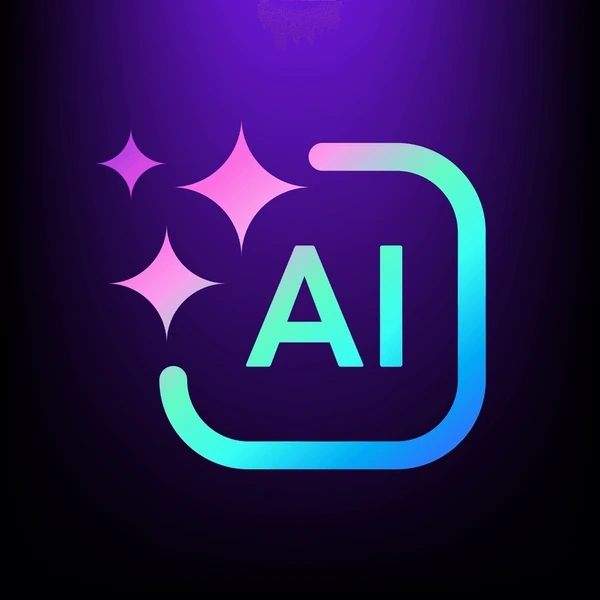
Smarter email, faster business.
Understanding the Shelf Life of Aircraft Parts to Create Your Next Replacement Schedule
July 15, 2025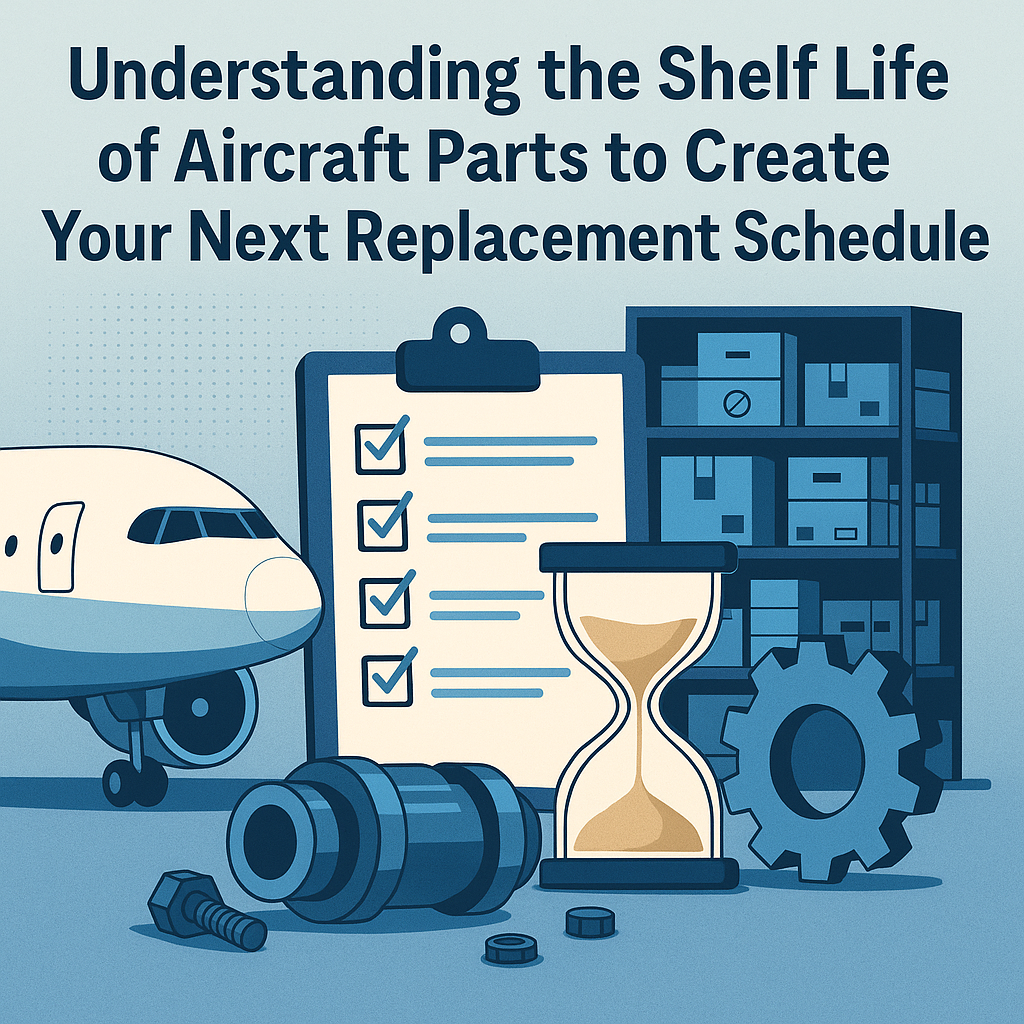
Aircraft parts don’t last forever. Learn how shelf life tracking and AI-drven planning can streamline airthworiness and compliance.
In aviation, every part has its own lifespan that must be meticulously managed against thousands of other parts. Coordination, in perfect synchronicity, is a must for flight safety.
Knowing when components expire, degrade, or go out of compliance is critical for safe operations and organized maintenance. Yet many airlines, MROs, and suppliers still rely on spreadsheets, manual tagging, or even sticky notes to track expiration dates.
Aviation shelf life requires far more meticulous planning. It directly influences replacement schedules, procurement costs, and aircraft availability. Done right, shelf life tracking can reduce waste and extend the useful life of expensive inventory. Done wrong, it can leave a multi-million-dollar aircraft sitting idle over a $200 expired seal.
In this guide, we’ll break down how aviation shelf life works, why it matters, and how next-gen tools are bringing further accuracy and automation.
What is shelf life in aviation parts management?
Shelf life refers to the maximum amount of time a part can remain in storage before it’s considered expired, even if it hasn’t been used. This time limit is so that the part will perform as intended once installed. For aviation parts, chemical stability, material degradation, or OEM testing protocols all impact their storage durability.
Examples of shelf-life-limited parts include:
- O-rings and rubber seals that dry out or harden after a fixed number of months
- Batteries with chemical aging concerns
- Fire extinguishers that require recharge or recertification
- Adhesives and lubricants that are sensitive to temperature swings
- Tires that can suffer from dry rot or sidewall cracking, even if unused
Shelf life must be tracked from the date of manufacture, cure, or certification, whichever the OEM specifies. Additionally, shelf life is distinct from flight or service life. An oxygen mask may have a 10-year shelf life, but in service, it must be replaced every five years.
Regulatory agencies like the FAA insist on rigorous adherence to these distinctions. Its Technical Center Report TC-15-33 outlines how shelf life affects material conformity and airworthiness approvals (FAA).
Why shelf life matters for safety, compliance, and cost
Expired parts are a headache on multiple fronts, notably bookkeeping, safety, and liability. Using an item past its shelf life could mean compromised performance (if not component failure) and FAA infractions.
It’s not just engines and avionic components that are under scrutiny.. Even “minor” items like an expired sealant can cause a malfunction mid-flight.
The FAA Advisory Circular AC 00-56C emphasizes the importance of maintaining traceability and quality system documentation, including expiration and cure dates, across all supply chain partners (FAA). If your organization uses expired or improperly documented parts, you risk violating airworthiness standards and nullifying your regulatory compliance standing.
There’s also a hidden cost dimension. According to Boeing’s Distribution Services brochure, poor shelf life tracking contributes to unnecessary scrapping of parts, duplicate orders, and excess inventory buildup (Boeing Distribution). One airline audit found that over 30% of their expired inventory could have been used if better rotation or inventory visibility had been in place.
Types of shelf life and how they’re tracked
Different parts have different shelf lives, thus different tracking methods are used depending on material sensitivity, storage requirements, and usage classification.
There are two main types:
- Hard time shelf life: A strict expiration date is applied regardless of the part’s condition. Once expired, the part must be discarded or recertified. Common for chemical products, adhesives, or oxygen generators.
- Conditional shelf life: The expiration depends on environmental exposure (like temperature or humidity) and often require periodic inspection. These parts may be extended if conditions remain favorable.
Each part typically includes a DOM (Date of Manufacture) or DOC (Date of Cure) from which shelf life is calculated. For example, nitrile O-rings may have a shelf life of 12 to 36 months from the cure date, depending on MIL-spec classifications (Defense Logistics Agency).
In well-managed operations, these dates are logged into an ERP or MRO system, flagged with automated alerts as expiration nears. But many smaller operations still rely on physical labels and handwritten ledgers, both of which increase the likelihood of human error and lost traceability.
Common aircraft parts with defined shelf lives
Some aircraft parts have strictly defined lifespans due to their chemical composition, environmental sensitivity, or degradation risk. These include:
- Rubber components such as O-rings, seals, and gaskets: Often affected by ozone exposure, temperature swings, and material fatigue. Shelf life typically ranges from 3 to 10 years, depending on storage conditions and compound type.
- Adhesives and sealants: Products like epoxy or polysulfide sealants may degrade chemically, even in sealed containers. Most have 6- to 12-month shelf lives from date of manufacture (FAA).
- Batteries: Both lead-acid and lithium-based aircraft batteries degrade over time regardless of use. Most OEMs define service or shelf life limits of batteries between 18 and 36 months.
- Emergency items: Survival gear, oxygen generators, and inflatable slides all have varying shelf life dates due to internal pressure systems and chemical age limits.
- Paints, lubricants, and fluids: These often include strict environmental tolerances and need to be rotated regularly. The Defense Logistics Agency (DLA) tracks thousands of consumables through automated expiration systems to support readiness (Defense Logistics Agency).
Understanding which categories pose the most risk allows supply teams to prioritize their monitoring and rotation practices accordingly.
How environmental conditions accelerate expiration
Even when a component isn’t technically “expired,” improper storage can still degrade its “useful” life.. Humidity, UV exposure, high temperatures, or failure to rotate stock can all accelerate material degradation. Some materials, like nitrite-based rubber, which requires dark, low-heat, low-humidity storage, are especially finicky (FAA).
Despite this, some facilities still store sensitive parts in uncontrolled environments. Without dehumidifiers or environmental monitoring, parts can silently expire well before their labeled dates, creating a false sense of security within inventories.
The need to monitor environmental exposure is one reason fleets are embracing modern ERP integrations. Platforms like ePlaneAI use sensors, IoT devices, and other controls for more precise monitoring, with real-time data continuously transmitted to enterprise resource planning systems.
Shelf life tracking challenges in MRO and supply chain
For MRO shops and airline maintenance departments, tracking shelf life is often an unnecessarily complex process. Many systems still rely on disconnected spreadsheets, handwritten labels, or siloed procurement platforms. These gaps often lead to overlooked expiration dates, duplicate purchases, or worse, installation of expired components.
A 2023 TRACE Aerospace survey found that nearly 40% of MRO providers admitted to having discovered expired inventory only during audits or aircraft checks (TRACE Aerospace). Beyond the safety and reputational risk, companies hemorrhage resources for wasted labor spent using ineffective tools managing unusable stocks, emergency repairs, and reorder and replacement costs.
What’s more, tracking gets harder when:
- Parts are transferred between locations
- OEMs relabel components or use inconsistent date formats
- Environmental logs are stored separately from part records
- Shelf life depends on variable exposure conditions, not just fixed dates
All of this highlights the need for automation, digitization, and integrated data sharing, a capability that many legacy systems lack.
How digital tools are improving shelf life management
Newer MRO and ERP platforms, especially those integrated with AI capabilities like ePlaneAI, can address shelf life complexity. These systems automatically calculate expiration dates from manufacture or cure data, flag at-risk parts, and integrate with supplier systems for real-time batch tracking.
For example, platforms like Boeing’s Distribution Services incorporate lot-based shelf life tagging and dynamic rotation rules for sensitive inventory (Boeing Distribution). Similarly, Tractian’s TracOS™ offers predictive inventory alerts using AI-driven trend data.
ePlaneAI’s own integration capabilities go further by aligning ERP and MRO data streams, enabling:
- Predictive shelf life forecasting based on environmental exposure
- Real-time alerts before expiry
- Streamlined supplier coordination for auto-replenishment
- Enhanced compliance reporting for FAA audits
Companies are increasingly combining procurement, storage, and usage data into one view, making shelf-life management a collaborative and proactive business function.
The regulatory landscape: FAA, DoD, and OEM shelf life standards
In the aviation sector, regulatory guidance around shelf life is strict but fragmented. The FAA, OEMs, and defense agencies each maintain their own expectations, and failing to comply can trigger grounding events, fines, or loss of certification.
The FAA requires that time-limited parts, such as O-rings, adhesives, batteries, and emergency equipment, be tracked by install date, by shelf life, and by service life limitations (FAA). Their Advisory Circular 00-56C also reinforces the need for traceability of parts with time limits and the need to verify conformance before release to service (FAA Advisory Circular).
Meanwhile, the Department of Defense maintains its own stringent requirements through the Shelf-Life Management Program, which uses Type I (non-extendable) and Type II (extendable) classifications to determine how military aviation parts are stored, inspected, and disposed of (Defense Logistics Agency).
For private sector compliance, this means:
- Understanding the classification and time limits defined by the OEM
- Using date of manufacture or cure date, not delivery date, to calculate expiration
- Maintaining environmental storage logs (temperature, humidity) that match the specs
- Documenting shelf-life extensions or inspections where allowed
Case study: RAF Mildenhall’s 24/7 parts store
At RAF Mildenhall, the 100th Logistics Readiness Squadron operates one of the few U.S. Air Force parts stores open 24/7. They help aircraft units like the CV-22 Osprey and KC-135 Stratotanker plug or prevent supply gaps and maintain mission readiness.
To manage shelf-sensitive materials, the squadron uses radio-frequency identification (RFID) systems, a centralized database, and real-time tracking to flag expiration risks and ensure items remain serviceable. Even toilet paper used on aircraft is tracked, highlighting the scope of logistics support needed (Defense Logistics Agency).
Their approach shows that when inventory housekeeping is taken seriously, businesses enjoy uninterrupted flight operations and a more proactive, well-coordinated supply chain.
Planning your replacement schedule with AI-enhanced predictive tools
Traditionally, replacement schedules were built on static charts, worst-case estimates, and a healthy dose of just-in-case overstocking. But with tougher global supply chain constraints, increased tariff uncertainty, and challenging environmental regulations, absolute demand precision is critical.
AI-powered tools like ePlaneAI integrate predictive maintenance into existing tech stacks. ePlaneAI pulls in historical usage, environmental, and exposure data, along with OEM guidelines to calculate the most cost-efficient replacement windows.
ePlaneAI’s machine learning models can identify which shelf-stable parts are degrading faster than expected based on humidity fluctuations or transportation handling, insights that would not surface in traditional recordkeeping. These AI models can also project downstream part failures from one single component nearing expiration, offering your maintenance planners ample time to act before reliability is compromised.
Additionally, MRO teams using ePlaneAI can automate alerts for parts approaching shelf life expiration, auto-generate replenishment requests, and sync with ERP systems to update availability in real-time.
Don't let shelf life be the weak link in your MRO chain
Shelf life mismanagement seems like a matter of warehouse paper-pushing, but in aviation, your storage shelves are at the center of cost management, compliance, safety, and all MRO workflows.
Whether you're tracking moisture-sensitive adhesives or inflatable life rafts, failure to adhere causes bottlenecks, and erodes trust.
When aviation teams understand regulatory frameworks and the direction the industry is headed, adopting
AI tools like ePlaneAI bring added clarity and resilience to aviation teams seeking a constant pulse on regulatory framework and where the industry is headed. Shelf life management is the crux of successful operations, and trending inventory figures are often a bellwether for what’s to come next.
>>> Don’t let expired parts catch you off guard. Use ePlaneAI to track, optimize, and automate your aircraft part replacement schedule. Book a demo today!
Aviation Maintenance Trends That May Gain Momentum in Uncertain Circumstances
Aircraft are staying in service longer, supply chains are a powder keg, and the tech is evolving overnight. Discover the maintenance trends gaining momentum and what they mean for operators trying to stay airborne and profitable.
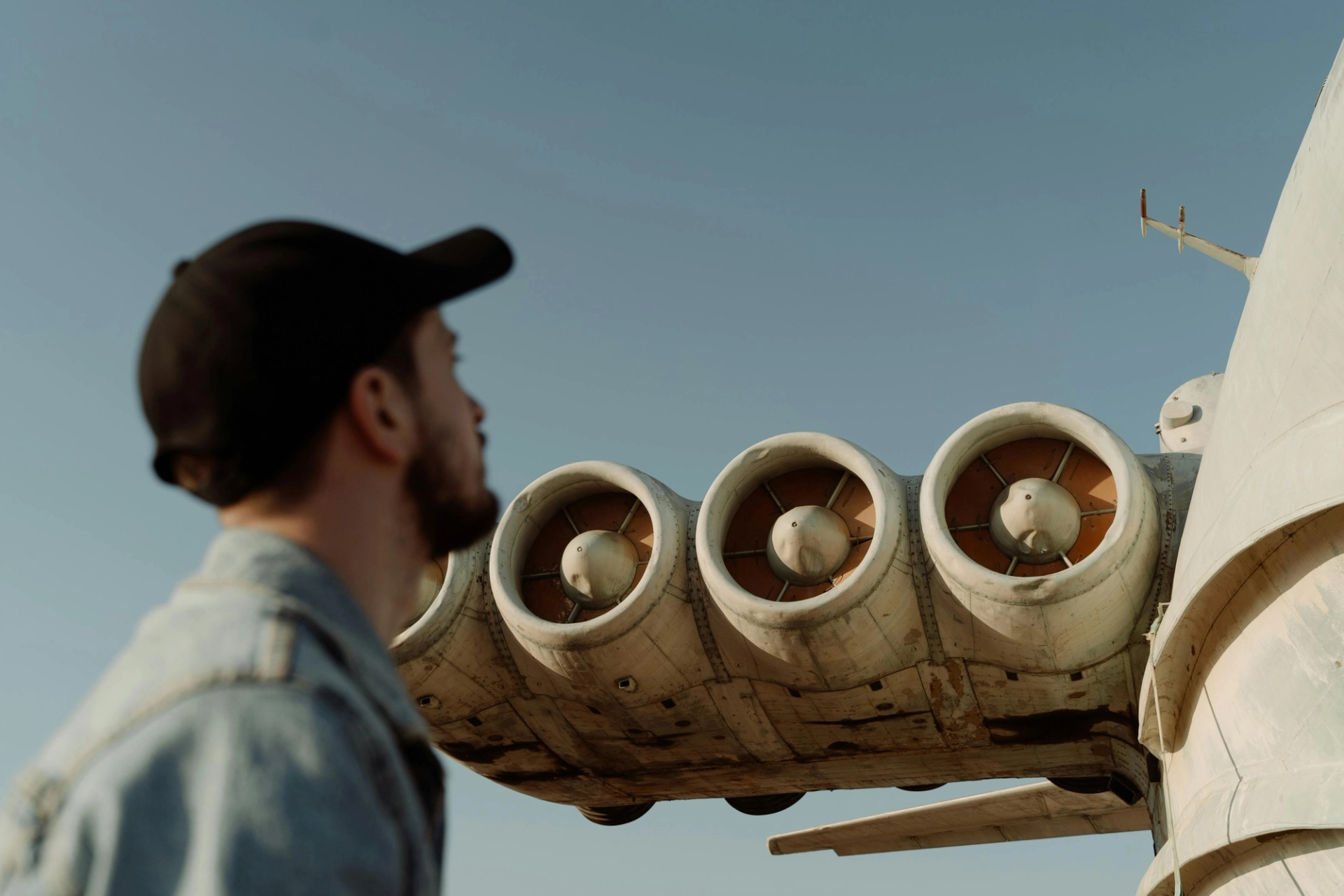
August 27, 2025
How to Use AeroGenie to Streamline Procurement Reporting in Aviation
What makes AI tools understand human language? It’s not magic—it’s NLP. Learn how NLP works, where it's going, and how it's changing the way we query and build reports with AI.
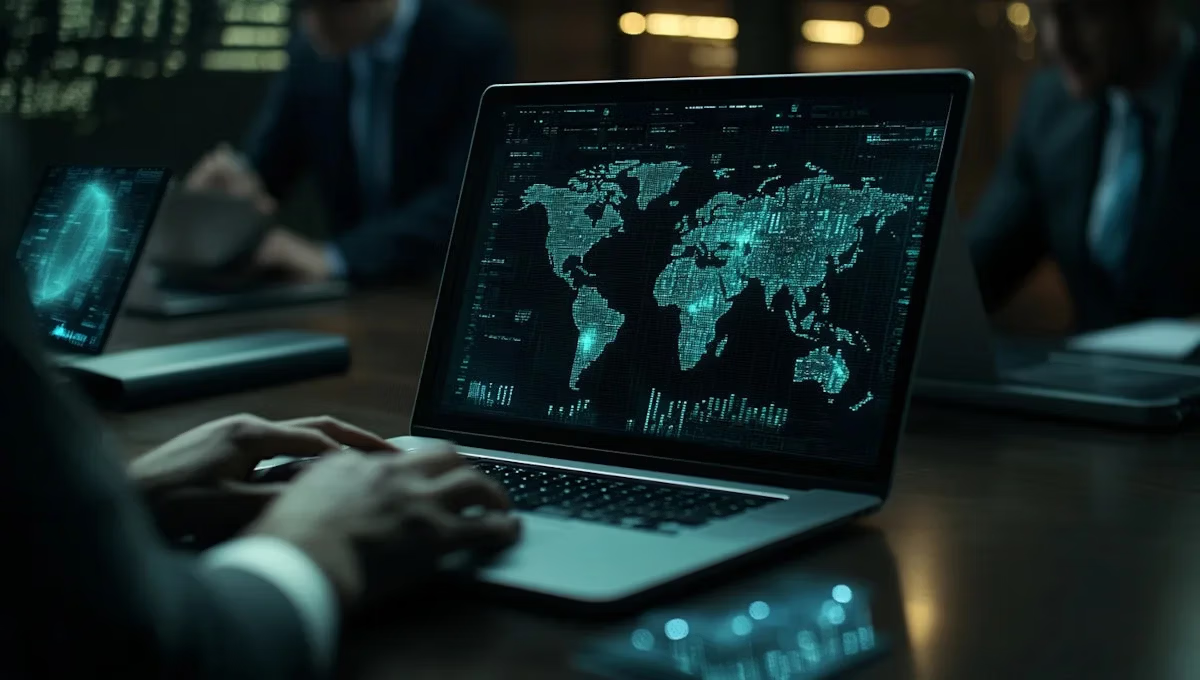
August 25, 2025
What Is Parts Manufacturer Approval (PMA) and Why Is It Important in Aviation?
PMA parts are transforming aviation—cutting costs, improving performance, and reducing downtime. Learn why FAA-approved PMA components are becoming a go-to choice for airlines, MROs, and OEMs alike.
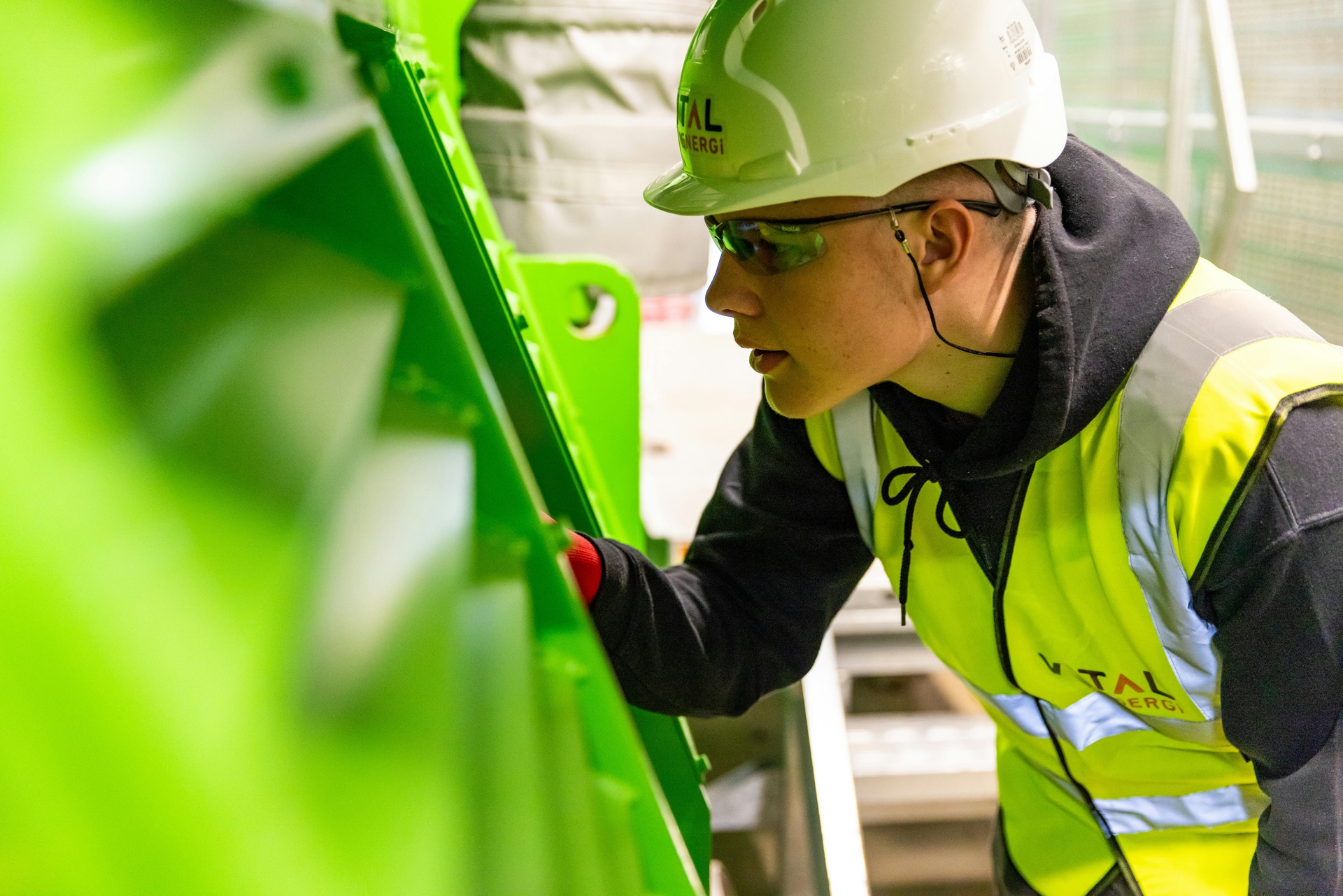
August 22, 2025
How to Manage Your Aircraft Maintenance Team With Schedule AI
Tired of manual maintenance scheduling headaches? Meet Schedule AI. See how Schedule AI is transforming aircraft operations, helping your team optimize tasks and drastically cut down turnaround times. Keep your fleet in the air and on schedule.
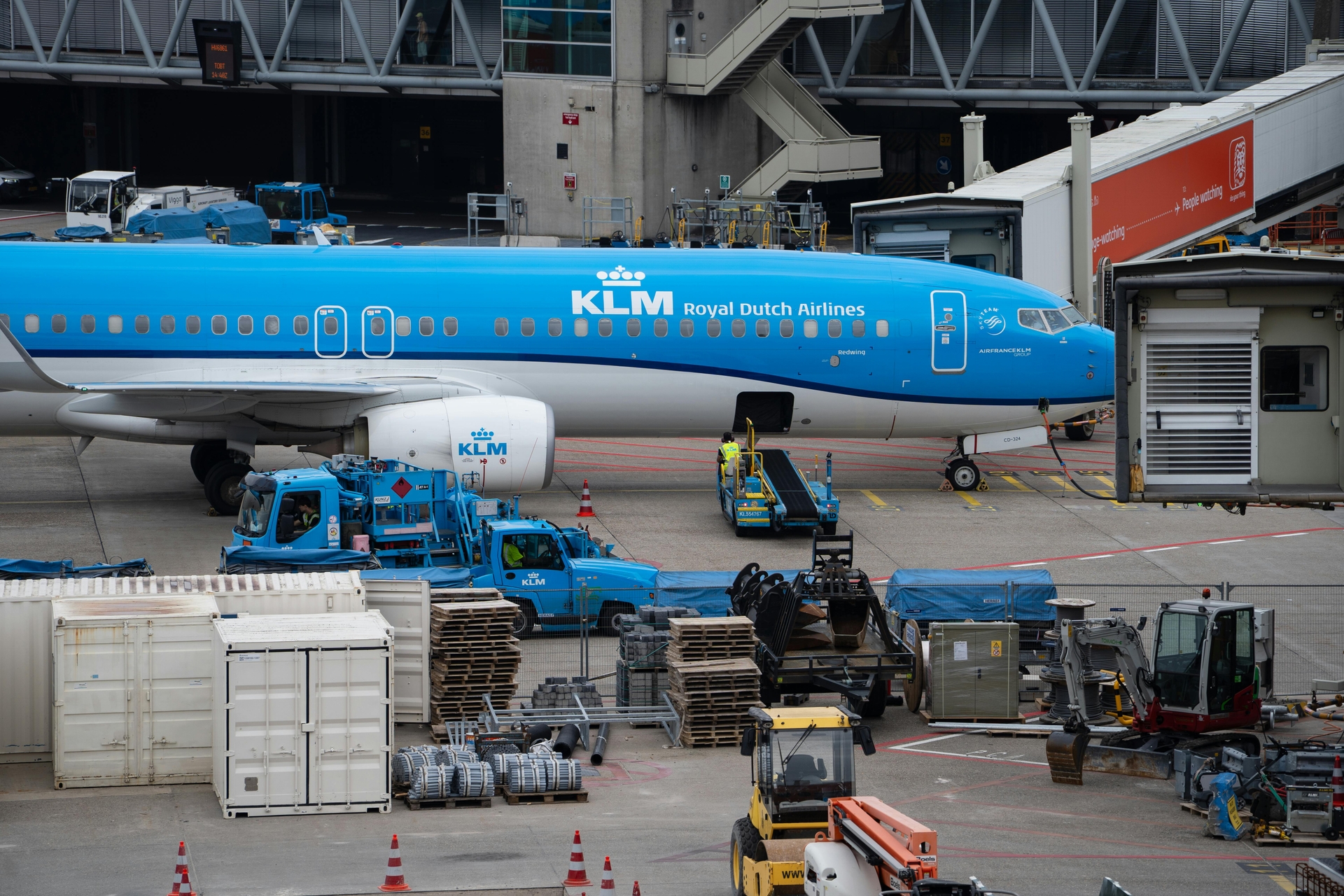