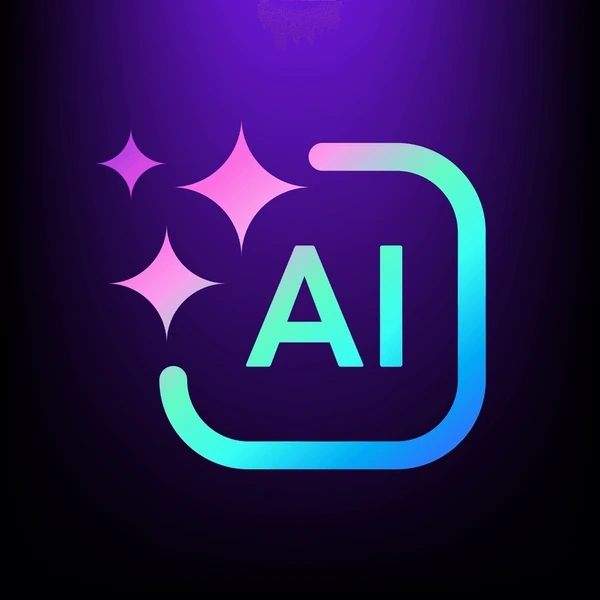
Smarter email, faster business.
How to Improve Spare Parts Forecasting with Predictive Models
January 08, 2025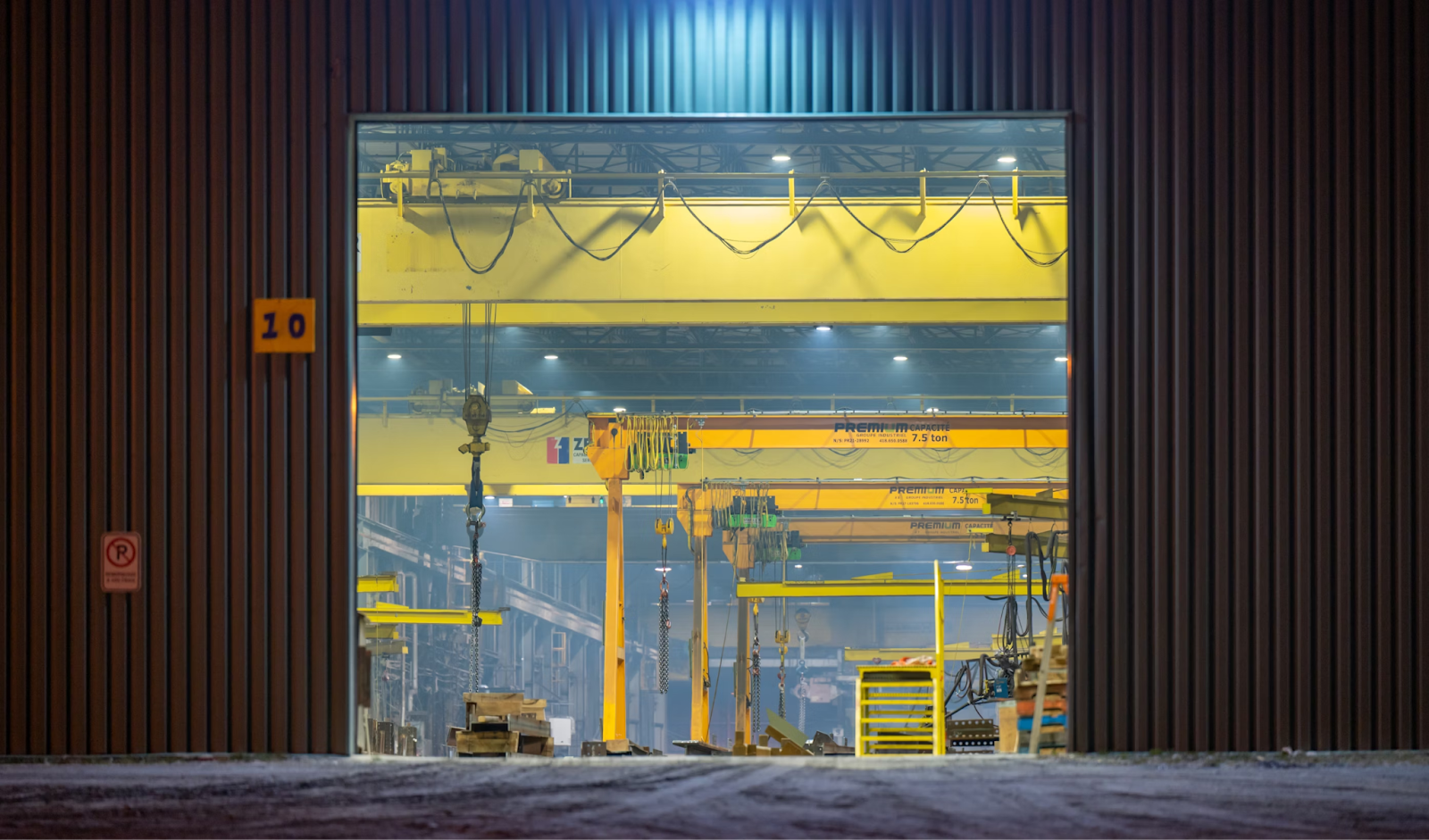
Spare parts forecasting just got smarter. ePlaneAI’s predictive models help aviation businesses reduce downtime, slash costs, and keep fleets in the air.
In aviation, precision isn’t just a luxury—it’s a necessity. Spare parts management plays a critical role in keeping fleets operational, avoiding costly delays, and maintaining customer trust. However, many aviation companies struggle with forecasting spare parts demand accurately, and it costs them on both ends with high holding costs for excess stock, or AOG incidents when the holding is insufficient. Both outcomes are avoidable.
Traditional methods rely on error-prone manual processes, like data entry in spreadsheets—or reactive approaches, reacting to shortages instead of more proactive demand forecasting methods to prevent them. These leave gaps in your parts management, resulting in stockouts or overstocking. Either scenario can be financially crippling.
Predictive models offer a truly game-changing solution. Aviation companies can forecast demand with unparalleled accuracy using advanced inventory analytics and quantitative demand forecasting models.
In this article, we explore the shortcomings of traditional forecasting methods and the advantages of a predictive modeling approach. We'll also explore how ePlaneAI’s inventory automation platform accurately forecasts demand for a leaner, more efficient supply chain.
Traditional forecasting and why it falls short
Using data and market research for data forecasting is not a new science. People have long used measurable data points to predict future outcomes and events, but the methods to do so have evolved over time for more consistent input variables and more accurate forecasts.
Spreadsheets and siloed data sources were once seen as cutting-edge tools, streamlining processes that had been painstakingly manual since the mid-20th century. But the velocity of modern aviation operations has left these traditional methods in the dust.
Today’s pace of technological advancements and the rapid flow of information demand systems that can interface seamlessly with real-time data. While some work tasks have transitioned to computer-based systems, a persistent reliance on outdated, manual processes creates bottlenecks. These inefficiencies are magnified in an environment where automated systems process vast quantities of data in seconds, while manual methods struggle to keep up.
This has rendered traditional approaches to spare parts forecasting obsolete. The need for integration, speed, and accuracy has never been greater, and clinging to decades-old methods risks leaving operations vulnerable to errors, delays, and mounting inefficiencies.
Manual processes lead to inefficiencies
Traditional forecasting methods often rely on past sales data in spreadsheets or generic ERP tools, both of which are prone to human error and lack real-time insights. Maintenance teams must estimate demand based on past trends with a limited ability to factor in critical dynamic variables like component wear, flight conditions, or customer demand.
Forecasting is incomplete without key metrics
For spare parts demand forecasting, your projections are only as good as the data you have—and traditional methods leave significant gaps. Manual data entry introduces inaccuracies, but the real issue is the sheer number of variables you can’t manually account for:
- Do you know how much inventory is in every warehouse?
- Can you predict which region will need parts next?
- How long will it take to move components where they’re required?
Accurate forecasting today requires more than static data and periodic updates. The frequency of stock checks and demand assessments needs to match the velocity of modern aviation activity.
Reactive forecasting is too late
With traditional forecasting methods, aviation companies can only react to data. When issues arise, such as when a key part is unavailable or overstocked components incur high storage costs, companies scramble to find a quick remedy. This reactive approach often results in grounded aircraft and operational disruptions, with Aircraft on Ground (AOG) events costing airlines $10,000 per hour just for starters (AAA Air Support).
Lack of integration with other real-time data
Traditional systems struggle to keep pace in an aviation world where many processes are now digitized. While other areas benefit from automation and real-time computing, legacy manual processes remain a critical bottleneck.
This lack of integration with current performance data makes inventory management inefficient and reactive. Furthermore, these legacy systems often limit how much historical data can be analyzed, leaving separate BI and data teams to piece together insights. This delays access to actionable information—creating an even sharper contrast with the speed of surrounding digitized processes.
Predictive models for accurate inventory forecasting
Predictive modeling addresses the gaps left by traditional methods by analyzing and training data sets on a vast scale, including historical usage trends, operational conditions, component lifecycles, and other patterns. Here’s how they work:
- Analyzing inventory trends and movement: Predictive algorithms assess historical usage data, stock movement between locations, and replenishment patterns to identify trends and forecast future demand. For example, if parts are frequently moved between hubs to cover shortages, the model can recommend optimal stock levels for each location to reduce transit delays and costs.
- Incorporating regional and operational variables: Factors like maintenance schedules, regional demand patterns, and operational conditions are included to forecast inventory needs. For instance, a high-demand region during peak travel months might require more frequent stock replenishment compared to lower-traffic areas.
- Balancing stock levels across locations: Predictive models analyze inventory discrepancies and usage rates across multiple warehouses to suggest redistribution or procurement strategies. This approach minimizes stockouts in critical areas while preventing excess inventory in low-demand locations, optimizing overall inventory efficiency.
Key benefits of predictive forecasting
1. Avoiding stockouts
Stockouts can disrupt maintenance schedules and ground aircraft, leading to massive financial losses. Predictive models enable aviation companies to plan ahead, ensuring critical components are always available when needed.
2. Reducing excess inventory
Overstocking parts not only ties up capital but also incurs storage and depreciation costs. Predictive models balance inventory levels by aligning stock quantities with actual demand forecasts. Aviation companies using these tools have reported significant reductions in carrying costs.
3. Optimizing maintenance schedules
Predictive forecasting allows maintenance teams to align spare parts availability with scheduled maintenance windows. This coordination minimizes downtime and maximizes fleet availability and overall operational efficiency.
4. Improving financial planning
Predictive models free up working capital and reduce unnecessary expenditures when they align inventory with real demand. This optimization supports long-term financial stability, particularly important for carriers operating on thin margins.
5. Increasing cash flow and inventory turns
Efficient spare parts forecasting ensures inventory levels align closely with demand, preventing capital from being tied up in excess stock. This approach improves cash flow, allowing resources to be allocated where they’re most needed. Additionally, better inventory turnover reduces the risk of obsolescence, minimizing waste and maximizing operational efficiency.
ePlaneAI’s predictive approach to spare parts management
ePlaneAI combines advanced predictive analytics with aviation-specific knowledge for exceptional inventory forecasting. Here’s what the platform offers:
Turning vast data sets into actionable insights
ePlaneAI can help you see the forest in the trees—or rather, the trend patterns in a deluge of historical data. The platform processes historical data, examining fleet usage, environmental factors, and other variables to accurately predict demand.
Real-time inventory monitoring
The system integrates AI with ERP and inventory management systems to provide real-time updates on stock levels and part lifecycles. Predictive alerts notify teams when pre-set thresholds are reached or when a part is nearing the end of its usable life. Which could trigger automated procurement following business rules.
Customizable to fleet requirements
ePlaneAI’s Aviation AI platform is designed to adapt to the unique demands of aviation fleets. Whether managing inventory for a regional airline, a global carrier operation, or an MRO with multiple locations, the system aligns with industry-specific operational needs.
For any scenario, ePlaneAI can automatically reorder or adjust existing orders based on forecasted demand. This means plenty of lead time to get needed spare parts or cancel excess orders.
Spare parts forecasting in action
Here are some real-world examples of how supply forecasting enhances operational efficiency:
- Up to 30% reduction in AOG events. Through proactive MRO maintenance, an industry study reports that airlines can spot potential maintenance issues, including spare parts needs, early on to minimize grounded flights.
- Improved collaboration with fleets and OEM manufacturers. Open data flow enables real-time sharing of inventory levels, lead times, and maintenance schedules between airlines and OEMs. This transparency helps prevent delays in spare parts delivery and improves overall supply chain coordination.
- Faster response times to unplanned maintenance. Predictive data analytics enable airlines to anticipate parts shortages before they occur, ensuring spare parts are available in critical situations. This minimizes repair times and keeps operations running smoothly.
- Better cost control and waste reduction. Forecasting tools flag slow-moving or obsolete parts, allowing companies to reallocate inventory or negotiate with suppliers for more precise stock levels. This reduces carrying costs and waste associated with overstocking.
How predictive models work for parts forecasting
Data integration
Predictive models, powered by advanced techniques like neural networks, pull data from a wide range of sources, including historical usage trends, real-time inventory levels, supplier performance metrics, and operational variables such as flight schedules or seasonal demand.
These models don’t just focus on high-tech scenarios like sensor data but also handle bread-and-butter inventory tasks.
Example: The system might analyze daily stock movement across multiple warehouses to identify discrepancies and suggest real-time adjustments to avoid overstocking in one location while preventing shortages in another.
Pattern recognition
These algorithms excel at spotting correlations and trends that aren’t obvious through manual processes. Predictive analytics can identify patterns in stock usage, supplier reliability, or even fluctuations in demand caused by external factors like weather or geopolitical events.
Example: If a particular supplier consistently delivers late, the model can flag the issue and recommend adjusting order lead times to maintain buffer stock.
Proactive planning
Predictive models use simulations to plan for routine scenarios and potential disruptions. They not only forecast demand surges or stock depletions but also guide teams on optimal reorder points and procurement schedules to ensure seamless operations.
Example: During peak travel months, the system might recommend pre-ordering frequently used consumables, such as seat covers or light bulbs, while also optimizing replenishment cycles for high-demand regions.
Fine-tuning your predictive model
Accurate predictions begin with clean, comprehensive data. ePlaneAI’s platform continuously integrates real-time updates from IoT sensors, ERP systems, and supplier networks to minimize blind spots. Users can adjust variables, such as lead times or priority levels for AOG parts, to ensure the model reflects operational realities.
- Prioritize critical variablesNot all data points hold equal weight. The system is designed to emphasize high-impact variables like AOG priority parts while de-emphasizing less critical components, ensuring the forecasts focus on what matters most for fleet readiness.
- Feedback-driven improvementWhile ePlaneAI’s predictive models are highly advanced, occasional adjustments are necessary. When real-world feedback identifies discrepancies—such as a miscalculated demand for a specific part—ePlaneAI’s team collaborates with users to refine the model. This process incorporates new data points and factors to improve accuracy and adaptability over time.
- Adapt to operational changesAviation operations are dynamic, and the ePlaneAI platform evolves alongside them. Whether fleets expand, routes change, or environmental conditions shift, the platform adjusts to ensure inventory forecasting remains precise and actionable.
AI and predictive modeling can redefine inventory forecasting
Predictive inventory forecasting is a must for aviation businesses aiming to optimize operations and maintain their business resiliency in a challenging industry. With platforms like ePlaneAI, you can anticipate demand, streamline inventory, and reduce costly downtime.
By using advanced algorithms and real-time data, aviation companies can transform spare parts management from a reactive burden into a proactive advantage for smarter decisions, leaner operations, and a fleet that’s always ready to fly.
Ready to eliminate guesswork and keep your fleet operational? Discover how InventoryAI can optimize your spare parts management and streamline your operations. Book a meeting with ePlaneAI today.
Aviation Maintenance Trends That May Gain Momentum in Uncertain Circumstances
Aircraft are staying in service longer, supply chains are a powder keg, and the tech is evolving overnight. Discover the maintenance trends gaining momentum and what they mean for operators trying to stay airborne and profitable.
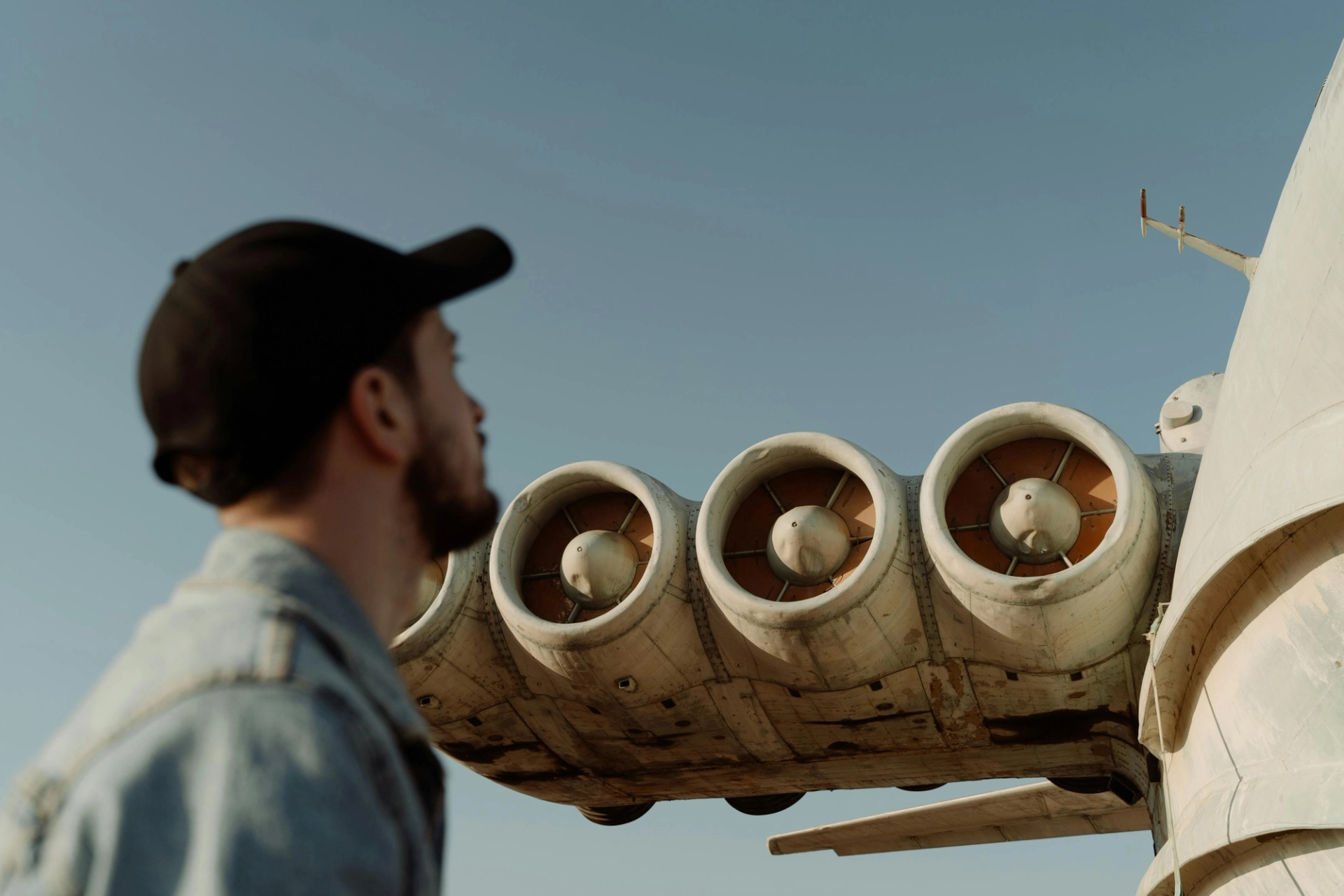
September 4, 2025
How ePlaneAI Can Help You Create an Aviation Sales Accountability Plan
Aviation sales need accountability more than ever. See how ePlaneAI helps airlines, MROs, and suppliers create data-driven sales accountability plans that boost performance, align incentives, and drive measurable growth.
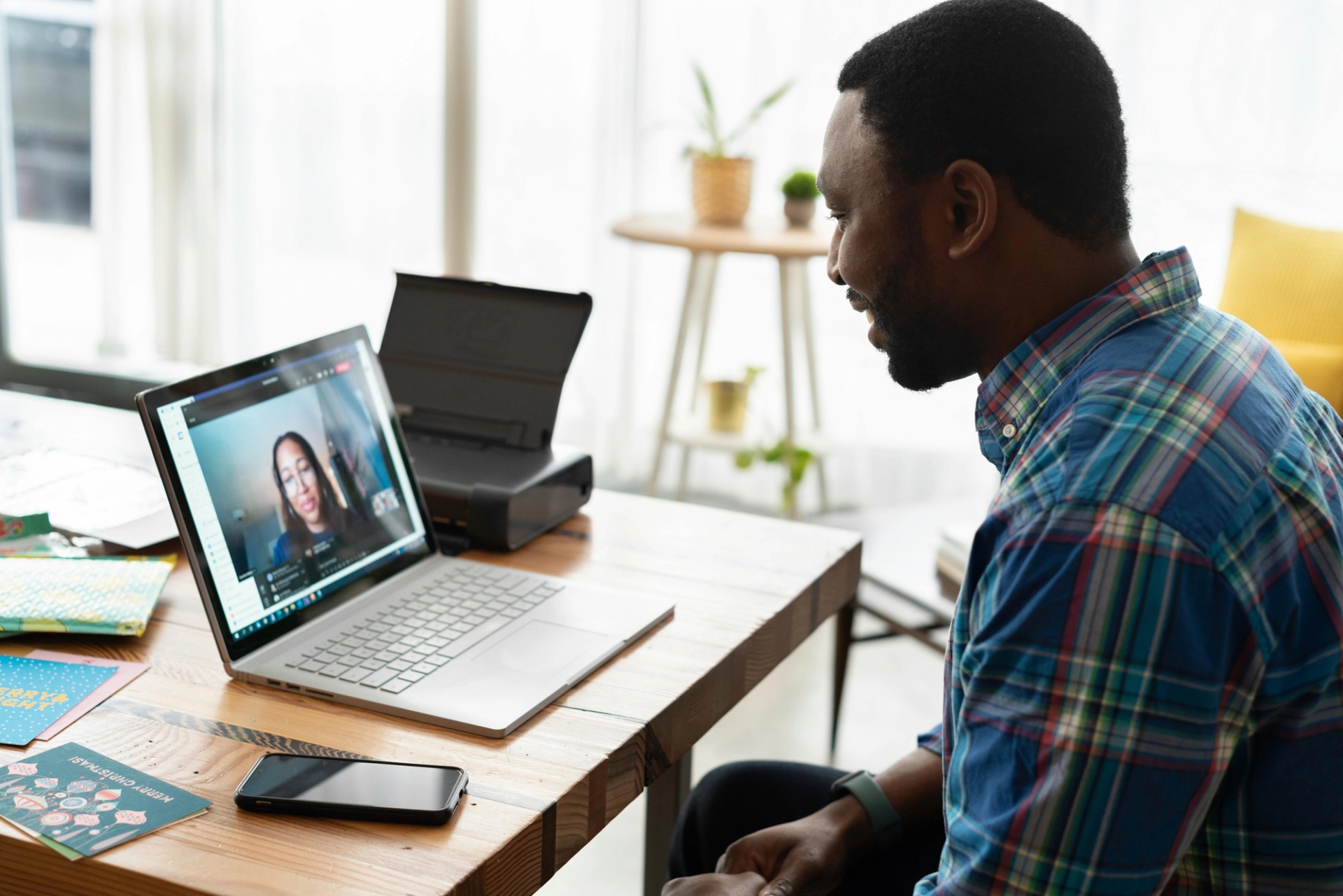
September 1, 2025
Aircraft Part Shipping Strategies That Work for Your Business
From urgent AOG shipments to oversized engine freight, better aircraft part shipping strategy matters. Learn the most effective ways to move high-value aviation parts safely, quickly, and cost-efficiently.
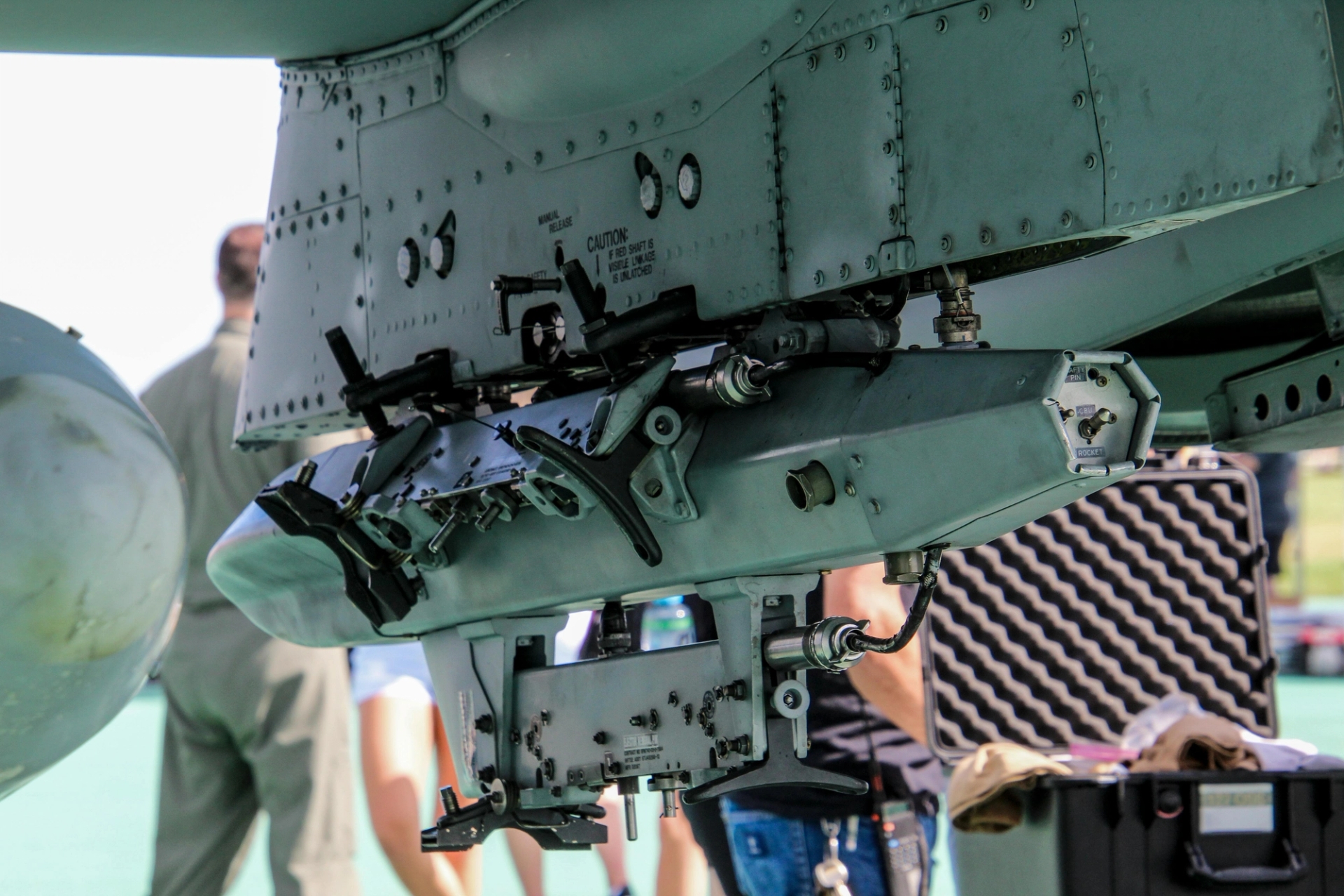
August 27, 2025
How to Use AeroGenie to Streamline Procurement Reporting in Aviation
What makes AI tools understand human language? It’s not magic—it’s NLP. Learn how NLP works, where it's going, and how it's changing the way we query and build reports with AI.
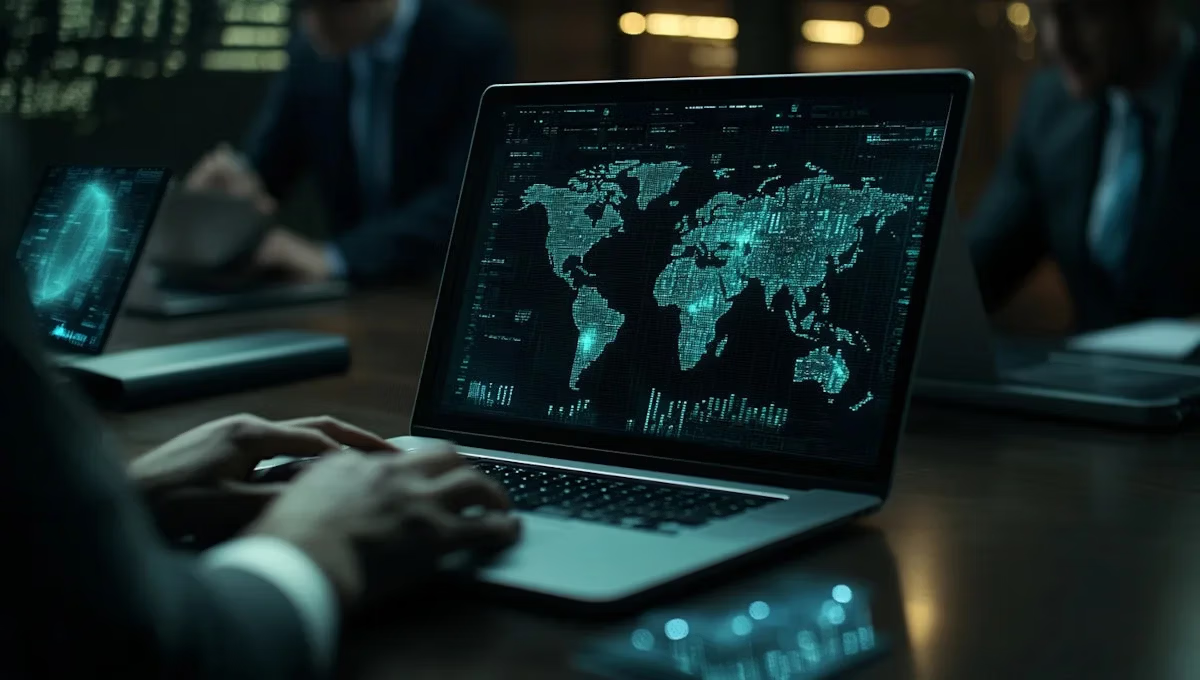