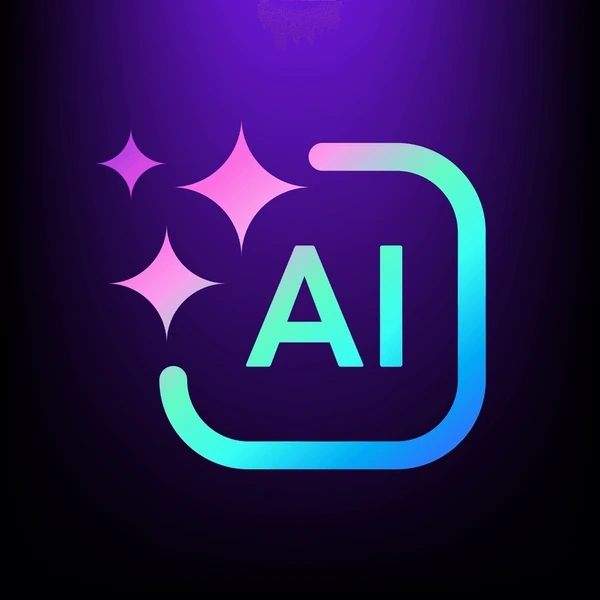
Smarter email, faster business.
Schedule AI. Real-Time Optimization of MRO Scheduling.
June 14, 2025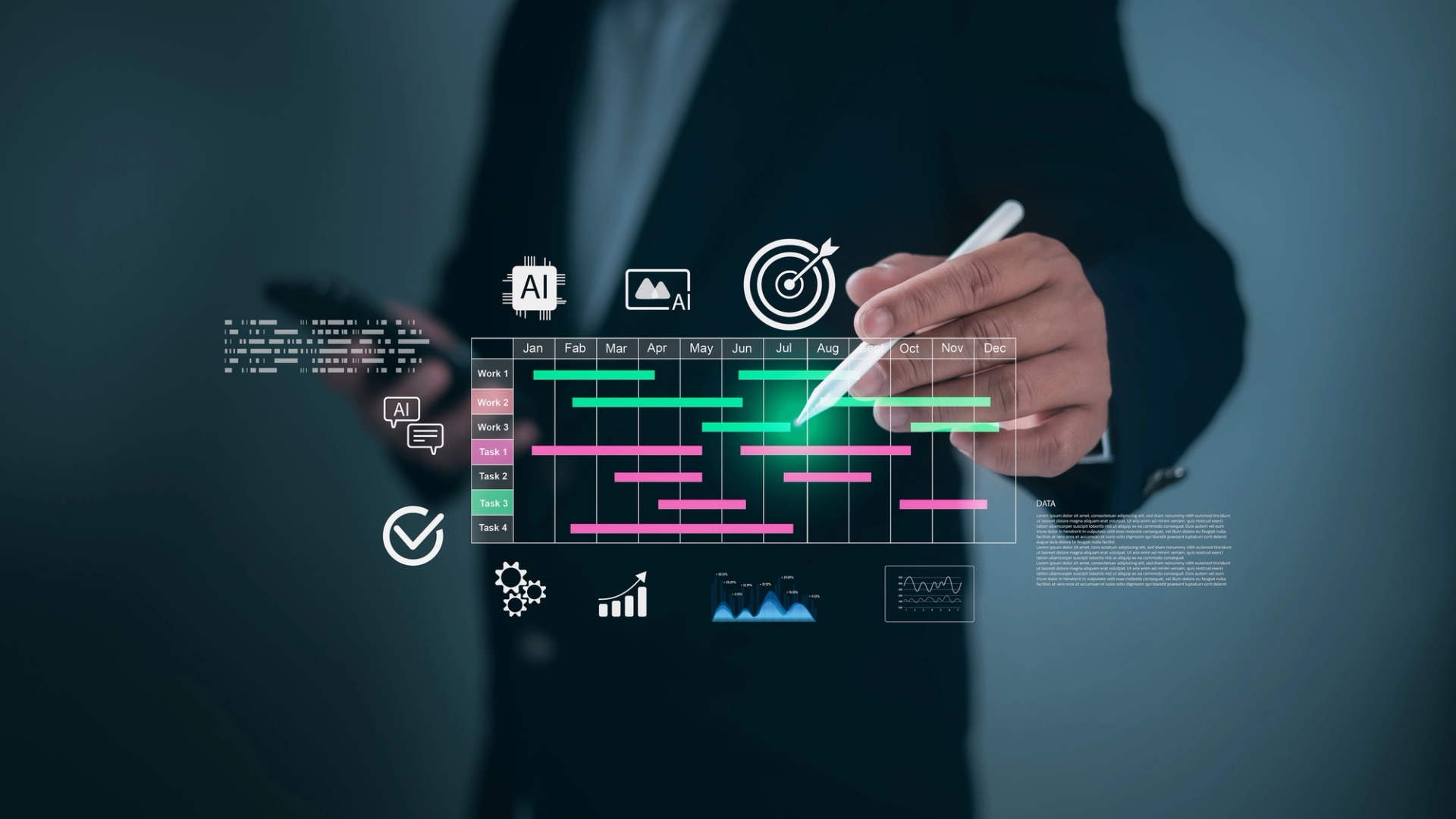
Maintenance, Repair and Overhaul (MRO) scheduling in aviation and manufacturing involves allocating skilled technicians, tools, parts, and hangar space to maintenance tasks under tight time constraints. Traditional methods (manual or legacy ERP planning) struggle with unpredictable breakdowns and diverse task requirements . In today’s “smart era,” AI-driven scheduling systems consider a wide range of variables – technician skills, certifications, location, parts availability, etc. – to create optimal work plans . For example, modern AI schedulers “consider countless variables — skills, certifications, location, parts availability — to create the most efficient plan,” learning from past jobs to optimize future schedules . Schedule AI applies this concept to MRO by continuously analyzing live data and using machine learning to predict, allocate, and optimize maintenance tasks in real time .
Key Challenges in MRO Scheduling
- Unpredictable Demand: Urgent repairs or AOG (Aircraft on Ground) events can arise suddenly, forcing immediate rescheduling under severe time pressure .
- Skill Matching: Each maintenance job requires specific technician skills and certifications. Manually matching tasks to qualified personnel is slow and error-prone; an AI system must automatically align job requirements with worker skill profiles .
- Resource Constraints: MRO facilities have finite capacity. Schedule AI must account for limited bays, platforms, and spare parts. For example, it can forecast how long an aircraft may occupy a maintenance bay, allowing teams to optimize hangar usage and avoid conflicts .
- Data Silos: Information about technicians, parts, and work orders often resides in separate systems. Schedule AI integrates data from the ERP, inventory, and maintenance logs so decisions are based on complete, up-to-date information .
How Schedule AI Works
For each incoming maintenance request, Schedule AI follows an automated workflow:
- Request Intake & Classification: The new work order is ingested by the system, which identifies the task type, required skills, parts, and urgency.
- Technician & Resource Matching: The AI queries the skills database to find available mechanics whose certifications match the job requirements . It automatically assigns the “best-fit” technicians to each task, ensuring the right expertise is applied and minimizing repair time .
- Duration & ETA Prediction: Using historical maintenance data (past task durations, technician performance, fault types), the system predicts how long the job should take under current conditions . This provides an estimated completion time.
- Schedule Optimization: The AI formulates a scheduling problem that considers technician availability (shifts, contracts, legal limits), facility capacity (available hangars/bays) , and parts availability. It then computes an optimized schedule that minimizes idle time and avoids resource conflicts.
- Continuous Rescheduling: As work proceeds, real-time updates (e.g. a task running long or a new urgent request arriving) trigger on-the-fly adjustments. The system “continually analyzes and adjusts schedules” to juggle resources and demands, ensuring tasks stay on track . This tight feedback loop prevents delays and repeat issues .
Throughout this process, Schedule AI operates within the enterprise’s existing ERP system. It runs as a cloud-based optimization engine in the background, reading live data (flight schedules, inventory, crew rosters) and writing optimized assignments back into the ERP. ePlane AI notes that its solution “works with SAP, Snowflake, Oracle, AMOS, Quantum, and other aviation systems” , so no separate dashboard is required – planners simply see updated schedules in their familiar interface. By augmenting the ERP rather than replacing it, Schedule AI creates a closed-loop optimization pipeline that continuously fine-tunes the maintenance plan.
ML Models for Skill Matching
Technician profiles and task requirements are encoded as high-dimensional vectors so that “semantic” matching can be done automatically. For example, resume/CV text or structured skill tags can be converted into embeddings (e.g. via transformer-based encoders like BERT/Sentence-BERT) . In practice one may even compute separate embeddings for different aspects of a technician’s profile (skills, experience history, certifications, etc.) . A simple nearest‐neighbor or cosine‐similarity lookup in this embedding space can then find the closest technicians for a given task. More advanced ML models (fine-tuned transformers or neural “Siamese” networks) can learn to score (task, technician) pairs based on historical assignment data: using past maintenance logs and outcomes, the model is trained so that technicians who successfully completed similar tasks have high similarity scores. This historical training data might consist of (task-description, technician, outcome) triples from the CMMS/ERP. In summary, skill matching can use anything from k-NN on skill vectors to deep embedding models. Recent work shows that contextualized embeddings improve matching quality over static word vectors , and multi-component embeddings (experience vs. education vs. skills) allow nuanced weighting of each factor .
ETA Prediction Models
Once a technician is selected, the system estimates how long the job will take. This is posed as a regression problem: features include task attributes (type, complexity, aircraft model), technician factors (individual efficiency, skill level), parts availability (lead times, delays), and shop conditions (shift, workload). Common choices are tree‐ensemble regressors (XGBoost, Random Forest) or deep networks. For instance, an aviation maintenance study combined XGBoost and LSTM models (plus SVR) to predict jet‐engine Remaining Useful Life – similarly, XGBoost/RandomForest on tabular features often excel in ETA prediction. If there is rich time-series context (e.g. sequences of tasks), recurrent models (LSTM/GRU) or recent Transformer‐based time-series models (Informer, Autoformer, Temporal Fusion Transformer, etc.) can be used to capture temporal patterns . The models are trained on historical maintenance records: each past task’s actual duration (adjusted for delays) forms the target. Part-delivery delays, technician ID, and ambient factors (shift, equipment availability) are input features. The trained model outputs a probability distribution or point estimate for task duration, which we interpret as the predicted ETA. (In practice, one would evaluate these models on held-out historical tasks to validate accuracy before deployment.)
Optimization Algorithms
The scheduling engine uses AI optimization to assign tasks to timeslots and techs under constraints. Common approaches include constraint programming (CP) solvers, mixed-integer programming, metaheuristics, and reinforcement learning. For example, a recent study applied a CP solver to MRO tasks and showed it could schedule engine inspections/repairs with ~99.3% resource utilization . Genetic algorithms and swarm methods have also been used: in heavy-maintenance scheduling, GAs have been shown to minimize overall makespan under resource constraints . Tran et al. applied ant-colony optimization (ACO) to MRO scheduling, targeting minimal total processing time and tardiness while adapting dynamically to shop-floor changes . Reinforcement learning is an emerging approach: Silva et al. (2023) framed maintenance scheduling as an MDP and trained policies (e.g. via PPO) to place routine tasks in calendar slots. Their combined static/adaptive RL solution produced efficient plans that reduced ground time and increased schedule flexibility .
These optimization layers typically operate in a loop with the prediction models. For instance, a CP or GA scheduler may take the predicted ETAs as input, generate a candidate schedule, and then simulate outcomes; if a simulated delay or new task appears, the system can re-run optimization (adaptive scheduling). In practice ePlane AI’s solution is cloud-native, integrating via API with an airline’s ERP/MRO system (e.g. IFS, AvSight, SAP) to pull in data and push schedule updates. The backend might run on a Kubernetes cluster or serverless environment, with microservices for ML inference and a solver (e.g. OR-Tools CP-SAT or Gurobi for MIP) to compute optimized rosters in real time.
Example Workflow
A simplified scheduling flow might look like:
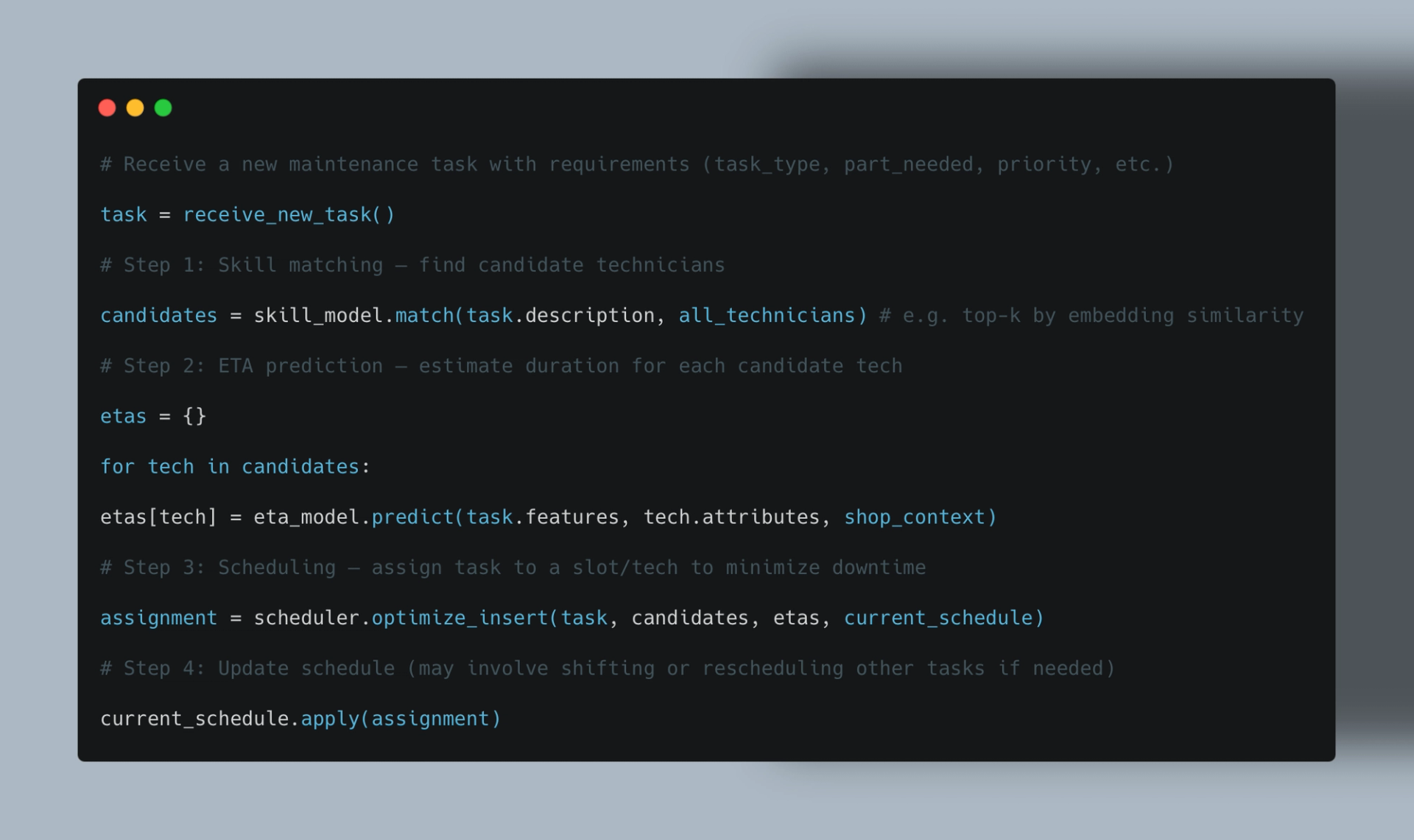
More concretely, one could call a machine learning service to rank skills and another to predict task durations, then call an optimization API (CP solver or GA) to rebuild the schedule.
As new tasks or delays occur, this loop repeats – triggering re-optimization. For example, if a high-priority AOG task arrives, the system can rerun skill matching and ETA estimates for all pending tasks and use the solver to find a new optimal assignment. This continuous feedback loop of predict → optimize → simulate → repeat ensures schedules are “real-time” and skill-aware.
AI-Driven Scheduling Benefits
Schedule AI delivers significant improvements in efficiency and utilization. Key impacts include:
- Increased Productivity: Aligning tasks to best-fit technicians can boost labor output by about 30% . Technicians spend more time doing the work they are most skilled at, with fewer delays due to skill mismatches.
- Reduced Downtime: Intelligent scheduling and predictive insights lead to fewer unscheduled maintenance events. For example, integrated failure prediction can cut unexpected breakdowns by ~20% , keeping aircraft and equipment in service longer.
- Optimized Resource Use: By forecasting workload and bay occupancy, the AI ensures that hangars and equipment are used continuously without conflicts . Inventory-aware scheduling also guarantees that required parts are on hand, avoiding costly wait times. Overall, AI-driven resource allocation makes sure “the right resources are available at the right time and place” .
- Faster Turnaround: With proactive allocation of staff and parts, maintenance jobs are completed more predictably. Planners can avoid last-minute bottlenecks, and crews benefit from seeing all needed information (past fixes, bulletins) in one place. As one MRO leader notes, this tight AI-assisted loop “not only saves time but also helps prevent repeat issues” .
In summary, Schedule AI transforms MRO scheduling into a dynamic, data-driven process. It continuously matches incoming tasks to technician skills and facility capacity, and adapts in real time to the shop’s changing state . Industry surveys reflect this shift: over 80% of aerospace and defense organizations report they’re using or planning to use AI to optimize MRO operations . By embedding the AI optimizer into existing systems , companies gain smarter, faster scheduling with no new interfaces. The result is a more efficient maintenance operation – less downtime, higher productivity, and lower costs – fulfilling the promise of real-time, AI-driven scheduling.
Aviation Maintenance Trends That May Gain Momentum in Uncertain Circumstances
Aircraft are staying in service longer, supply chains are a powder keg, and the tech is evolving overnight. Discover the maintenance trends gaining momentum and what they mean for operators trying to stay airborne and profitable.
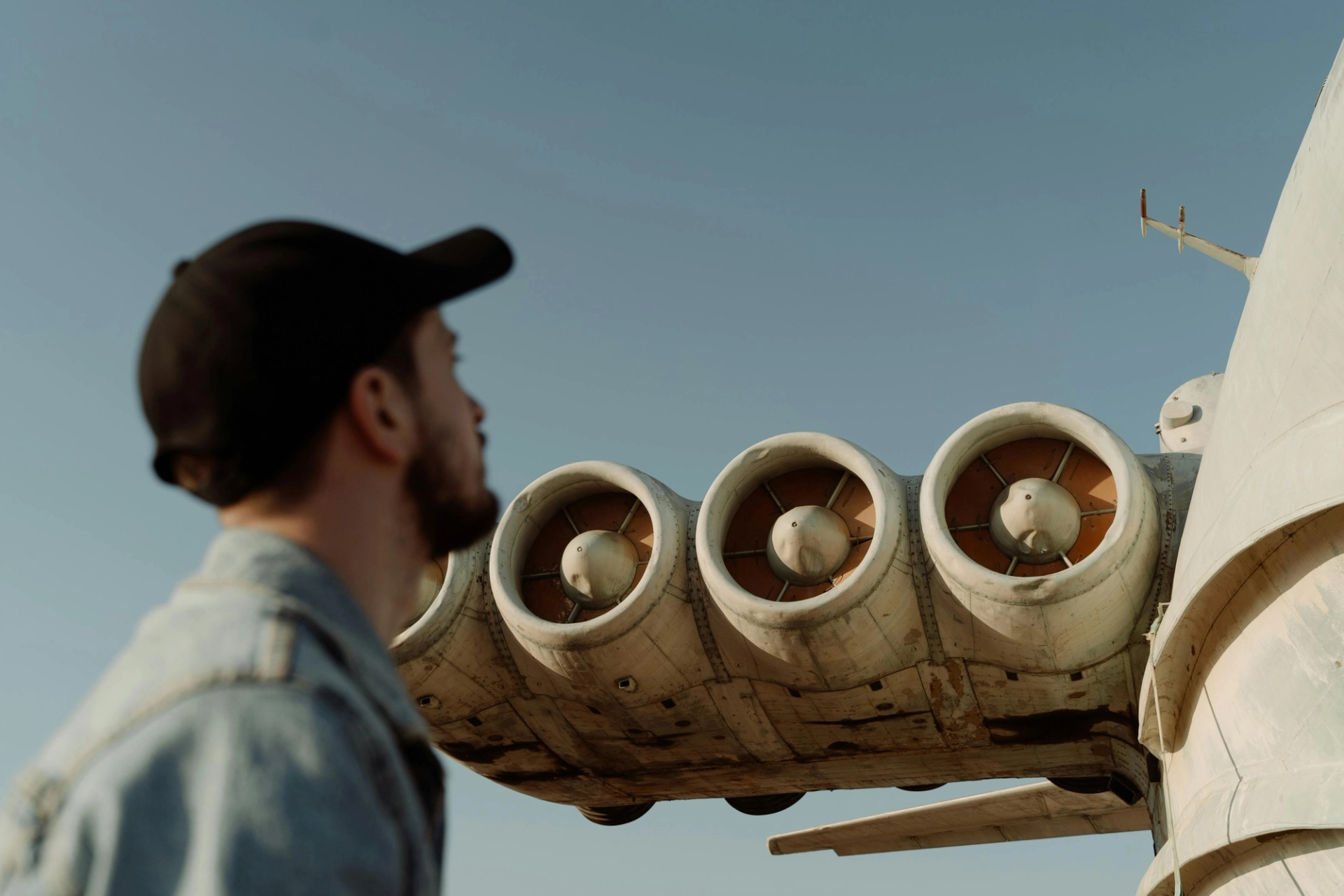
August 15, 2025
The Pros and Cons of Using Lean Manufacturing in Aviation
Lean manufacturing can improve efficiency and reduce costs in aviation—but it’s not always a clean fit. This breakdown explores what works, what doesn’t, and how leading aerospace companies are adapting lean to meet real-world complexity.
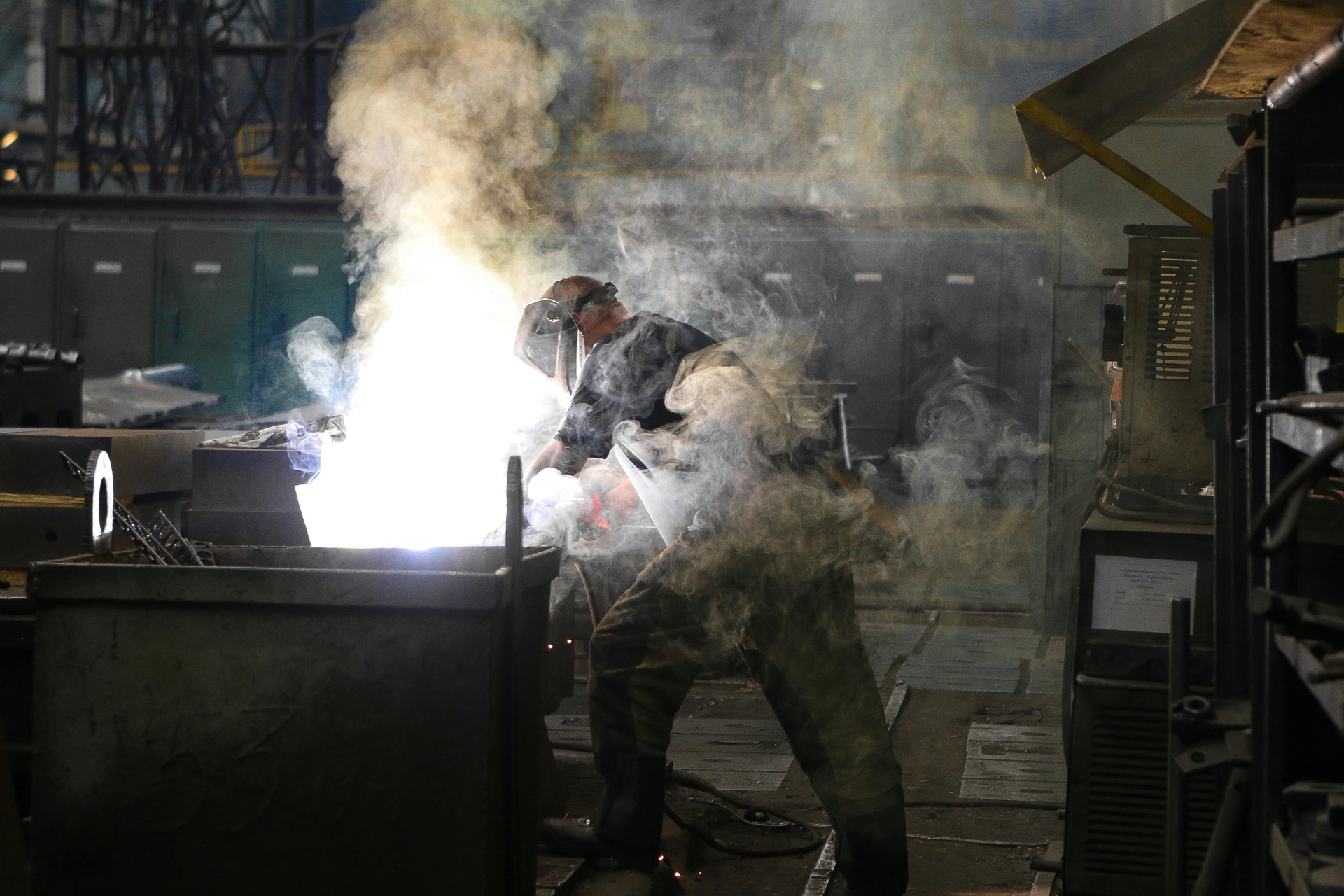
August 13, 2025
How Aviation OEMs Can Use Digital Twins to Optimize Manufacturing
Digital twins are transforming how aviation OEMs design, build, and maintain aircraft. Here’s how leaders like Airbus, Rolls-Royce, and Bell are using them to optimize manufacturing and operations.
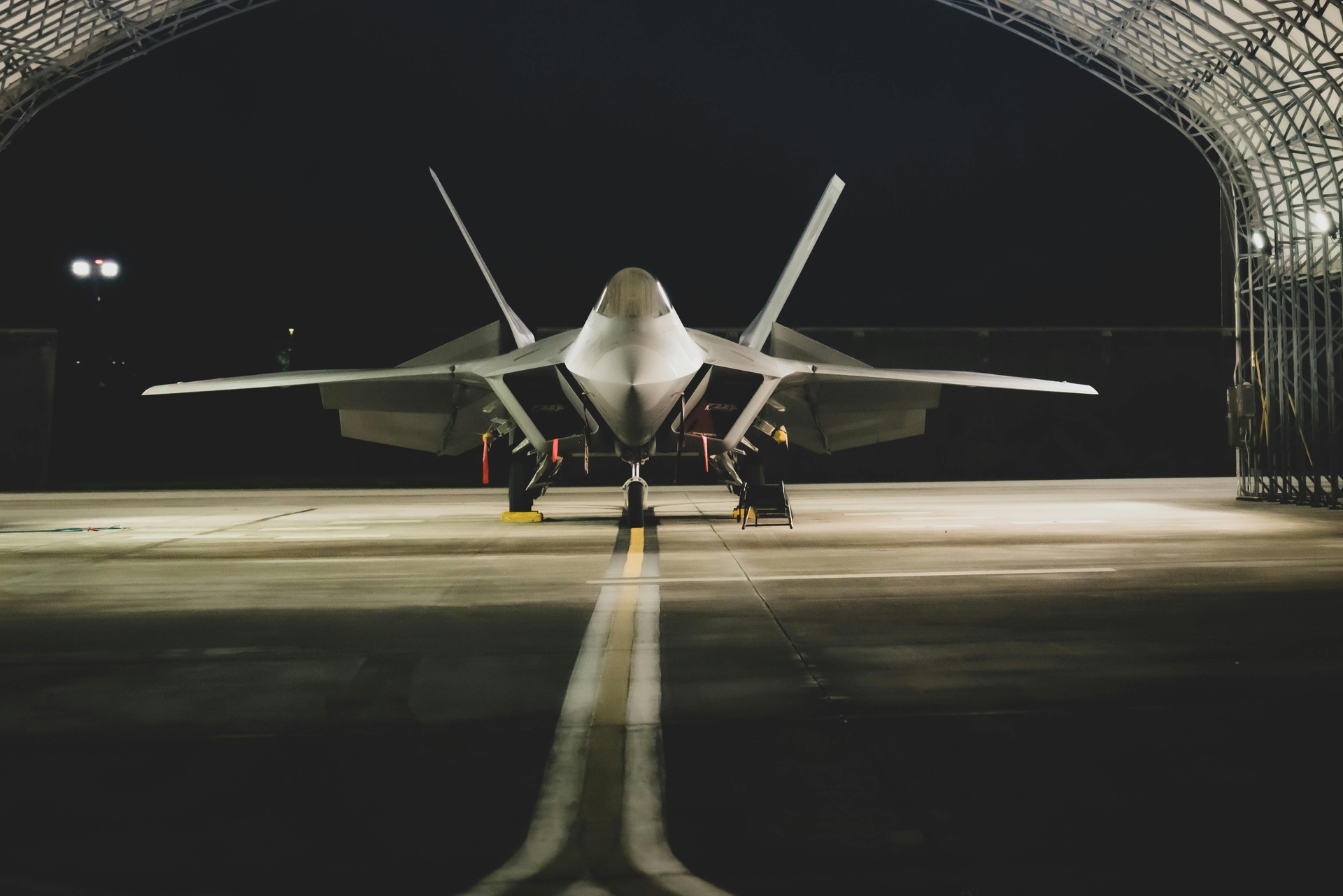
August 11, 2025
Integrating Blockchain for Traceability in Aviation Maintenance
Blockchain is bringing crystal-clear traceability to aviation maintenance. It’s helping companies create tamper-proof records, track parts with confidence, and cut down on errors. See how the industry is using it today, and where blockchain is headed next.
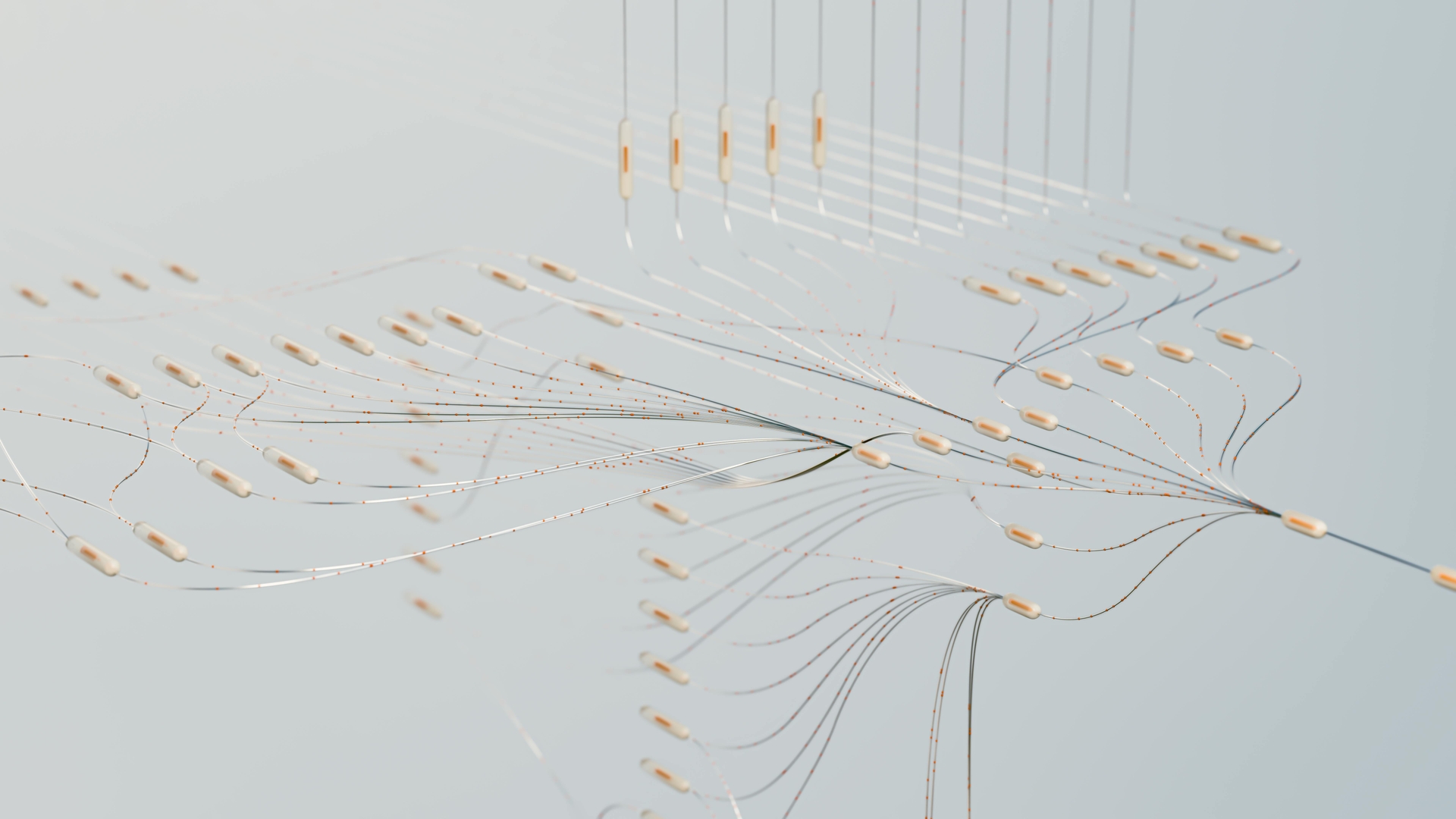