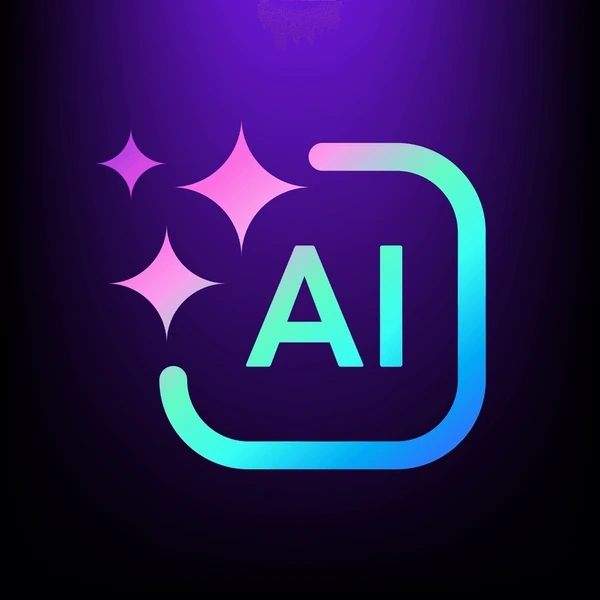
Smarter email, faster business.
How Aviation Labor Shortages Are Affecting Spare Part Sourcing
July 10, 2025
Aviation’s labor shortage isn’t just slowing repairs—it’s gutting global parts sourcing. See how MROs and OEMs are rethinking training, tooling, and supplier strategy.
Why spare part sourcing is failing
Aircraft don’t fly without parts, and parts don’t move without people. That’s the core problem facing aviation maintenance and repair operations (MROs) in 2025. A severe labor shortage has collided with global supply chain instability, creating a parts slowdown that’s impacting everything from engine overhauls to avionics replacements.
Before the pandemic, many aviation leaders viewed sourcing delays as logistical hiccups. Now, the problem is systemic. MRO providers, OEMs, and airlines are scrambling to secure not only scarce components but the skilled technicians required to inspect, install, and certify them. When those roles go unfilled, supply chain workflows jam up, aircraft get grounded, and margins get squeezed.
No matter how advanced your forecasting software or how deep your stockpile, it still takes humans to keep spare parts moving. And right now, there just aren’t enough of them.
The workforce breakdown that’s blocking the supply chain
The aviation labor shortage didn’t sneak up suddenly on the industry. This shortfall is decades in the making. Baby Boomer retirements, lackluster recruitment, and a slow certification processes have converged into a full-blown staffing crisis. According to the Aviation Technician Education Council (ATEC), the average age of aviation maintenance technicians is 54, and nearly 30% are within five years of retirement (Aviation Technician Education Council Pipeline Report).
Boeing’s 2023 Pilot and Technician Outlook forecasts that 690,000 new maintenance technicians will be needed globally by 2042—an eye-watering number that reflects both a growing fleet and a shrinking talent pool (Boeing Pilot and Technician Outlook).
Fewer certified workers on the shop floor means longer wait times for inspections, diagnostics, and component repairs. North America alone could face a shortage of 12,000–18,000 aviation maintenance technicians in 2023—which is expected to cause delays, cancellations, and the need to hold more spare parts and aircraft proactively (Avionics International, Air Transport Action Group).
Worse, the knowledge gap between veteran techs and new hires widens the productivity chasm. Training a new technician isn’t as simple as handing them a wrench. FAA regulations, OEM specifications, and airline safety protocols demand intensive upskilling. That means every unfilled role is a multiplying drag on sourcing speed.
When technicians disappear, so do the parts
Labor shortages upend repair timelines and warp the entire spare parts sourcing process. In theory, a warehouse full of rotables and expendables should cushion against delays. In reality, those inventories are only useful if personnel are available to:
- Perform incoming inspections
- Manage inventory systems
- Coordinate with OEMs
- Install and certify components
And that’s exactly where the gap is. A shortage of AMTs (Aviation Maintenance Technicians) means parts sit idle—even when available. In some cases, AOG (Aircraft on Ground) scenarios are extended by days or weeks not because the part is missing, but because no one is cleared to install it.
A June 2025 article in Flying Magazine highlights how this problem has led schools like the Aviation Institute of Maintenance to partner with carriers to fast-track technician pipelines and close sourcing-related delays (Flying Magazine). But education reform takes time and market demand doesn’t wait.
From delayed deliveries to lost orders: The ripple effect
Even before a part reaches the hangar, labor shortages upstream are making sourcing more fragile. Consider how these staffing gaps hit every node of the chain:
- OEMs: Facing their own technician attrition, original equipment manufacturers are producing parts slower than projected.
- Distributors: Understaffed logistics teams are overwhelmed with backlogs, losing track of serialized items and delaying shipments.
- MRO providers: Without enough labor to manage tracking, inspection, and installation, they're forced to reschedule service windows or cannibalize existing fleets for parts.
According to a March 2025 Satair report, spare parts backlogs now stretch over 14 years due to both labor and production delays—nearly double the pre-2019 wait times (Satair).
What’s worse: the domino effect. If one component is missing—say, a pressure transducer or a fuel control unit—an entire C-check can stall. One staffing gap becomes a full-fleet maintenance delay.
Grounded by gaps: The MRO workforce crisis
The MRO (Maintenance, Repair, and Overhaul) sector is getting hit from all sides. Retirements are accelerating, training pipelines are sluggish, and even the most resourceful MROs are struggling to retain talent. The Aviation Technician Education Council forecasts a 20% shortfall in certified AMTs by 2028 (Flying Magazine). That means fewer hands on deck to evaluate, repair, or replace aging components.
Some operators have attempted to build buffer stock or turn to PMA (Parts Manufacturer Approval) alternatives. But when you lack the trained labor to vet those alternatives, the risk of regulatory violations rises. The FAA requires that replacement parts be traceable and installed per strict compliance guidelines—something that can’t be sped up with temp labor or unvetted contractors.
And it’s not just the people doing the wrench-turning who are missing. Procurement officers, QA specialists, and inventory control managers are also in short supply. This leads to errors in part tracking, longer RFQ cycles, and missed expiration dates on life-limited parts. In short, labor gaps at MROs don’t just slow repairs—they compromise sourcing quality itself.
Contracting out: A short-term fix with long-term costs
With their own MRO rosters shrinking, airlines and operators are increasingly outsourcing both maintenance and sourcing logistics. This trend has exploded post-2021, especially for regional carriers and cargo operators without in-house parts programs.
Outsourcing can temporarily plug holes in labor-strapped teams—but it comes at a cost:
- Less visibility into the sourcing chain
- More dependency on third-party compliance
- Increased turnaround times due to contractual bottlenecks
- Higher per-part prices due to margin stacking
According to a June 2018 FAA Human Factors newsletter, mismatches in contract maintenance documentation have led to maintenance delays, miscommunication, and agency findings (FAA). Contracting out sourcing and repairs doesn't eliminate labor issues; it simply shuffles them further down the chain, where oversight is thinner and coordination is harder.
Training lag time and the certification bottleneck
Even when airlines and MROs recruit aggressively, the time it takes to get a new technician fully operational is considerable. FAA Part 147 programs require 18 to 24 months of classroom and practical training, followed by certification exams and often additional OJT (on-the-job training). This pipeline simply isn’t built for speed (FAA Aircraft Maintenance Technician Schools).
Aviation Institute of Maintenance (AIM), the largest aircraft mechanic school in the U.S., is working to close that gap by partnering with major carriers to fine-tune training curricula and speed up job readiness (Aviation Institute of Maintenance). Their advisory board includes execs from American, United, Southwest, and others who’ve helped tailor coursework to real-world needs (Flying Magazine).
But no matter how fast schools move, there’s no escaping the regulatory guardrails. Adherence creates a cascade of delays. When fewer certified techs are available, fewer parts get inspected, installed, or tagged for return-to-service, leading to an increase in aircraft-on-ground (AOG) situations and reliance on expedited ( expensive) sourcing and logistics.
When retirees walk, tribal knowledge goes with them
There’s another element to the labor crisis that rarely makes headlines but hits hard on the sourcing side: the departure of tribal knowledge. Veteran maintenance pros have invaluable insider information. They know which vendors ship on time, which alternate part numbers are cross-compatible, and how to expedite a part swap without blowing compliance.
When these workers retire, and they're doing so in droves, that practical knowledge also disappears. That leads to avoidable errors, sourcing delays, and greater dependency on documentation and external vendor support. One United Airlines insider described the retirement wave as “watching your troubleshooting library walk out the door, one chapter at a time” (FAA).
Operators that fail to capture this knowledge in standardized systems or AI-driven knowledge bases are particularly vulnerable. Their sourcing teams must relearn lessons the industry has already paid for—costing time, compliance, and money in the process.
Grounded by gaps: The AOG impact
Aircraft-on-ground (AOG) events are the most visible and costly consequence of the labor and sourcing pinch. When an aircraft can’t return to service due to a missing part and no qualified mechanic to install it, this can cost airlines between $10,000 and $150,000 per hour (AAA Air Support).
While many industry insiders hotly contest the hourly cost of AOG events, everyone agrees that an AOG is financially catastrophic. AOG events are just much a staffing failure as a sourcing one. Short-staffed MROs can’t turn wrenches fast enough to close the maintenance loop, which means even when parts are in-hand, they don’t reach their needed destinations in time.
As a 2023 Satair report notes, “Persistent shortages of critical components—including engines, avionics and landing gear—combined with a maintenance workforce stretched thin, means lead times are getting longer, not shorter” (Satair).
Collaboration as a pressure valve
Some in the industry are responding not with competition but greater collaboration. MROs, OEMs, and suppliers are experimenting with joint procurement agreements and shared technician pools to ease the burden.
In Europe and Southeast Asia, for example, airline alliances have begun coordinating maintenance scheduling to avoid AOG overlaps and smooth out peak labor demand.
Satair’s 2025 MRO Outlook suggests that “collaborative strategies, such as joint procurement, diversified suppliers, and stockpiling high-demand parts, can buffer against unexpected shortages and minimize maintenance-related delays” (Satair).
While “buffering against” is not a perfect fix, it is a promising shift. Shared data systems can also improve real-time visibility into inventory and labor availability, helping airlines and MROs make smarter sourcing decisions—before parts go critical.
Training pipelines and the talent vacuum
At the heart of the labor crisis is the broken labor pipeline. The average age of an aircraft mechanic in the U.S. is well over 50, and thousands are expected to retire by the end of the decade (Flying Magazine). Yet the influx of new technicians isn’t keeping pace. The FAA issued fewer new A&P certificates in 2023 than in 2014, a stark signal that the system is leaking talent faster than it’s replacing it.
Training bottlenecks are partially to blame. Aviation programs struggle with outdated curricula, a lack of modern equipment, and minimal exposure to the digitized environments of today’s hangars. And because certification takes time and tuition, potential entrants often opt for quicker, more lucrative trades, like automotive repair or renewable energy.
Institutions like the Aviation Institute of Maintenance (AIM) are trying to plug the gaps. AIM’s recently created industry advisory board with representatives from major domestic carriers is making sure technician curricula aligns with current, real-world needs.
“We’re going to become a powerhouse and maintain that long term in the future,” said AIM’s Chief Aviation Officer Bill Brown, “and we think that’s going to help solve the problem that’s out there… in the huge gap between what jobs are going to be needed and what is available” (Flying Magazine).
Forecasting the fallout: What happens if we don’t fix this?
If labor and sourcing pressures continue unchecked, the entire MRO system could buckle. While the 2023 Boeing Pilot and Technician Outlook forecasted a need for 690,000 new maintenance technicians by 2042, reports released a year later increased that projected an increased worker shortfall of 716,000 (Satair).
Missed flights, delayed deliveries, and idle aircraft could become the new normal. In spite of growing demand, airlines may be forced to sideline fleet expansion plans. Even with available aircraft, planes can’t fly if there’s no one there to maintain them.
And in an industry where margins are already razor-thin, the cost of reactive maintenance and chronic AOGs would likely destabilize many carriers already walking the financial tightrope.
Some MROs have begun outsourcing maintenance to countries with lower labor costs, but this creates new risks: longer turnaround times, geopolitical exposure, and inconsistent safety oversight.
FAQs
Why are younger generations hesitant to pursue or stay in aviation maintenance careers?
While aviation maintenance offers stability and competitive pay, younger workers often hesitate to enter—or stay in—the field due to lifestyle misalignment and workplace rigidity.
Gen Z technicians increasingly prioritize work-life balance, flexibility, and career mobility. One Aviation Week panelist noted that “people were leaving and even taking a pay cut to get weekends off,” prompting AAR Corp. to restructure technician shifts for more predictable schedules (Aviation Week).
Digital engagement also matters. Newer techs want purpose-driven work environments where their voices are heard. Turkish Technic saw success with a digital portal where employees submit improvement ideas and received over 700 suggestions a year (Aviation Week).
Meanwhile, training attrition is staggering: One European airline reported losing 80% of technician trainees before certification. The challenge isn’t just recruitment—it’s retention in a generation that doesn’t want to work 30 years in the same role.
How does standardizing an aircraft fleet impact labor and spare parts sourcing?
Fleet standardization simplifies maintenance and inventory needs, but increases sourcing risk. Southwest Airlines operates an all-Boeing 737 fleet in a model of strategic simplification. With fewer aircraft types, they reduce parts variety, improve technician specialization, and streamline inventory (RM Study Group).
But this trade-off creates dependency and operational vulnerability. If a specific Boeing 737 part is delayed or recalled, the entire fleet can be grounded. Southwest mitigates this by stockpiling high-risk parts and diversifying component suppliers, but it doesn’t eliminate the risk. What seems like an efficient sourcing model can quickly become a bottleneck if one vendor falters or a design flaw emerges.
How did previous generations overcome AMT labor shortages?
They didn’t. They didn’t have to; these AMT labor shortages are a new problem.
Traditionally, there was always a robust and well-trained talent pool to pull from. Past generations of “new” air mechanics gained experience in military roles or smaller machinist shops before moving to major carriers.
That progression no longer exists. Young workers are no longer gaining practical, job-transferable skills through compulsory service, and airlines are now hiring technicians straight out of school and pulling from the same limited talent pool as MROs (Aviation Week).
There’s also a class perception issue. Since the 1970s, there’s been a strong cultural bias for college (over skilled trades) as the pathway to success. While college-level work today offers less job security and often comes with sky-high student loan debt, it’s largely viewed as more desirable.
Technician work, by contrast, is stable, high-paying work and with affordable tuition fees to break into the field, not to mention critical to domestic infrastructure and public safety (U.S. Government Accountability Office). AMT work may need a major social rebranding.
Grounded by gaps: Turning a crisis into collaboration
The labor shortage before us is alarming, but at least the crisis is no longer invisible.
Airlines, MROs, suppliers, and training institutions are beginning to act, forming advisory boards, investing in hybrid training models, and exploring automation for diagnostics and skilled tasks like borescope inspections and precision part installation (AviTrader, GE Aerospace).
Many industry leaders suggest that collaboration is the most viable route forward, advocating for pooled procurement, shared inventory networks, and better alignment between OEMs and MRO providers (Satair). Others are pushing for fast-track certifications and modular coursework to fill gaps faster.
But time is short. With aircraft deliveries expected to double by 2034 and thousands of techs retiring each year, the industry must confront its vulnerabilities now or risk grounding itself under the weight of its own complexity.
Need help navigating sourcing delays and tech shortages?
ePlaneAI helps MROs and aviation suppliers optimize sourcing despite workforce constraints. With predictive demand planning, intelligent part-matching, and secure integrations with your existing ERP system, we help you keep fleets flight-ready—-even in a labor-challenged market.
👉 Explore how ePlaneAI can support your sourcing strategy. Schedule a demo today!
Aviation Maintenance Trends That May Gain Momentum in Uncertain Circumstances
Aircraft are staying in service longer, supply chains are a powder keg, and the tech is evolving overnight. Discover the maintenance trends gaining momentum and what they mean for operators trying to stay airborne and profitable.
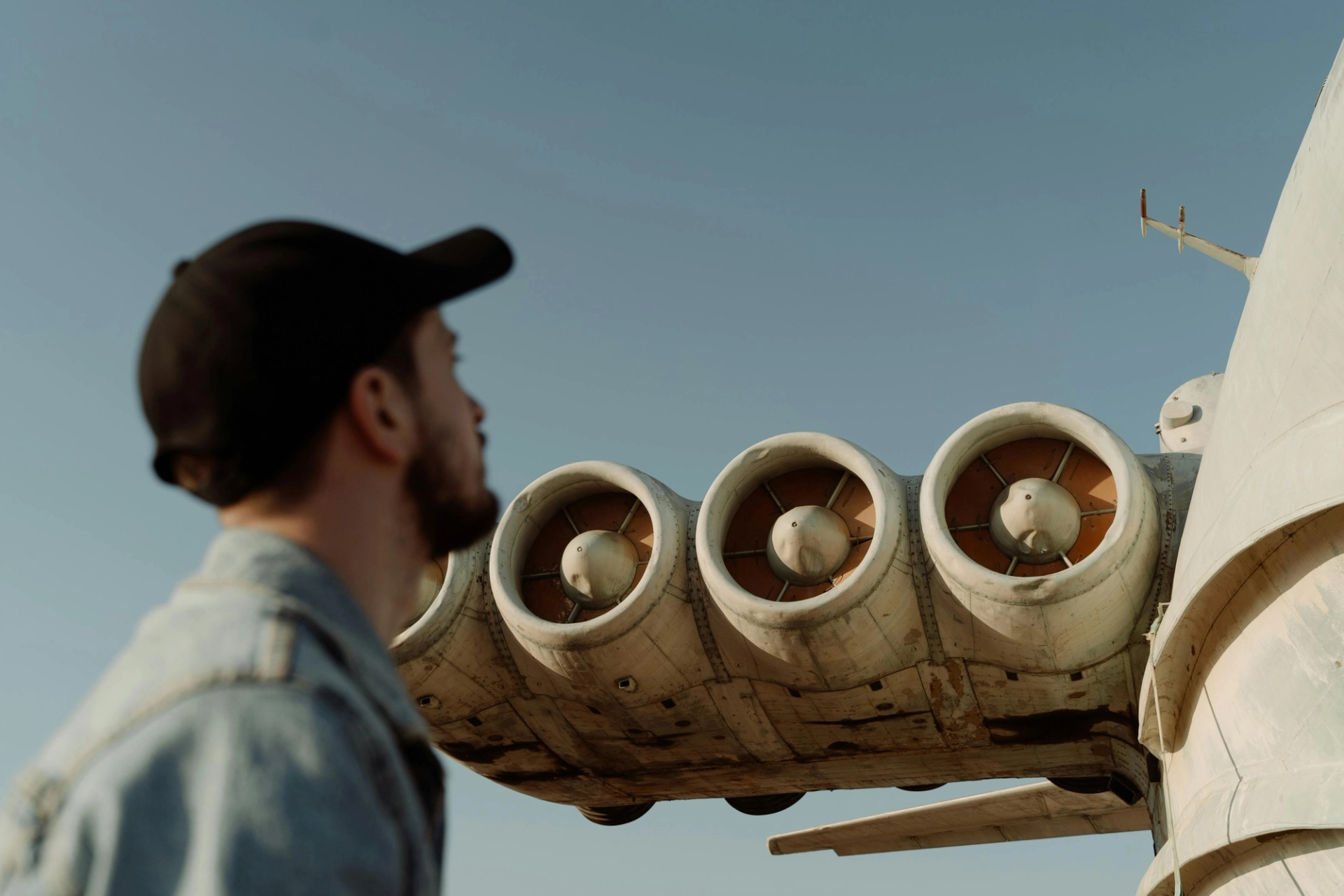
August 25, 2025
What Is Parts Manufacturer Approval (PMA) and Why Is It Important in Aviation?
PMA parts are transforming aviation—cutting costs, improving performance, and reducing downtime. Learn why FAA-approved PMA components are becoming a go-to choice for airlines, MROs, and OEMs alike.
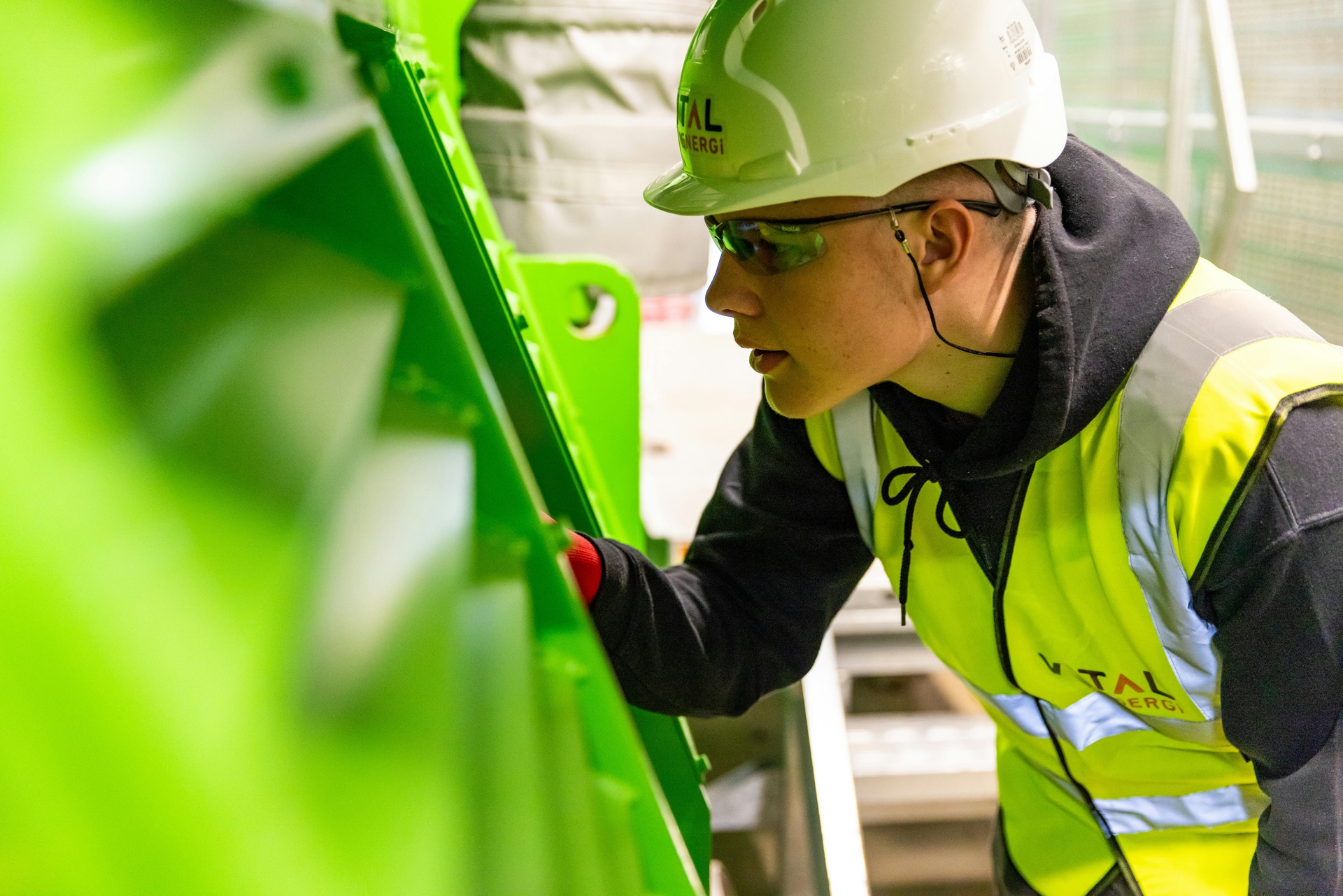
August 22, 2025
How to Manage Your Aircraft Maintenance Team With Schedule AI
Tired of manual maintenance scheduling headaches? Meet Schedule AI. See how Schedule AI is transforming aircraft operations, helping your team optimize tasks and drastically cut down turnaround times. Keep your fleet in the air and on schedule.
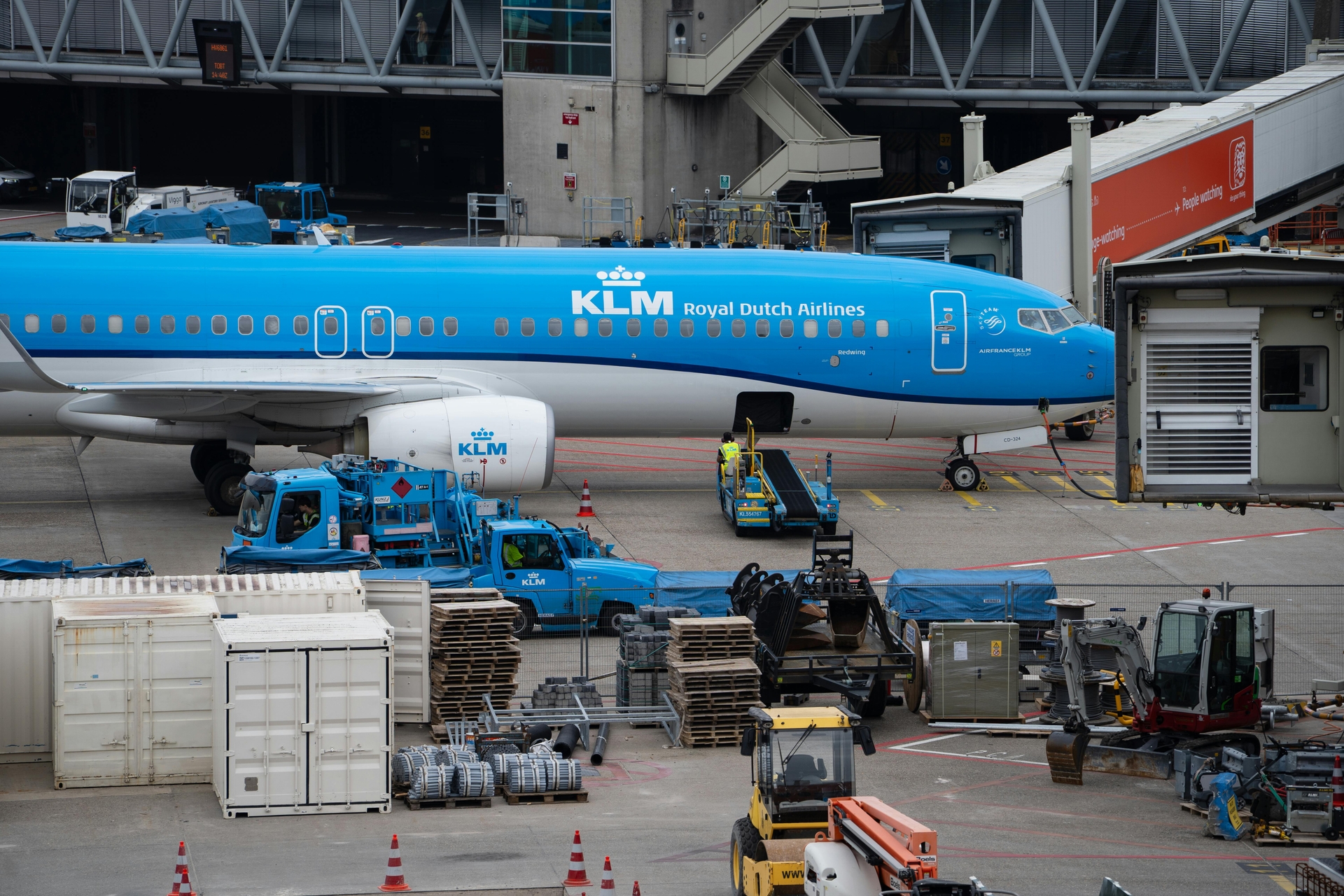
August 20, 2025
Aircraft Part Shipping Strategies That Work for Your Business
From urgent AOG shipments to oversized engine freight, better aircraft part shipping strategy matters. Learn the most effective ways to move high-value aviation parts safely, quickly, and cost-efficiently.
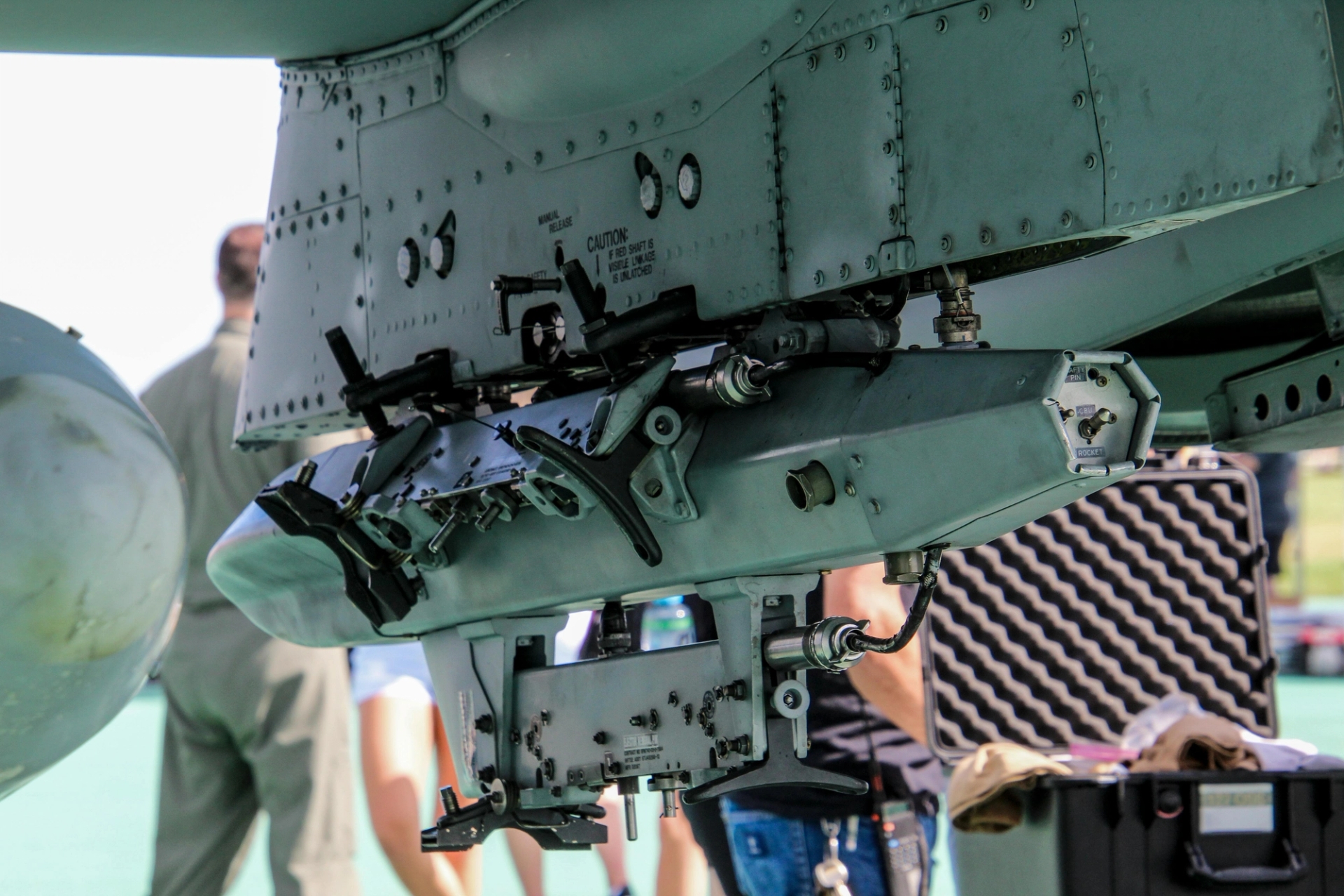