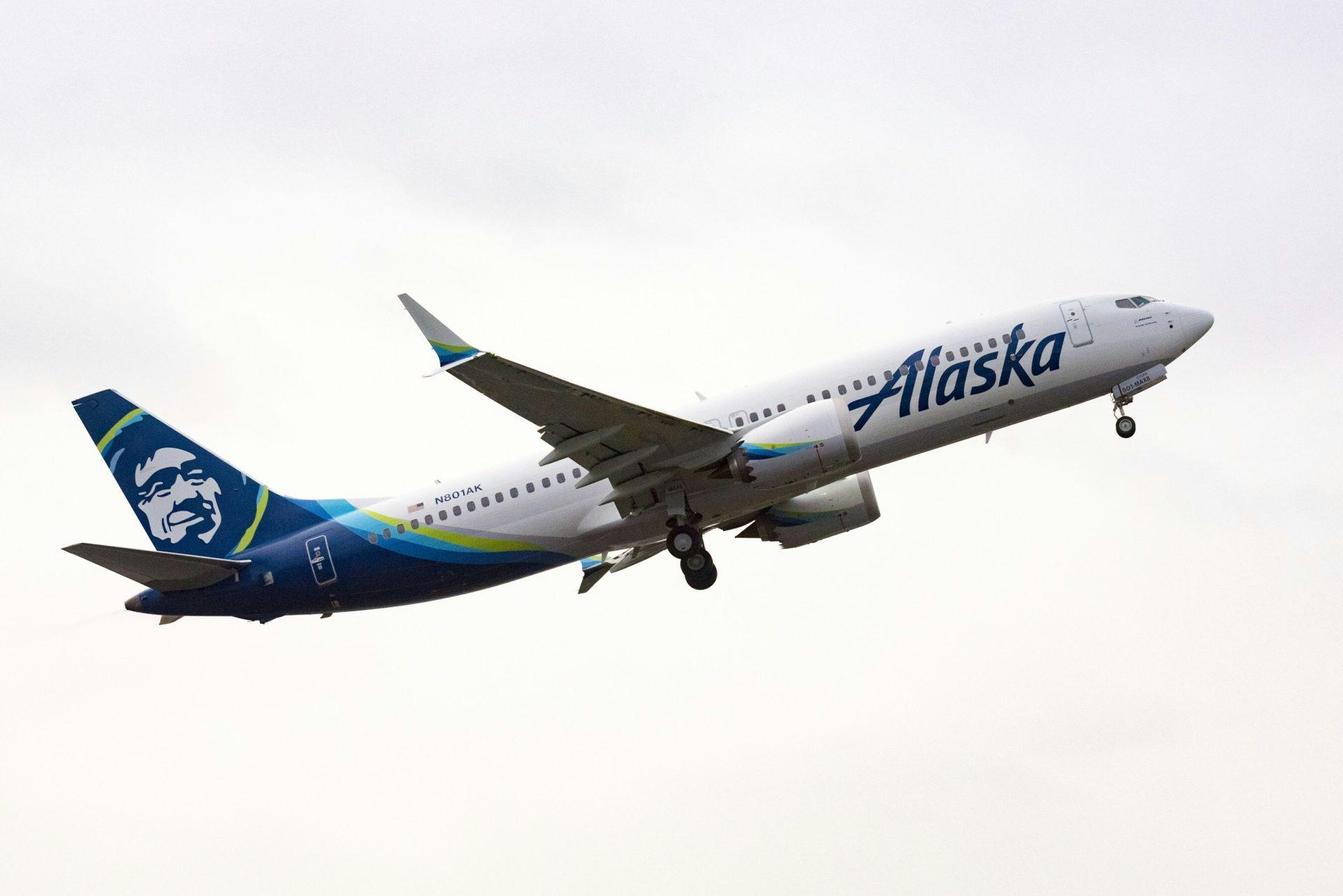
Alaska Airlines Orders Additional Boeing 787 and 737 MAX 10 Jets for Seattle Expansion

The Mystery of AI-171 Explained
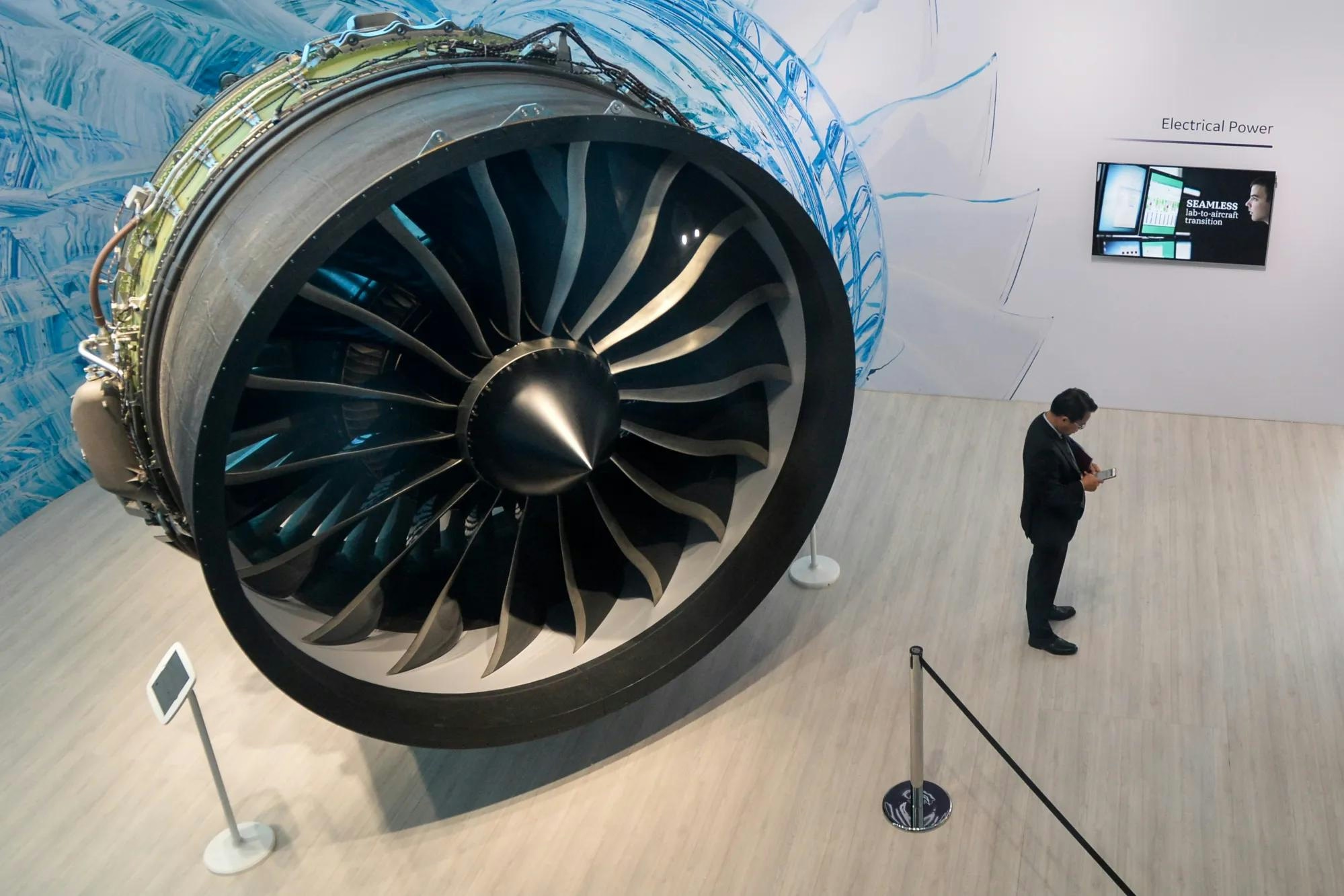
US to Lift Engine Export Restrictions to Chinese Aircraft Maker COMAC
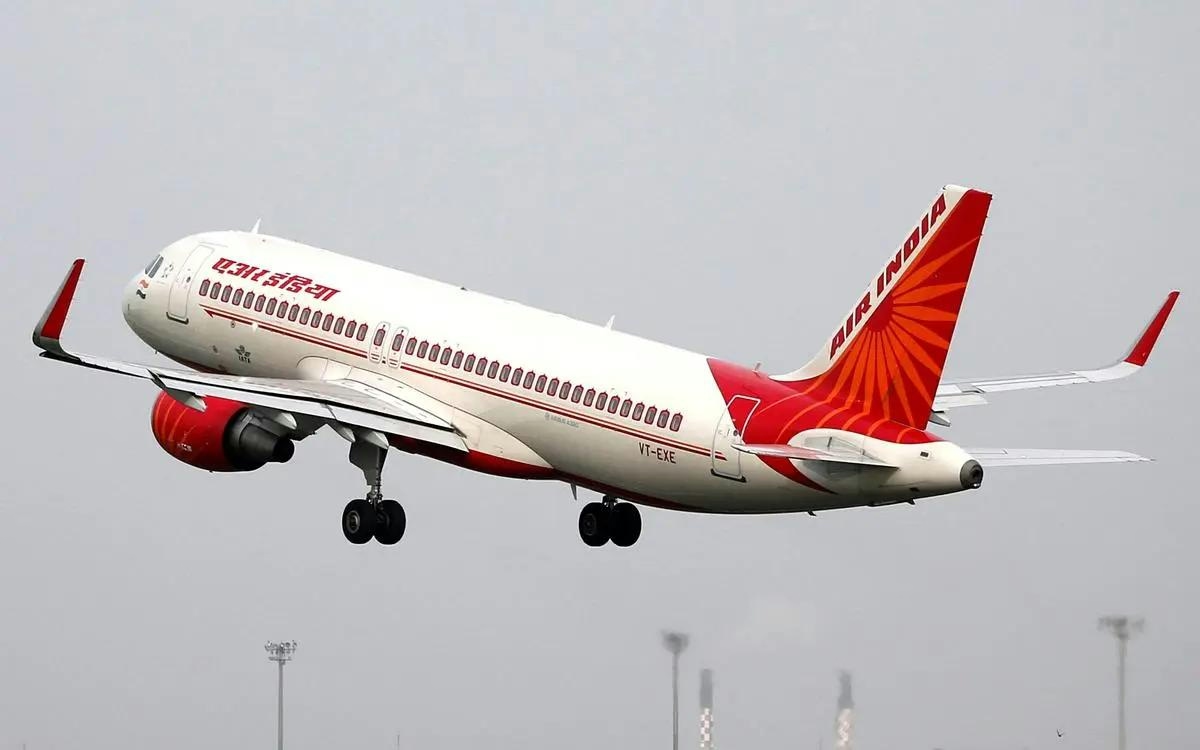
Air India Pilot Collapses in Cockpit Before Bengaluru-Delhi Flight
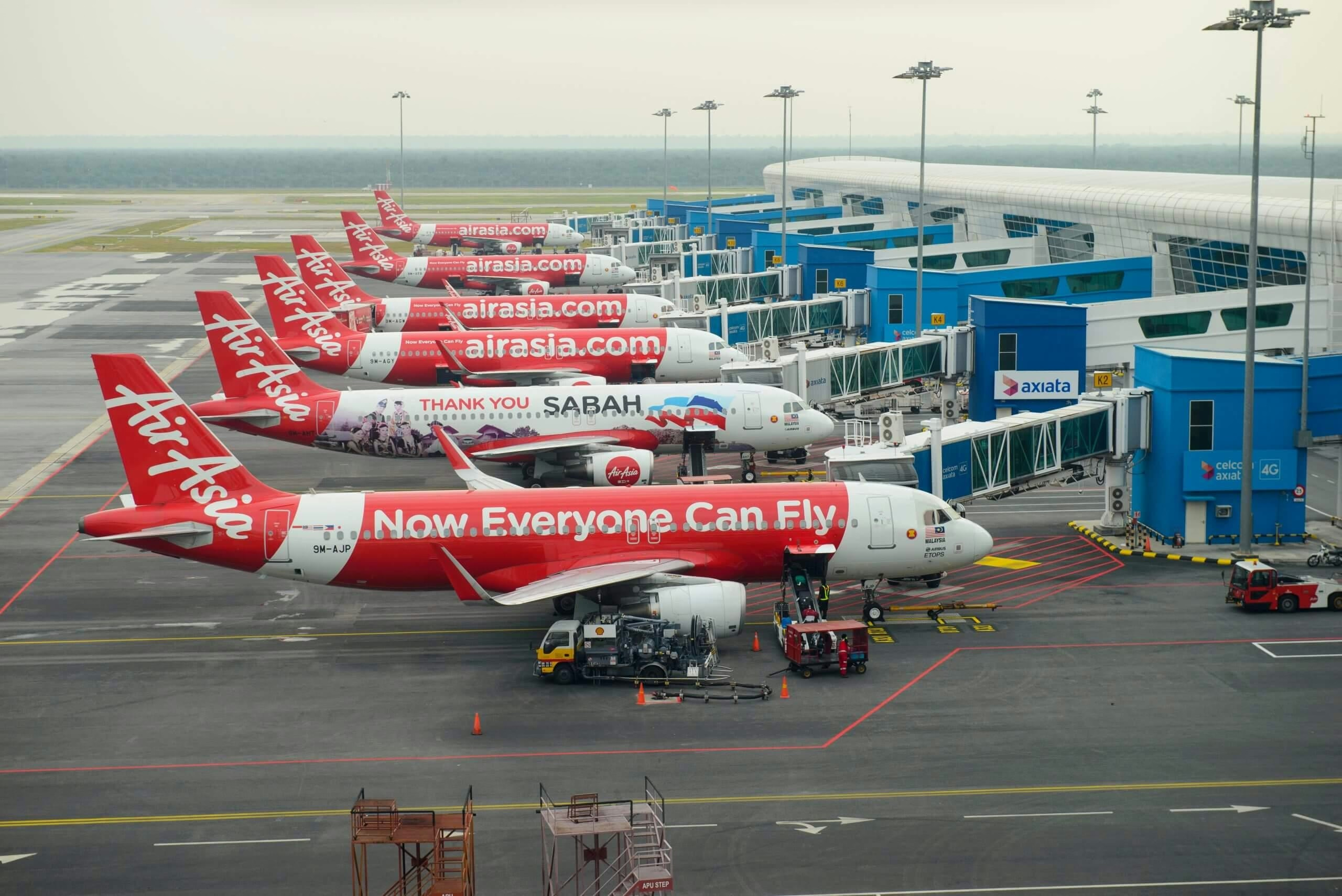
AirAsia Orders 50 Airbus A321XLR Jets as Restructuring Nears Completion
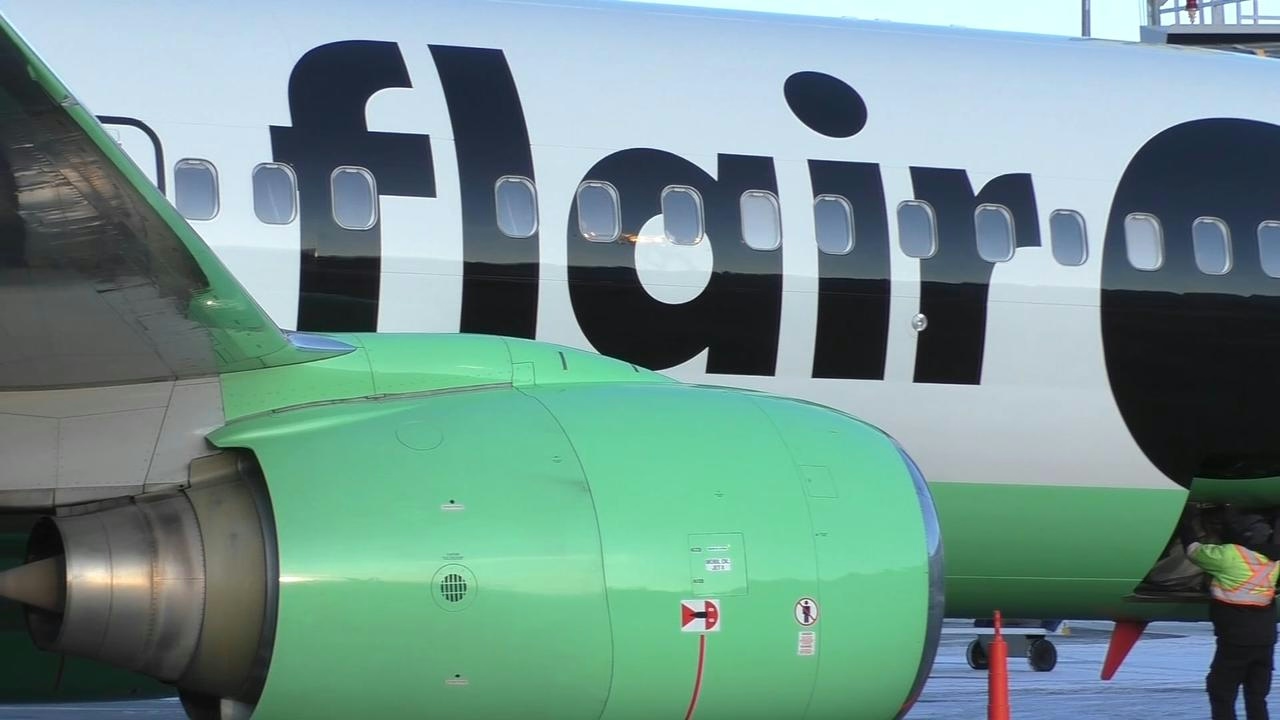
Aircraft Lessors Sue Flair Airlines Over 2023 Plane Seizures
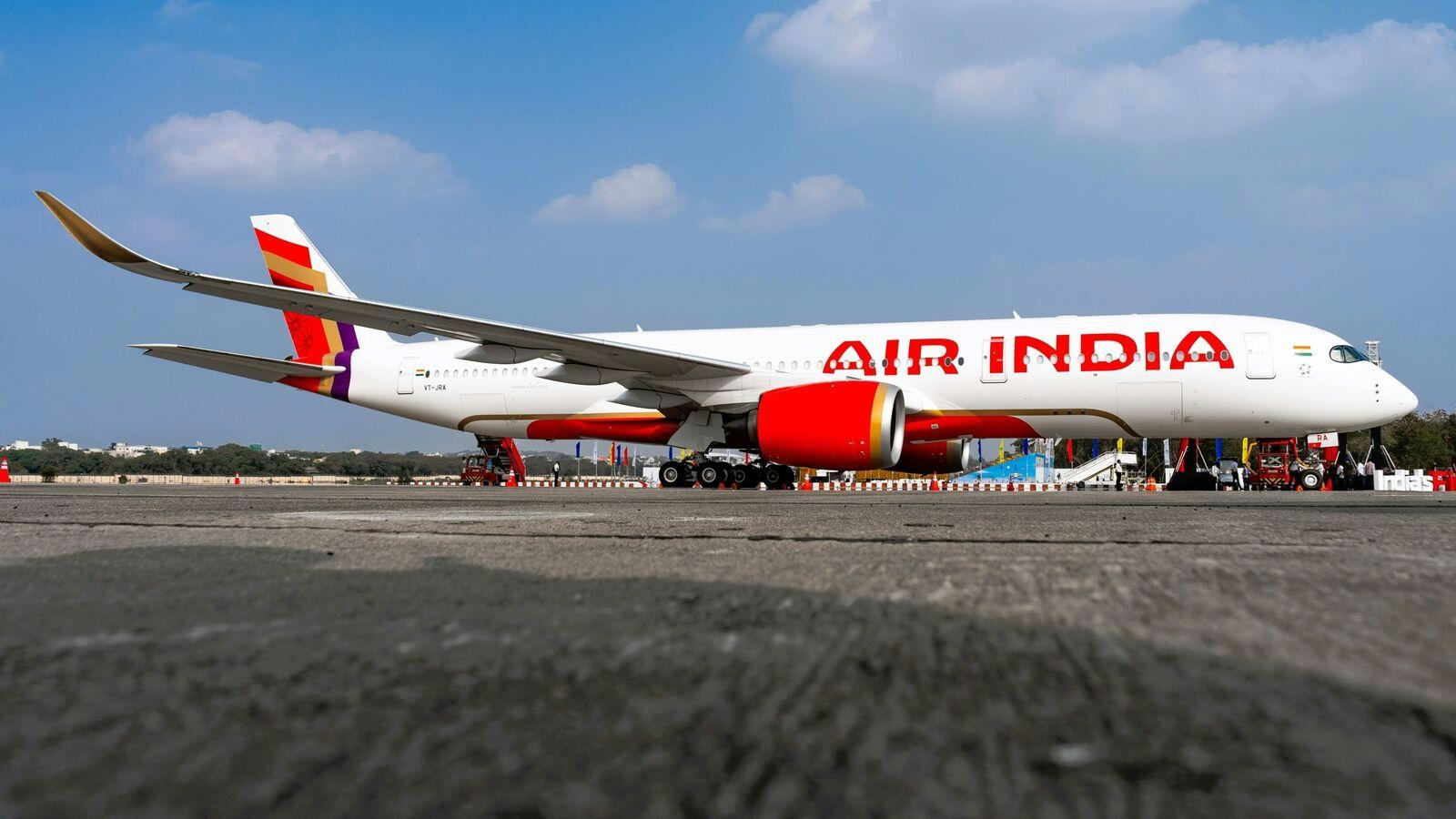
Why India’s Airline Startups Are Investing in Hybrid Fleets
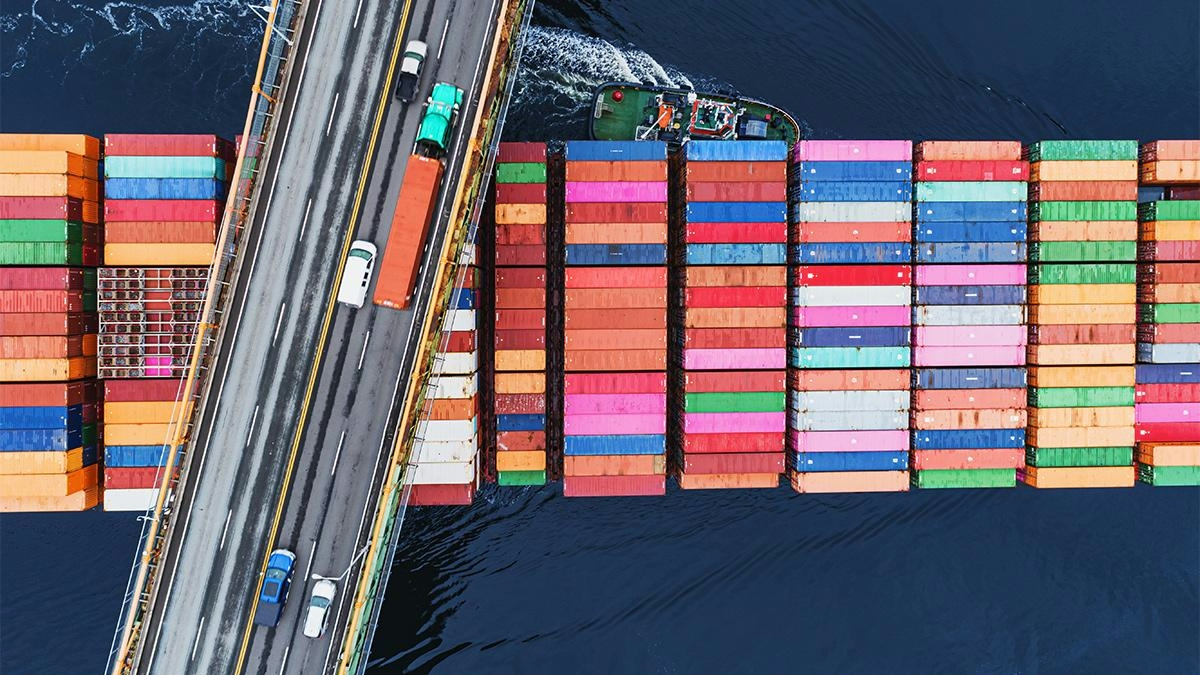