Preventing Inventory Shrinkage in the Aviation Industry
三月 27, 2025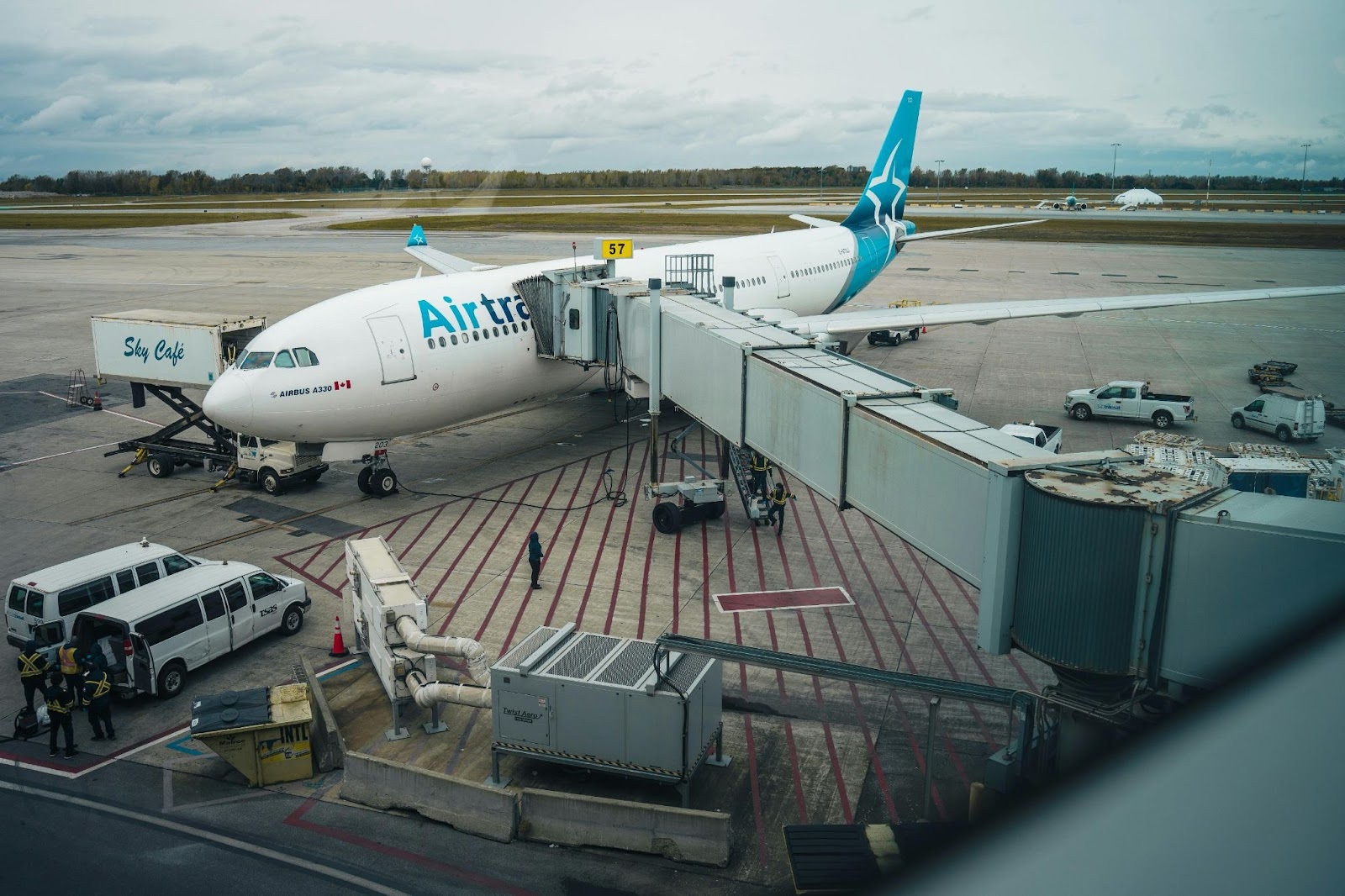
航空库存丢失的原因和方式远比你想象的更令人意外。从内部欺诈到飞机部件被盗,探索盗窃背后的原因,以及人工智能、RFID、区块链和其他技术如何阻止盗窃。
库存收缩是指由于盗窃、欺诈或运营效率低下而导致的飞机零件、工具和材料的损失,对航空业来说是一个持续的财务和航空安全风险。
无论是发动机缺失、未经授权的部件拆卸还是供应链管理不善,损耗都会导致飞机停飞、运营中断和法律纠纷。
最近一些备受瞩目的案件凸显了问题的严重性。香料航空被指控未经许可拆除租赁飞机的发动机,而捷特中西部航空则指控澳大利亚雷克斯航空在未全额付款的情况下拆除并报废了其飞机。内部威胁也发挥了重要作用,由于财务脆弱性,航空业员工参与了走私、盗窃和欺诈等活动。
与航空公司和维护、修理和大修面对不断上升的成本和精简运营的压力,应对库存损耗比以往任何时候都更加重要。本文探讨了航空企业减少损失和加强问责制的成因、财务影响以及最佳预防策略。
Whether it’s missing engines, unauthorized part removals, or supply chain mismanagement, shrinkage leads to grounded aircraft, disrupted operations, and legal battles.
什么原因导致航空库存缩水?
盗窃和未经授权的部件拆卸
航空资产价值极高,使其成为库存盗窃的首要目标。近期最引人注目的案件之一涉及香料航空(SpiceJet),该公司涉嫌未经Spectre Air Capital批准,从租赁的B737-700(BDSF)货机上拆卸发动机。出租人的法律团队将此行为定性为“表面盗窃”,指控该航空公司无偿使用了这些发动机(CH-Aviation,2025年1月)。
同样,Jet Midwest 也对 Rex Airlines 提起诉讼,声称该航空公司在未能完成 200 万美元的购买协议后,拆解了四架飞机的零件,并报废了剩余的机身(CH-Aviation,2024年9月)。
这些事件凸显了租赁商和维护、修理和大修公司在与陷入财务困境的航空公司打交道时面临的风险,而且盗窃不仅限于发动机等主要部件。
根据 鱼鹰飞行解决方案机场和航空公司员工利用内部权限走私黄金、毒品和其他贵重物品的行为屡屡被抓。维护、修理和大修(MRO)设施、货运站和飞机存放地点的安全漏洞使不法分子更容易利用航空资产。
内部威胁和员工剥削
内部人员参与航空业萎缩并非新鲜事,但疫情后的经济困境加剧了这一问题。英国国家犯罪局2021年的一份报告警告称,由于财务困境,机场和航空公司的员工——尤其是那些从事安全敏感岗位的员工——正成为有组织犯罪网络的目标。Osprey Flight Solutions,2023年1月)。
除了库存盗窃之外,常见的诈骗手段还包括:
- 行李搬运工和货物工人交换行李标签以绕过海关。
- 航空公司维修人员将毒品和违禁品藏匿于飞机电子设备舱内。
- 地勤人员和清洁工走私贵重物品,例如餐饮车里藏着黄金。
航空业对第三方服务提供商和承包商的依赖进一步使监管复杂化,使内部监控变得既具有挑战性,又对于降低收缩风险至关重要。
Whether it’s missing engines, unauthorized part removals, or supply chain mismanagement, shrinkage leads to grounded aircraft, disrupted operations, and legal battles.
库存缩减的财务影响
直接经济损失
库存缩水每年给航空业造成数百万美元的损失,但其全部财务影响不仅限于零件被盗或丢失的直接损失。
例如,Jet Midwest 向 Rex Airlines 索赔 720 万美元,指控该航空公司在没有全额付款的情况下拆除并报废了飞机(CH-Aviation,2024年9月)。
除了这些诉讼之外,萎缩还会导致:
- 飞机停飞造成的收入损失:当发动机、起落架或航空电子设备等关键部件消失时,飞机将无法使用,从而扰乱运营。
- 更高的保险费:因盗窃或零件丢失而频繁提出的索赔可能会推高航空盗窃风险保险的成本。
- 罚款和法律费用:违反租约和资产丢失纠纷通常会导致数百万美元的和解。
运营中断和供应链问题
库存缩减不仅会损害资产负债表,还会对国际航空运营造成严重影响。
一 麦肯锡2024年6月报告强调,消费包装商品和塑料及纸质包装公司的库存水平仍比新冠疫情之前的平均水平高出 15-20%,而零售商则大幅削减库存水平以将损失降至最低。
航空业面临着类似的平衡行为,因为库存过剩会导致浪费,但由于收缩而导致的短缺会导致延误和供应链瓶颈。
运营后果包括:
- 航班取消和延误:缺少零件会导致飞机被归类为 AOG(飞机停场)事件,从而造成代价高昂的中断。
- 更长的维护周转时间:如果关键部件消失,维护团队必须寻找替代品,从而增加停机时间。
- 供应链效率低下:航空公司必须持有超过所需数量的库存来规避盗窃和欺诈风险,从而占用了可以更好地配置到其他地方的资金。
鉴于这些风险,航空公司、MRO 和租赁商必须采取主动措施跟踪库存并加强航空安全协议。
Whether it’s missing engines, unauthorized part removals, or supply chain mismanagement, shrinkage leads to grounded aircraft, disrupted operations, and legal battles.
防止库存缩水的策略
实施先进的跟踪和安全措施
为了防止未经授权移除高价值部件,航空公司可以利用技术驱动的解决方案 例如:
- 飞机部件的 RFID 和 GPS 跟踪:这些系统能够实时监控发动机、航空电子设备和其他关键库存。
- 基于区块链的资产追踪:提供组件所有权和转移的不可变记录,降低欺诈风险。
- 维护设施和存储站点的人工智能监控:帮助识别异常员工行为,例如未经授权进入限制区域。
许多行业已经从这些技术中受益,航空业也必须效仿,以降低萎缩风险。
加强内部控制和审计
定期审计和库存核对可以显著减少损耗。公司应该:
- 进行突击检查在维修站点和仓库。
- 限制接触高价值零件具有多层次的删除授权。
- 需要双重验证用于零件转移和移除,以防止内部欺诈。
航空公司还应确保租赁协议包含明确的资产保护条款,以防止出现类似 Jet Midwest 和 SpiceJet 案件中的纠纷。
Whether it’s missing engines, unauthorized part removals, or supply chain mismanagement, shrinkage leads to grounded aircraft, disrupted operations, and legal battles.
协作和行业标准
加强产业合作应对萎缩
航空业必须采取协作方式来减少库存损耗,尤其是在涉及内部威胁和有组织犯罪的情况下。Osprey 飞行解决方案报告强调了经济困难的航空业员工如何成为犯罪网络走私毒品、武器和贵重飞机部件的目标。
在经济低迷时期,这个问题更加严重,因此员工筛选和安全培训至关重要。
为了应对这些风险,航空利益相关者应该:
- 分享盗窃模式情报涉及航空公司、MRO 和执法机构。
- 标准化报告程序寻找被盗或丢失的零件,以追踪黑市转售活动。
- 制定全球安全认证适用于处理高价值部件的航空员工。
机场和维修设施还必须加强背景调查并建立举报人保护措施,以鼓励员工举报可疑活动。
利用技术加强问责
人工智能和自动化在预防欺诈方面发挥着越来越重要的作用。行业领导者应该投资于:
- 人工智能驱动的欺诈检测系统分析交易数据是否存在异常。
- 自动库存审计使用机器学习来标记不一致之处。
- 安全的数字记录创建透明、防篡改的零件移动日志。
正如麦肯锡2024年6月报告所述,库存过剩可能是一种负担,但过度削减库存则会增加供应链中断的风险。人工智能驱动的预测模型可以帮助平衡库存水平,同时确保安全性和合规性。
Whether it’s missing engines, unauthorized part removals, or supply chain mismanagement, shrinkage leads to grounded aircraft, disrupted operations, and legal battles.
防止航空业库存萎缩
库存缩水不仅仅是一个会计问题,它直接威胁着运营效率、财务稳定和行业信任。无论是航空公司被指控剥离租赁飞机,内部威胁走私贵重部件,还是供应链漏洞导致库存错置,航空业都必须采取积极主动的措施来减少损失。
主要策略包括:
- 加强安全协议通过 RFID 跟踪、AI 监控和基于区块链的资产管理。
- 加强内部审计和问责防止内部欺诈和未经授权的零件拆除。
- 鼓励全行业合作改善库存收缩趋势的报告和情报共享。
- 利用人工智能和自动化创建更准确的库存管理系统并防止财务损失。
防止库存缩水对每个人都有利
库存缩减不仅仅关乎克服组织的财务和运营挑战(这足以成为加强安全的理由),还关乎保护整个航空生态系统的安全。
加强安全协议和改善库存管理可以保护企业免受财务损失,同时保护员工安全,使用未经剥离的经过认证的部件来提高飞机的飞行质量,并有助于全球安全。
减少盗窃和欺诈行为的公司正在保护其员工——尤其是那些从事低薪、高风险工作的员工——否则他们可能会被犯罪网络剥削。更安全、更透明的库存系统可确保关键航空部件存放在其所属位置,从而避免代价高昂的短缺,并消除不必要的资源浪费。
除了经济效益之外,解决损耗问题对全球安全也具有深远的影响。当飞机部件得到追踪和记录时,被篡改的风险就会降低,从而确保飞行安全。当非法货物无法通过航空渠道运输时,供应链就能保持安全,毒品走私等非法活动也会变得更加难以实施。
简而言之,防止库存缩水的意义远不止于保护发动机和航空电子设备部件。从地面工作人员到空中航空公司,每个利益相关者都能受益于一个以问责制、安全性和效率为优先考量的系统。航空业的未来取决于更智能、更安全的库存管理,现在投资这些系统的人将在运营稳定性、成本节约和长期信任方面获得回报。
在库存缩水导致您的车队停飞之前,应对库存缩水。使用 ePlaneAI 预约通话了解我们的 AI、区块链和 RFID 解决方案如何帮助您防止盗窃、追踪高价值部件以及端到端保护您的航空供应链。
航空维修趋势可能在不确定的情况下获得动力
飞机的服役时间越来越长,供应链如同火药桶,技术也在一夜之间不断革新。探索日益增长的维护趋势,以及它们对于努力保持飞行和盈利的运营商的意义。
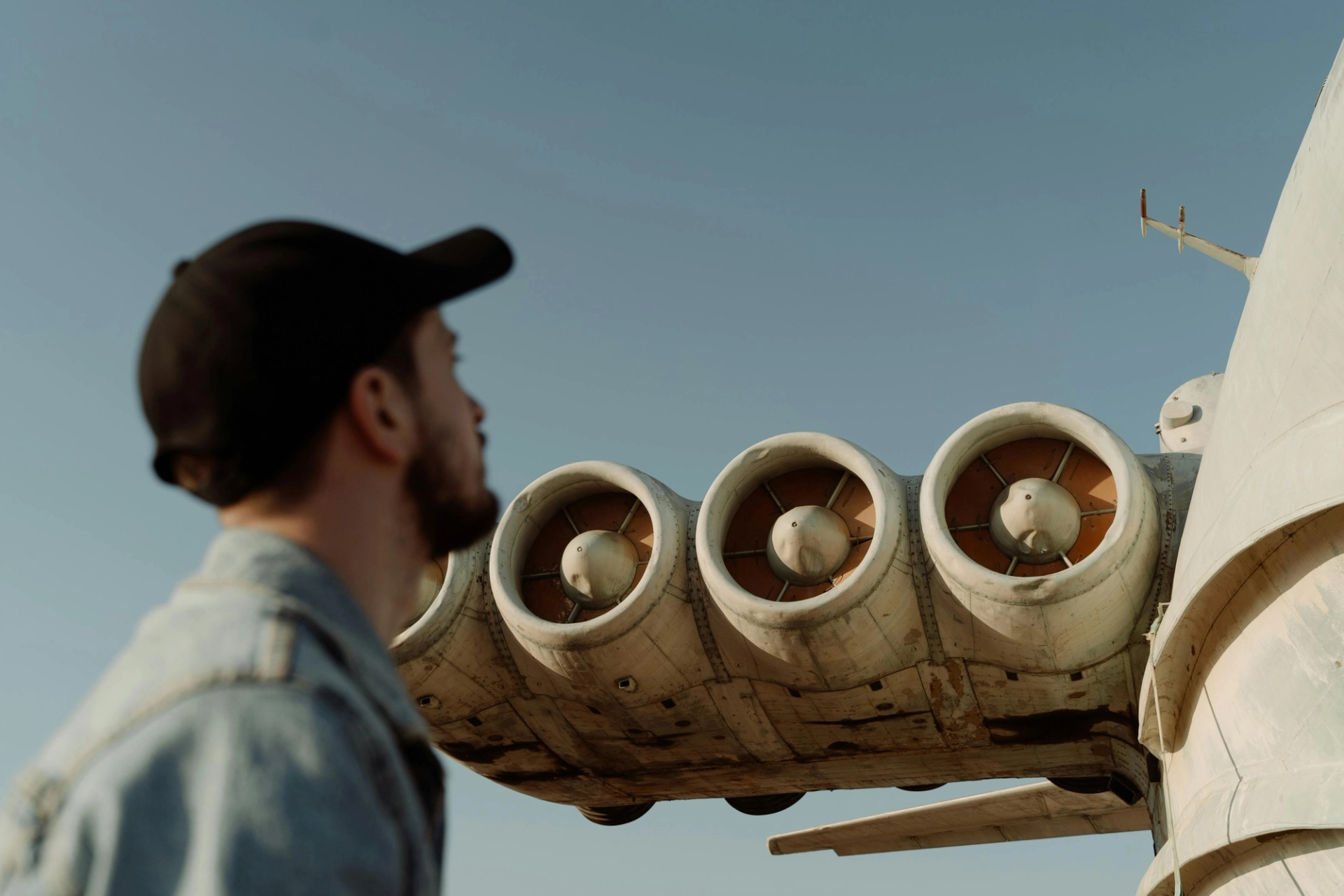
August 18, 2025
如何利用人工智能驱动的支出分析精简航空采购成本
采购延误给航空公司带来数百万美元的损失。了解 AI 驱动的支出分析如何帮助航空团队削减成本、避免缺货,并通过快速清晰的洞察进行更明智的谈判。了解如何开始使用。
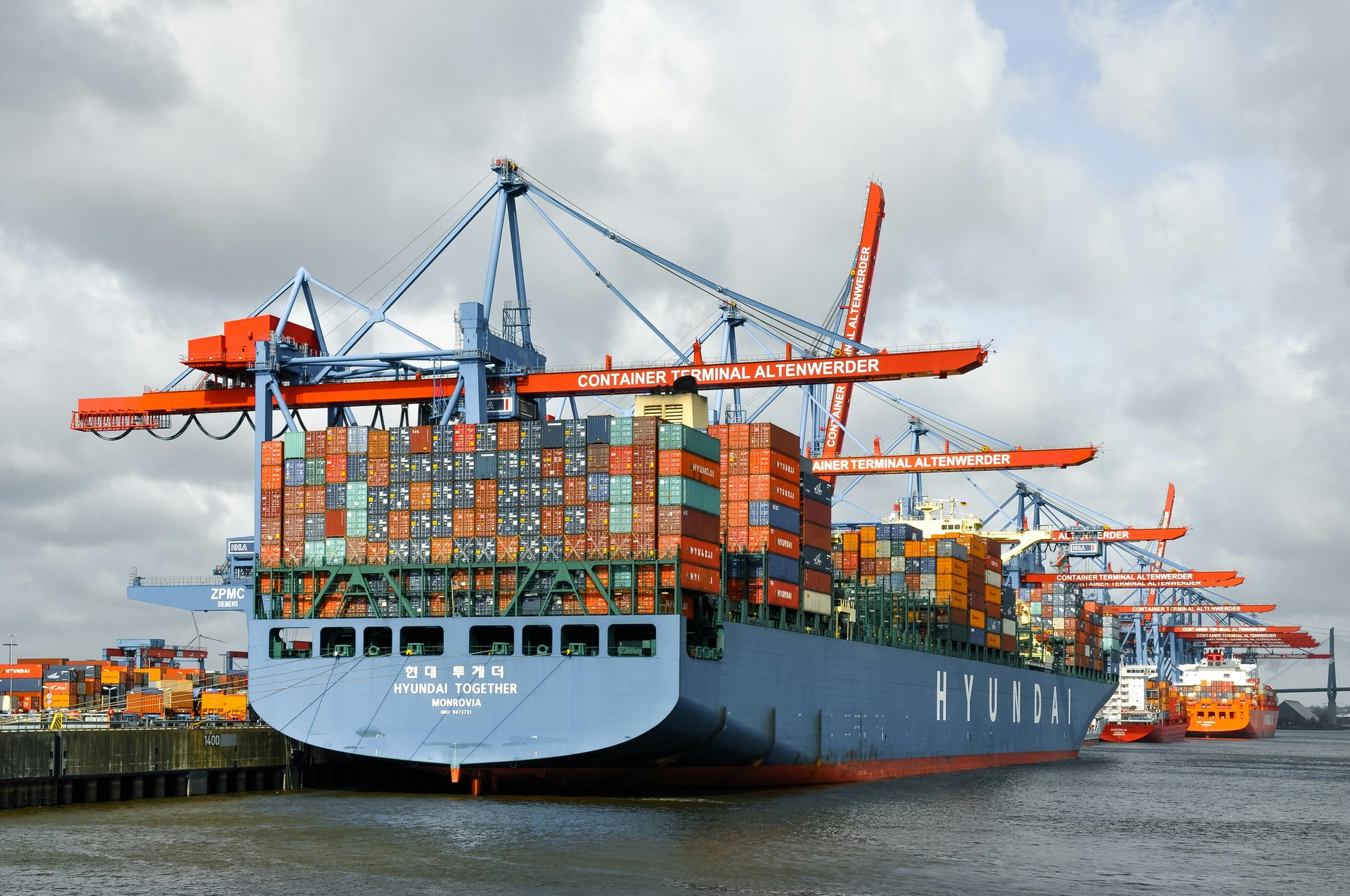
August 15, 2025
航空业采用精益制造的利与弊
精益制造可以提高航空业的效率并降低成本,但并非总是完美无缺。本文将深入探讨哪些方法有效,哪些无效,以及领先的航空航天公司如何运用精益制造来应对现实世界的复杂性。
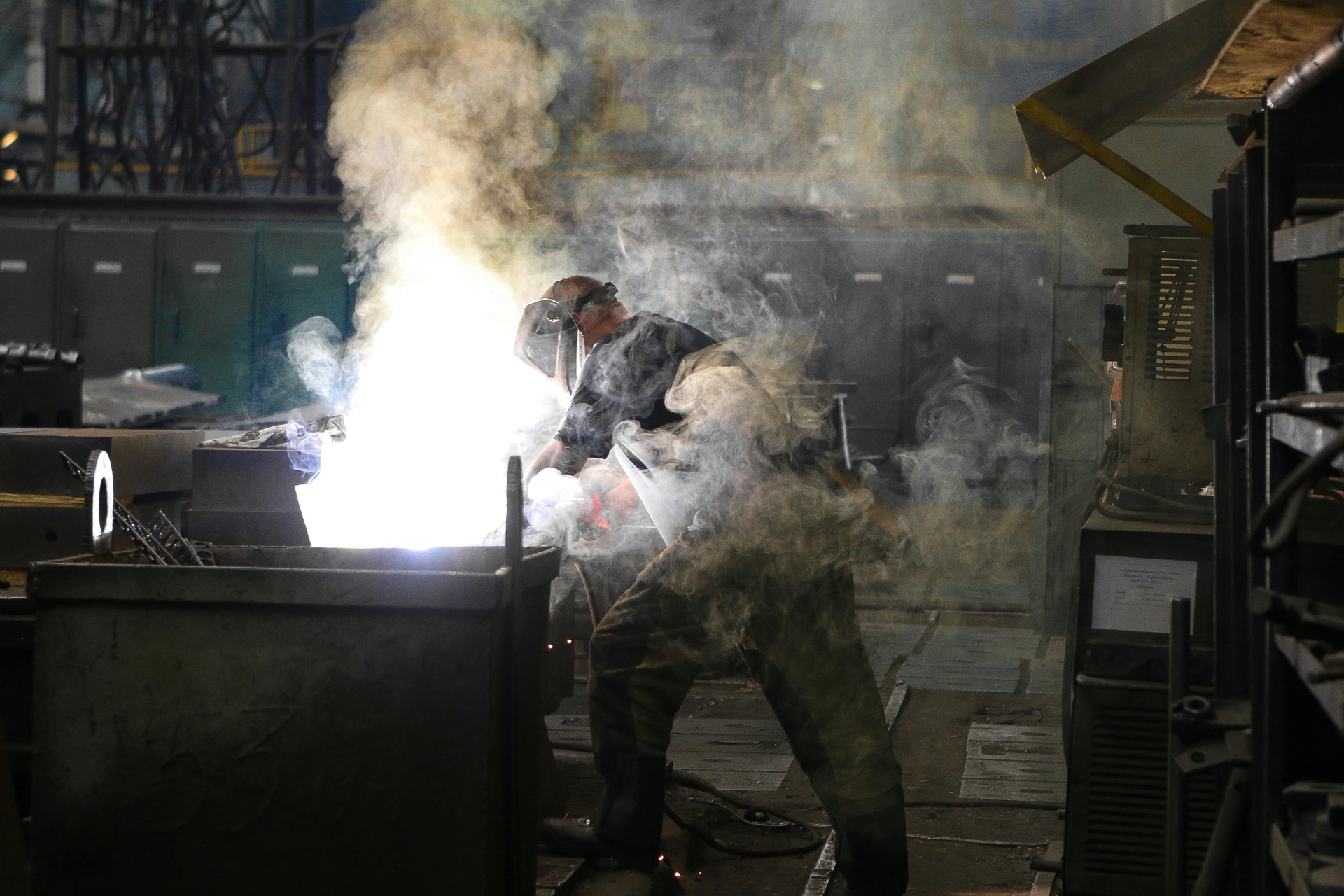
August 13, 2025
航空原始设备制造商如何利用数字孪生优化制造
数字孪生正在改变航空原始设备制造商(OEM)设计、制造和维护飞机的方式。以下是空客、劳斯莱斯和贝尔等领先企业如何利用数字孪生优化制造和运营。
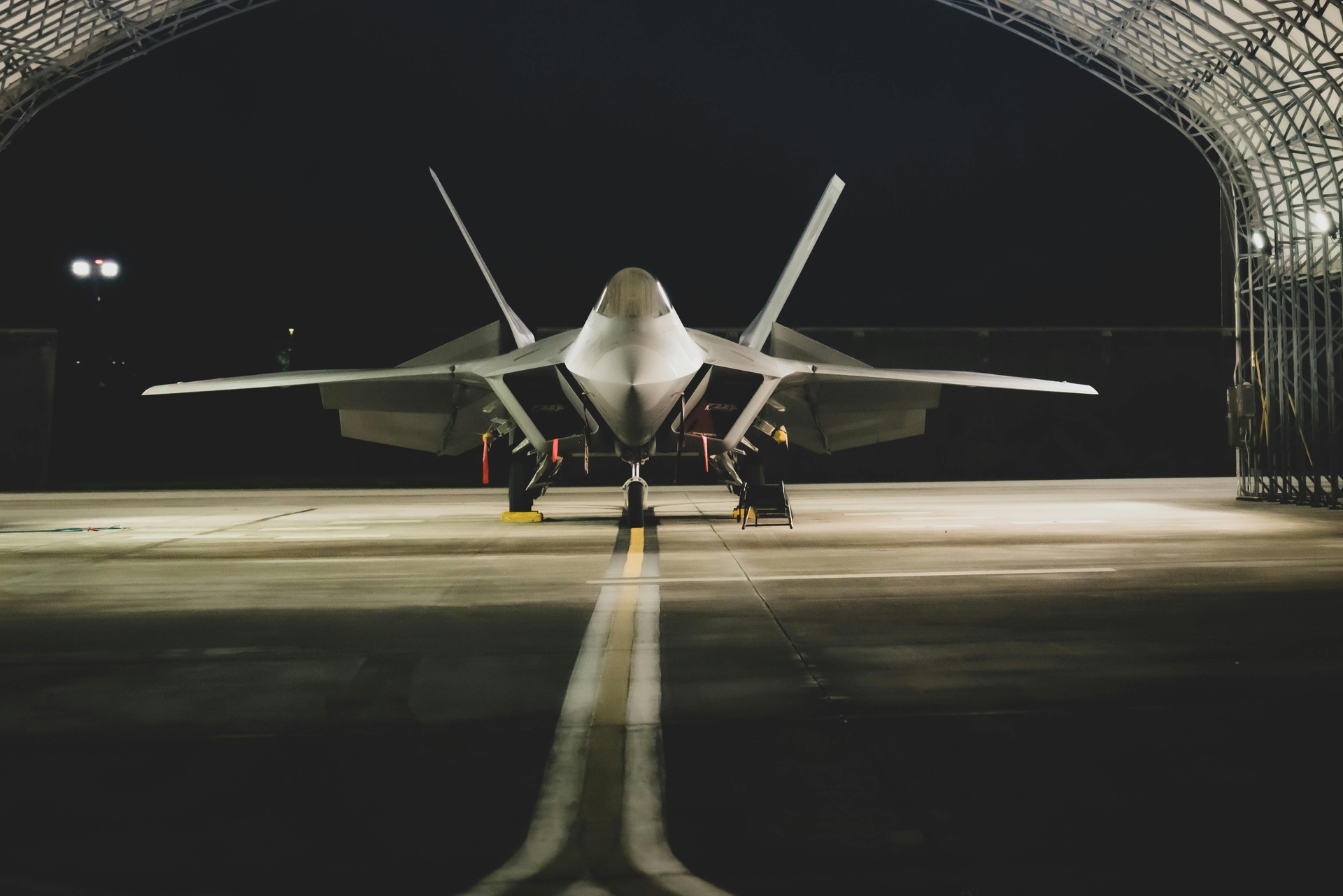